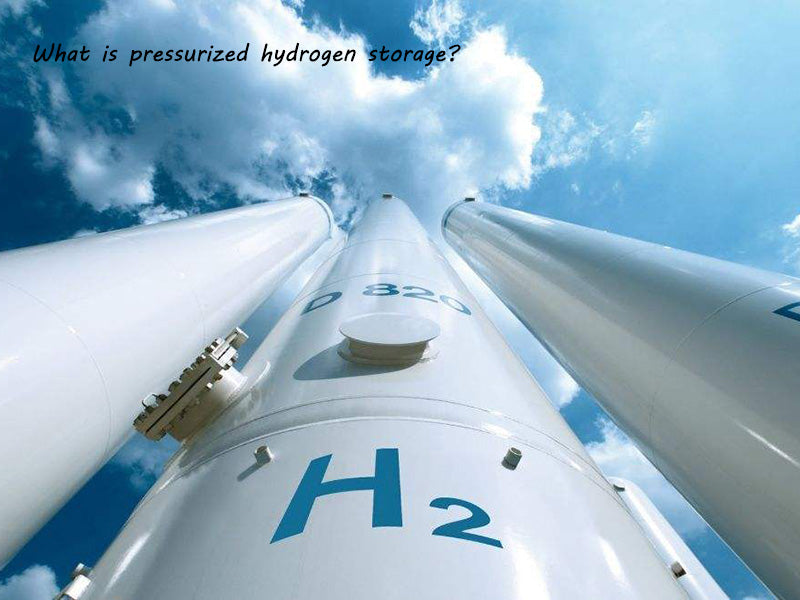
Main content:
1.Introduction to hydrogen storage
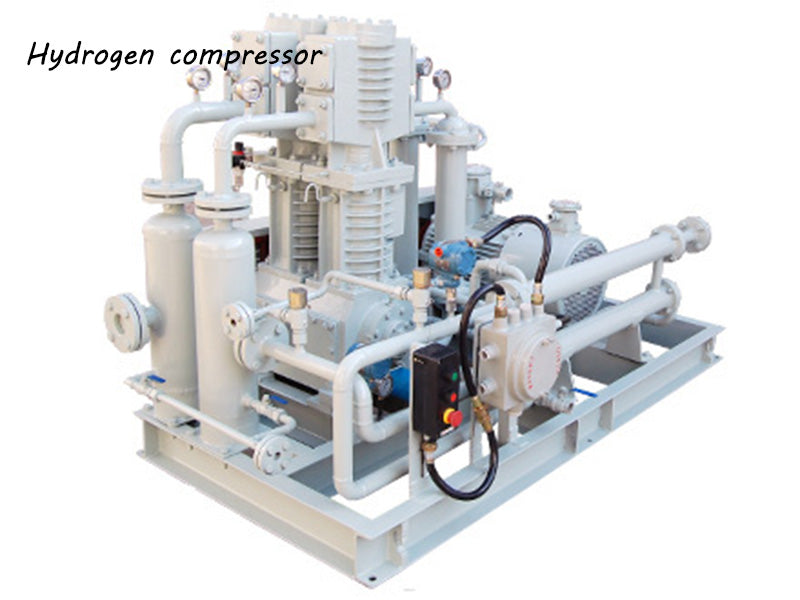
Pressure hydrogen storage is a technology that has been proven by the industry for many years. It uses steel pipes (about 10N m3) under 200bar pressure to distribute regassing. However, it is foreseeable that it is not an economical way to distribute huge amounts of hydrogen with traditional steel pipes and ground transportation. Therefore, research institutes in many countries and the world's leading gas production and distribution companies have begun to develop special containers for transportation applications, divided into 350bar and 700bar.
The technical solutions of these storage and recovery vessels for pressure hydrogen storage are consistent, including:
1) The housing has a high mechanical resistance to corrosive environments (such as acids) and is at the same time very light; made of high-quality carbon fiber reinforced synthetics.
