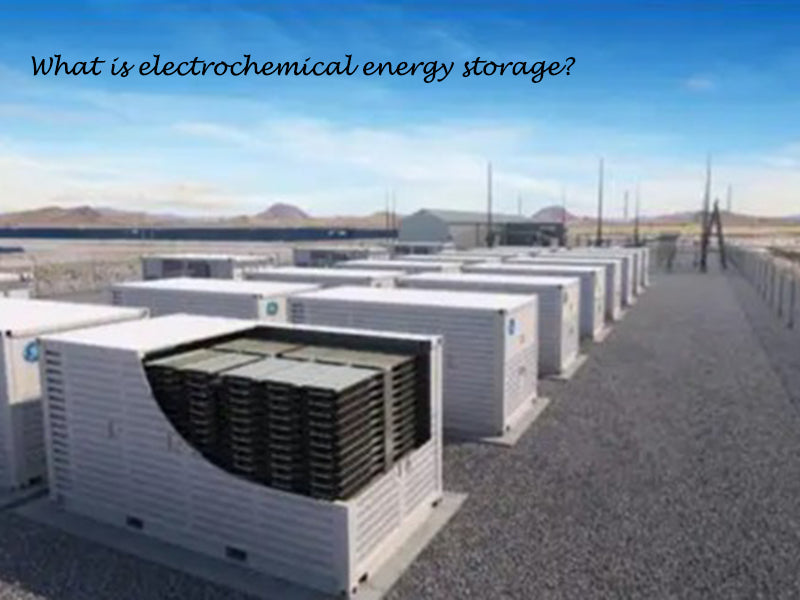
Main content:
Electrochemical energy storage can be divided into three categories: primary batteries, secondary batteries, and fuel cells. There is a lot of literature on how to miniaturize them, and we can also integrate them on silicon, which is currently being done in many labs. The figure below provides a comparative analysis of various electrochemical energy storage technologies.
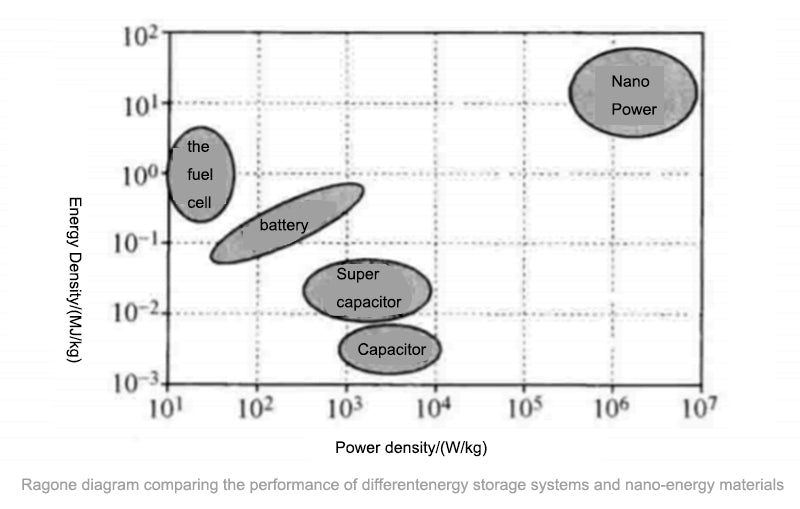
1.Primary battery electrochemical energy storage
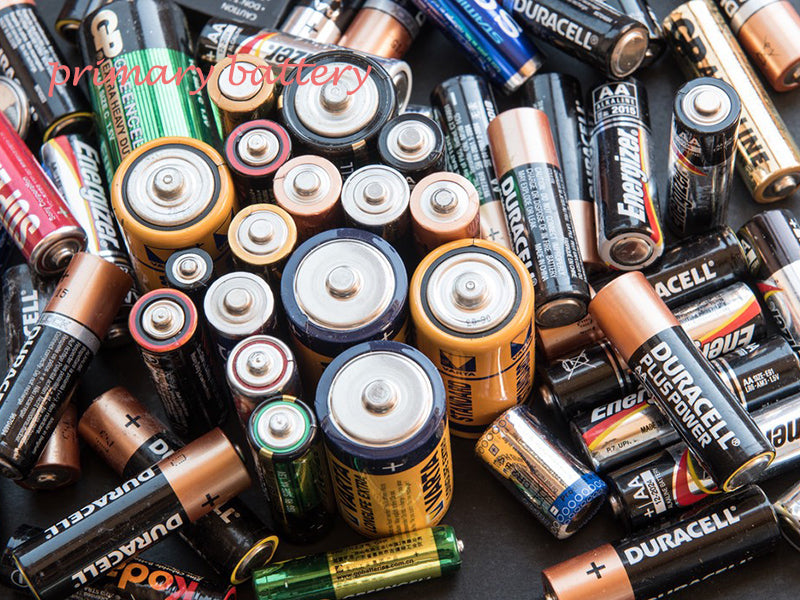
Primary batteries offer a great solution for electrochemical energy storage when recharging is not required. Alkaline dry batteries, widely used by the public, have an energy density comparable to the best nickel-metal hydride batteries. For zinc-air batteries, the available energy density is almost three times higher than that of lithium polymer batteries. The figure below shows the specific energy ranking of primary cells that can be obtained by different miniaturization techniques.
