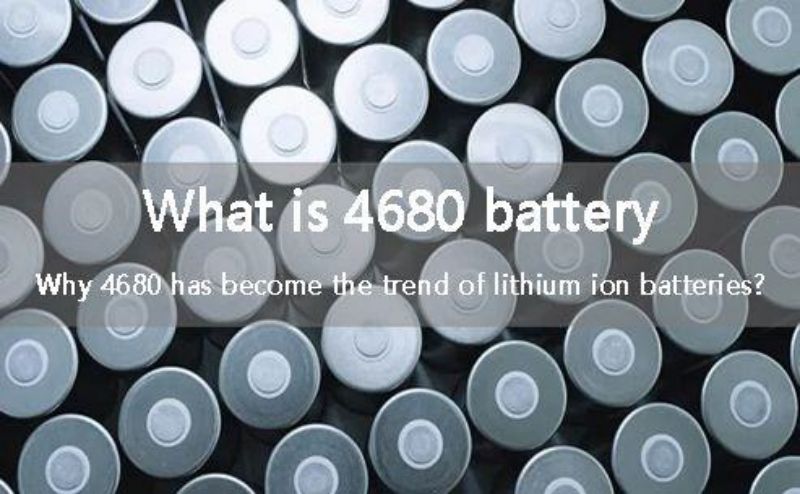
Main content:
-
1.The trend of large cell is clear, and the prospect of large cylindrical route is promising
- 1.1 18650→21700→4680, the trend of cylindrical battery large-size is clear
- 1.2 Cylinder battery has obvious advantages in consistency, safety and material application
- 1.3 The high group efficiency, low BMS difficulty and high voltage platform adaptability of the 4680 battery make it has a promising route
- 2.Battery link: Battery manufacturers layout 4680 battery, and the multiple advantages of 4680 battery help increase the cylinder share
-
3.Material link: The demand for large cylindrical batteries increases, improving greatly the application potential of high energy density materials
- 3.1 High nickel cathode: high nickel expansion peaks and and the integrated layout creates the high nickel cathode material leader
- 3.2 Silicon-based anode: The demand for silicon-based anode is upward, and the commercialization process is expected to accelerate
- 3.3 LiFSI: 4680 battery drives the demand of LiFSI to increase, and the large-scale layout of China enterprises accelerates
- 3.4 Carbon nanotubes: 4680 battery helps improve the permeability of carbon nanotubes
- 4.Structural parts: 4680 battery demand increase, open the incremental space of cylinder structural parts
- 5. Investment analysis
1.The trend of large cell is clear, and the prospect of 4680 bttery route is promising
1.1 18650→21700→4680, the trend of cylindrical battery large-size is clear
Power battery according to the different packaging form, mainly divided into cylindrical battery, square battery and pouch battery.Among the three forms of batteries, the cylindrical battery is coiled by one end of the cathode, diaphragm and negative and packaged in the cylindrical metal shell; the square battery is made by winding or lamination, the winding process usually has two axles, the positive, diaphragm and negative laminated around the two axes, and then loaded directly into the square aluminum shell; the soft pack battery is a typical "sandwich" stack structure, stacked by positive sheet, diaphragm and negative sheet, and wrapped with aluminum plastic film. Cylinder batteries have the longest development time, the most mature technology, and a high degree of standardization.The earliest cylindrical battery was an 18650 lithium battery invented by SONY in 1992.18 is a diameter of 18 m m, 65 is 65mm and 0 is a cylindrical battery.Due to the long history of 18650 cylindrical battery, so the market penetration rate is high, it is the most common battery model on the market, and is widely used in the consumer electronics field.
