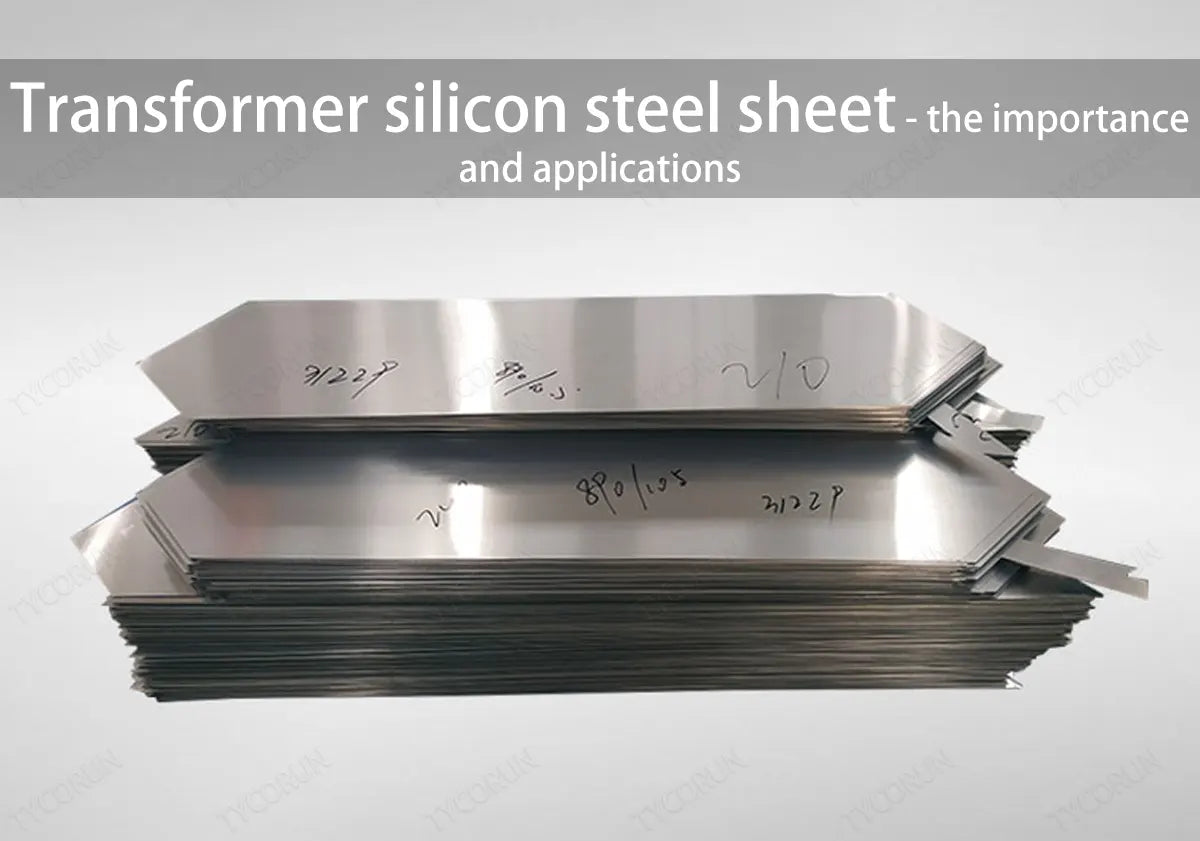
Unlike 2000w inverter or 3000w inverter, which invert direct current to alternating current, electronic transformer is a kind of device that can transfer the alternating voltage of the utility into direct current and then constitute a high-frequency alternating current voltage output through the semiconductor switching devices and electronic components and high-frequency transformer windings.
So it is a kind of AC-DC-AC converting circuit. Simply put, it is mainly composed of a high-frequency transformer core (iron core) and two or more coils. Commonly used transformer cores are generally made of silicon steel sheets. Silicon steel is a kind of steel containing silicon, and its silicon content ranges from 0.8 to 4.8%.
Silicon steel is used as the core of the transformer because silicon steel itself is a magnetic material with strong magnetic p ermeability. With the development of PCS technology, in the energized coil, it can produce a large magnetic induction intensity, thereby reducing the size of the transformer.
Main content:
1. The power loss of transformer
The transformer always works in the AC state, and the power loss is not only in the resistance of the coil, but also in the iron core magnetized by the alternating current. The power loss in the iron core is usually called "iron loss". Iron loss is caused by two reasons, one is hysteresis loss, and the other is eddy current loss.