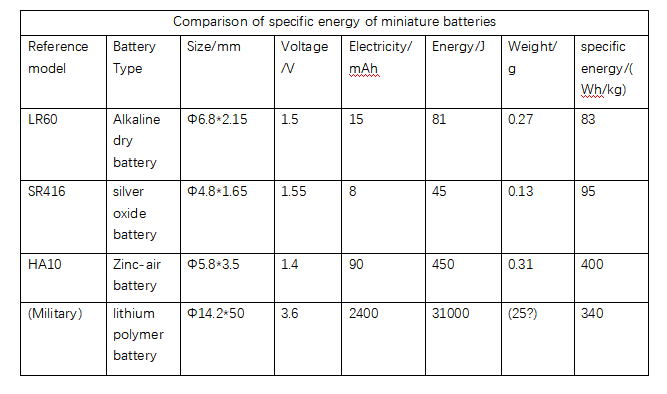
2.Battery electrochemical energy storage
For mobile applications of battery electrochemical energy storage, it is easier to judge the rationality of the use of high-performance batteries through economy.
A 130g iPhone was priced at 800 euros (excluding user network charges) in early 2009, reaching 6,000 euros/kg. An 850kg Renault car was priced at 7,000 euros in the same period, or 8 euros/kg. For the former, lithium polymer batteries are the best choice for electrochemical energy storage, while for the latter, it is best to choose cheap lead-acid batteries for starting batteries.
The chart below summarizes these batteries in order of performance.
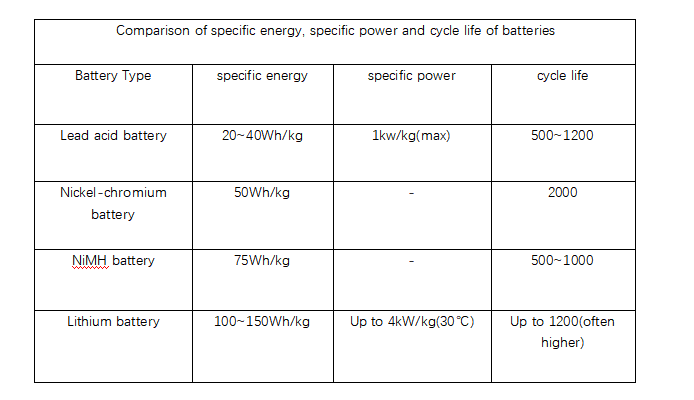
In micro-miniature system applications, the manufacturing techniques of batteries differ from those of conventional techniques.
The miniaturization of batteries, and how to integrate them on silicon wafers, is a research hotspot. Its main goal is to directly connect the battery with its associated circuitry on the same substrate.
To achieve this goal, two technical routes are currently being explored: the first is to assemble the battery on a flexible substrate and then place it on the electronic device; the second is to use the deposition method, directly on the silicon wafer. Make batteries.
The capacity of lithium battery integrated with silicon wafer can reach 100 ~ 400μA h/cm2, and the voltage is 3.8V. These cells can provide a maximum current density of 15mA/cm2 and can be cycled more than 10,000 times (data from the French Atomic Energy Agency CEA).
In addition to planar layered processing techniques, these microbatteries currently have a comparable area of coverage on the exchange surface and substrate where the reactions occur. In order to improve the battery performance, the researchers made full use of the third dimension in the subsequent battery fabrication, placing the reaction layer in a "mini accordion" fashion, hoping to increase the exchange surface by 10 times, and the battery performance can be correspondingly increased by 10 times.