2) The inner shell, or "liner", is made of polymer or light metal (such as aluminum); this is the best material in terms of water tightness or air tightness. In order to develop the specifications, numerous resistance and safety tests have been carried out on the material properties, especially the mechanical properties and blasting properties.
From the energy point of view, the use of pressure hydrogen storage has good economics, because the pressure storage hydrogen to 350bar and 700bar respectively consumes only 9% and 13% of the stored energy in theory. However, pressurizing the container implies an increase in the internal temperature of the gas during rapid compression, which must be taken into account. Therefore, when designing the container, the mechanical properties of the materials used must be considered at temperatures above 200°C. Adding liquid ammonia to cool gaseous hydrogen in the rapid storage and recovery process is a solution to the temperature rise.
At present, in order to achieve the 500-kilometer battery life of electric vehicles, lithium-ion batteries and fuel cells can be used as the energy power of vehicles,the storage and recovery container of vehicles using fuel cells (FC) must have a capacity of at least 125L; while vehicles using internal combustion engines (ICE) must have a capacity of at least 250L. The volume of the container housing and auxiliary systems has not been taken into account. From an economic point of view, in the next ten years, under the premise of mass production of pressure hydrogen storage containers for vehicles, the estimated unit cost should be less than 60 euros, and the recycling of composite materials for making shells The cost needs to be further determined.
In stationary applications, high-capacity units for storing high-pressure (50-180 bar) regassing have been developed, primarily to meet the needs of hydrogen production and distribution companies. Usually cylindrical structures (eg 4500 m3, about 20 m long, 50 bar pressure), or spherical structures are used. In order to reduce the risk, EU standards are devoted to storage and recovery devices with a pressure of less than 50 bar and a maximum volume of 350 m3, which can store 400 kg of hydrogen.
2.Network distribution of pressure hydrogen storage
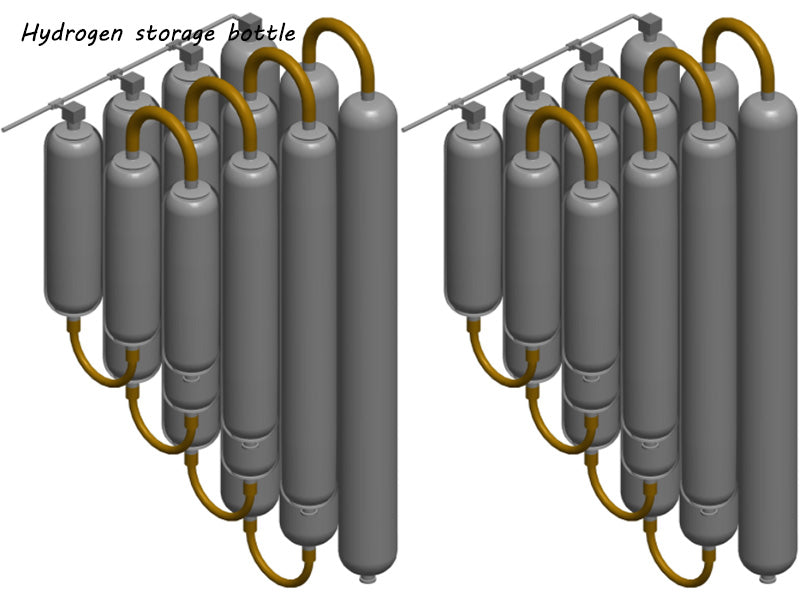
Low-pressure pipelines are used for industrial reuse. The most influential pressure hydrogen storage distribution network in the world is the pipeline network between France, Germany, Belgium and the Netherlands. This pipeline network constitutes a moderate-capacity "storage container" that acts as a buffer between intermittent energy (eg wind, photovoltaic, etc.) replication and short-term (24-72h) hydrogen consumption.
In addition to pressure hydrogen storage, for underground hydrogen storage, large-scale practical tests have been carried out in France, Germany, the United Kingdom and the United States (the maximum volume exceeds 3 × 108m3). Finding leak-tight underground caverns is an important task, as in some cases less than 50 percent of the injected gas is recovered.