Hysteresis loss is the iron loss caused by the hysteresis phenomenon during the magnetization process of the iron core. The size of this loss is proportional to the area surrounded by the hysteresis loop of the material. The hysteresis loop of silicon steel is narrow, and the hysteresis loss of the core of a transformer made of silicon steel is small, which can greatly reduce the heat generation.
Since silicon steel has the advantages above, why not use a whole piece of silicon steel as the iron core but process it into sheets? This is because the sheet core can reduce another type of iron loss - eddy current loss.
2. What is eddy current loss?
When the transformer is working, there is alternating current in the coil, and the magnetic flux it generates is also alternating. This changing magnetic flux produces an induced current in the iron core. The induced current generated in the iron core circulates in a plane perpendicular to the direction of the magnetic flux, so it is called eddy current.
Eddy current losses also heat the core. In order to reduce eddy current losses, the core of the transformer is stacked with silicon steel sheets that are insulated from each other, so that the eddy currents pass through a smaller cross-section in a long and narrow circuit to increase the resistance on the eddy current paths; at the same time, the silicon in the silicon steel increased the resistivity of the material, which also plays a role in reducing eddy currents.
For the iron core of the transformer, 0.35mm cold-rolled silicon steel sheet is generally used. It is cut into long pieces according to the required size of the iron core, and then overlapped into a shape like the picture below. Theoretically, in order to reduce eddy currents, the thinner the silicon steel sheets and the narrower the spliced sheets, the better the effect. This not only reduces eddy current losses and temperature rise, but also saves materials for silicon steel sheets.
But when actually making silicon steel cores. It is not just based on the above-mentioned favorable factors, because making the iron core in that way will greatly increase the manufacturing hours and also reduce the effective cross-section of the iron core. Therefore, when using silicon steel sheets to make transformer cores, you must start from the specific situation, consider the pros and cons, and choose the best size.
Transformers are made based on the principle of electromagnetic induction. There are two windings wound on the closed iron core column, a primary winding and a secondary winding. When the original winding is connected to the AC power supply voltage. There is an alternating current flowing through the original component, and a magnetic potential is established. Under the action of the magnetic potential, an alternating main magnetic flux is generated in the iron core.
So why can it boost and reduce the voltage? We’ll need to use Lenz's law to explain it. The magnetic flux generated by the induced current always hinders the change of the circular magnetic flux. When the original magnetic flux increases, the magnetic flux generated by the induced current is opposite to the original magnetic flux, that is to say, the secondary magnetic flux.
The induced magnetic flux generated by the winding is opposite to the main magnetic flux generated by the primary winding, so a low-level alternating voltage appears in the secondary winding. Therefore, the iron core is the magnetic circuit part of the transformer.
3. Performance parameters of silicon steel sheet
- Low iron loss: The most important indicator of quality, the iron loss value is commonly used around the world to classify the grades. The lower the iron loss, the higher the quality.
- High magnetic induction intensity: Silicon steel sheets can obtain higher magnetic induction under the same magnetic field. The size and weight of the motor or transformer core made with it are relatively small, which can save silicon steel sheets, copper wires and insulating materials.
- High stacking coefficient: The surface of the silicon steel sheet is smooth, flat and uniform in thickness, and the stacking coefficient of the core is improved.
- Good film processing properties: This is even more important for manufacturing small and micro motor cores.
- Good adhesion and weldability between the surface and the insulating film.
- Good magnetic aging.
- Silicon steel sheets must be annealed and pickled before delivery.