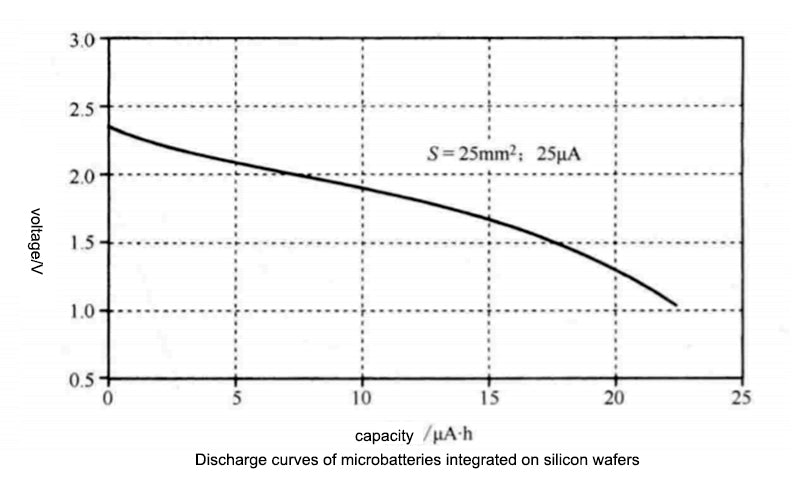
While studying compressed nanopowders and composite electrodes, researchers at the Massachusetts Institute of Technology (MIT) found that by improving ion exchange technology, the discharge time of the battery can be increased to 10~20s (temperature controlled at 200~400℃). Such performance metrics enable lithium-polymer batteries to have discharge rates comparable to supercapacitors.
3.Fuel cell electrochemical energy storage
energy storage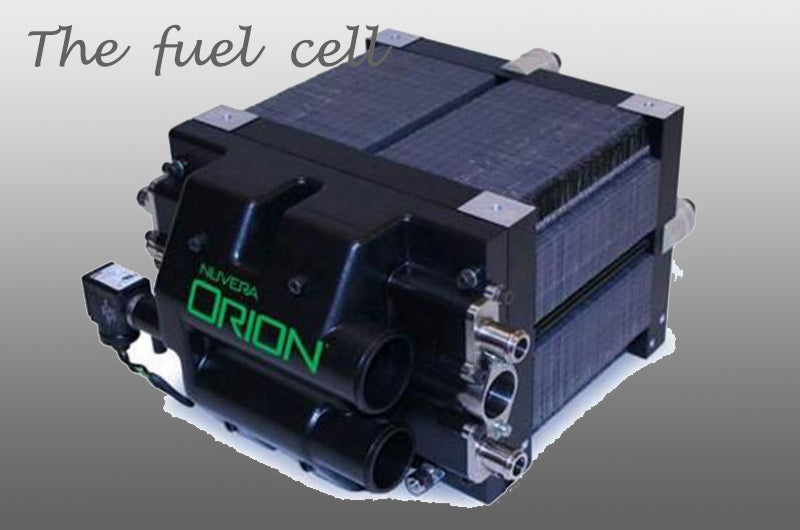
Fuel cell electrochemical energy storage provides an attractive solution for some special on-board energy supplies. The Fraunhofer Institute for Reliability and Microintegration in Germany and the Technical University of Berlin have jointly developed a system that can provide 12W of power. , Fuel cells weighing 30g. But such high power density (400W/kg) fuel cells have not yet been achieved in systems above a few hundred grams.
Other research institutes in this field are the French Atomic Energy Agency (CEA, Grenoble, France), the French Institute of Electronics, Microelectronics and Nanotechnology (IEMN, Lille, France), and the University of Sherbrooke. In addition, the University of Vancouver and the University of California, Berkeley are also collaborating on the research and development of related technologies.
Mobile applications are a potential market for fuel cells, but the current popularity of high-power fuel cells (traffic or household) is constrained by the availability and price of materials (metal platinum and proton exchange membranes). Low-power or low-power fuel cells require less material than high-power fuel cells, but their cost is comparable to today's very expensive batteries.
The French company Paxitech produces fuel cells that meet the needs of many different mobile applications. A fuel cell unit has a mass of 500g and can output 20W of power. This fuel cell power generation unit needs to be connected with a storage and recovery device, and the metal hydride storage and recovery device can make the specific energy of the fuel cell power generation system reach 160 ~ 180W·h/kg. However, experimental studies have shown that if hydrogen is stored in chemical complexes, specific energies of 600–800 W h/kg can be obtained, which is more than four times higher than the current state-of-the-art batteries.
The above three kinds of electrochemical energy storage have their advantages and disadvantages, but the future market prospect of electrochemical energy storage will be more inclined to more environmentally friendly electrochemical energy storage technology and deeper electrochemical energy storage performance.