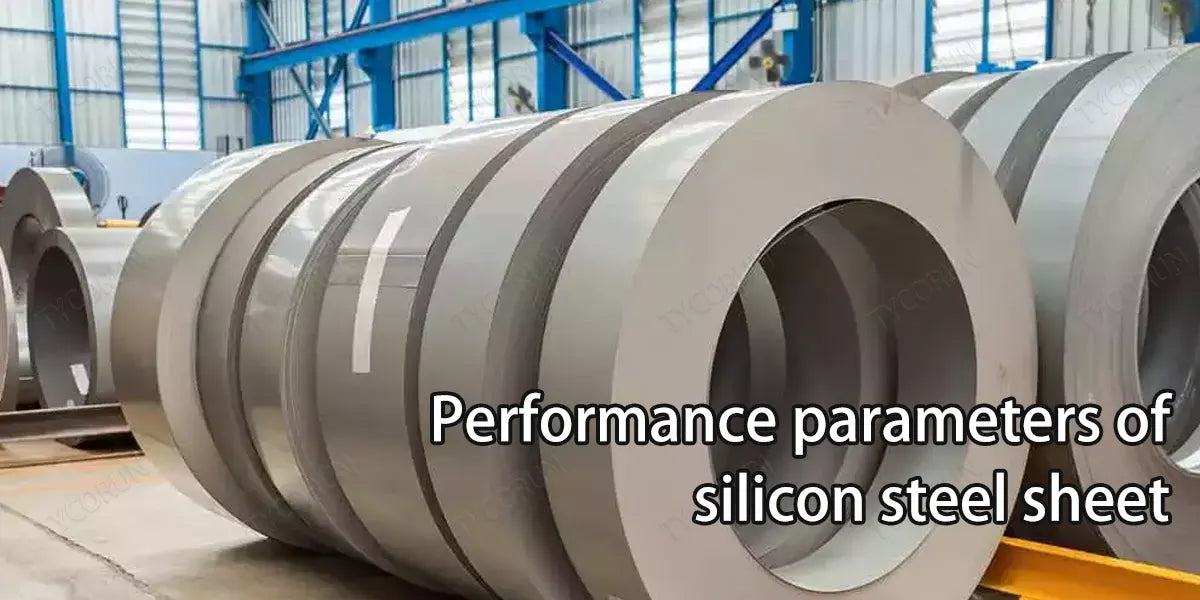
4. Classification of silicon steel sheet
Silicon steel sheets for electrical purposes are commonly known as silicon steel sheets or silicon steel sheets. As the name suggests, it is electrical silicon steel with a silicon content of up to 0.8%-4.8%, which is made by hot and cold rolling.
Generally, the thickness is less than 1mm, so it is called thin plate. Silicon steel sheets belong to the plate category and are an independent branch due to their special uses. Silicon steel sheets for electrical purposes have excellent electromagnetic properties and are indispensable and important magnetic materials in the power, telecommunications and instrument industries.
There are mainly two kinds of classifications of silicon steel sheets:
- Silicon steel sheets can be divided into low silicon and high silicon according to their silicon content. Low silicon wafers contain less than 2.8% silicon.
- According to the production and processing technology, it can be divided into hot rolling and cold rolling.
Cold rolling can be divided into two types: grain non-oriented and grain oriented. Cold-rolled sheets have uniform thickness, good surface quality, and high magnetic properties. Therefore, with the development of industry, hot-rolled sheets have a tendency to be replaced by cold-rolled sheets.
5. Application scenarios for silicon steel sheet
- Hot-rolled silicon steel sheet for electrical purposes (GB5212-85)
Hot-rolled silicon steel sheets for electrical purposes are made of ferrosilicon soft magnetic alloy with low carbon loss, and are hot-rolled into sheets with a thickness of less than 1mm. Hot-rolled silicon steel sheets can be divided into low silicon (Si≤2.8%) and high silicon (Si≤4.8%) steel sheets according to their silicon content.
- Cold-rolled silicon steel sheet for electrical purposes (GB2521-88)
This kind of silicon steel sheet is made of electrical silicon steel containing 0.8%-4.8% silicon and is made by cold rolling. Cold-rolled silicon steel sheets are divided into two types: grain-non-oriented and grain-oriented steel sheets. Cold-rolled electrical steel sheet has the characteristics of smooth surface, uniform thickness, high stacking coefficient, and good punching performance.
It has higher magnetic induction and lower iron loss than hot-rolled electrical steel sheets. Using cold-rolled sheets instead of hot-rolled sheets to manufacture motors or transformers can reduce its weight and volume by 0%-25%. If cold-rolled oriented sheet is used, the performance will be better. Using it instead of hot-rolled sheet or low-grade cold-rolled sheet can reduce the power consumption of the transformer by 45%-50%, and the transformer performance will be more reliable.
Generally, grain-non-oriented cold-rolled strips are used as motors or welding transformers, etc.; grain-oriented cold-rolled strips are used as iron cores for power transformers, pulse transformers, magnetic amplifiers, etc. Steel plate specifications and dimensions: thickness is 0.35mm, 0.50mm, 0.65mm, width is 800-1000mm, length is≤2.0m.
- Hot-rolled silicon steel sheet for home appliances (GBH46002-90)
The grade of hot-rolled silicon steel sheet for home appliances or home solar power system is represented by JDR. The number after JDR is the iron loss value *100, and the number after the horizontal line is the steel plate thickness (mm) * 100.
Hot-rolled silicon steel sheets for home appliances can have slightly lower electromagnetic performance requirements, and the minimum iron loss value (P15/50) is 5.40W/kg. Generally delivered without washing. This kind of silicon steel sheets are used on differential motors used in electric fans, washing machines, vacuum cleaners, range hoods and other household appliances.
Related posts: pure sine wave vs modified sine wave inverter, inverter and battery shop near me, top 10 power conversion system companies