Because the technology of cylindrical batteries is the most mature and consistent, Tesla has introduced cylindrical batteries into the field of power batteries.In 2008, Tesla first used Panasonic's 18650 cylindrical battery cell as the vehicle's power battery, and after testing it on Roadster, it began to use it on a large scale on Model S.To improve the energy density of the cell and reduce costs, Tesla launched the 21700 lithium ion battery jointly developed with Panasonic in 2017, and applied the battery in the Model 3 model.The 21700 cylindrical battery is 21mm in diameter and 70mm long, and the battery energy is 50% higher than the 18650 cylindrical battery.In 2019, Tesla applied for 4680 cylinder patent, and 4680 cylindrical battery day in 2020,4680 cylinder using lug, new silicon material and cobalt free technology, the performance of 21700 cylindrical battery, it is expected that 4680 cylindrical battery energy will increase 5 times, range increase 16%, power increase 6 times.
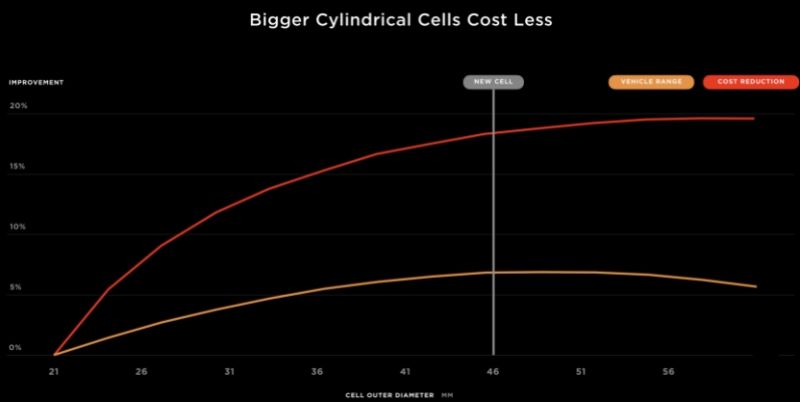
Large cylindrical batteries have the advantage of low cost
Compared with small cylindrical batteries, large cylindrical batteries have the advantages of high energy density and low cost.The size of the cylindrical battery was upgraded from 21700 to 4680 battery, and the cell volume increased by 448%, while the surface area only increased by 180%, which indicates that as the diameter of the cylindrical battery increases, the proportion of the structural mass to the total weight of the battery pack decreases, and the battery energy density of the large cylindrical battery will increase, thus reducing the production cost of the battery per Wh.Upgrading from 21700 cylindrical battery to 4680 large cylinder can reduce the unit production cost by 14%.Large-scale cell is one of the important means for Tesla to reduce costs and increase efficiency, and the trend of cylindrical battery is clear.
1.2 Cylinder battery has obvious advantages in consistency, safety and material application
Cylinder battery manufacturing process is relatively mature, with high production efficiency and high product consistency.Due to the long-term application of cylindrical batteries in nickel-metal hydride batteries and consumer electronics (3C) lithium-ion batteries, the industry has accumulated a lot of production and design experience, so there are relatively mature automatic production lines and equipment.In addition, the cylindrical battery is manufactured in the way of winding. The winding process can improve the production efficiency of the cell by accelerating the rotation speed, while the efficiency of the lamination process is limited, and the production efficiency of the cylindrical battery is higher.In the winding process, in order to ensure the high consistency of the battery assembled into the cell, the winding tension needs to be controlled. The tension fluctuation will make the winding cell produce uneven tensile deformation, seriously affecting the consistency of the product.At present, the tension fluctuation of domestic leading enterprises in cylindrical battery is controlled below 3%, and the mass-produced cylindrical battery products have high consistency.
Benefiting from the thermal runaway transmission blocking characteristics, good sealing and high product consistency, the cylindrical battery has obvious advantages in safety.Because square, soft pack battery has flat surface, the module rear plane is often in close contact, in thermal control, heat transfer, lateral direction, and cylindrical battery because of the arc surface, in full contact still exist large gap, to some extent, inhibit the heat transfer between the battery, so cylindrical battery can prevent the spread of thermal control to a certain extent. At the same time, due to the low energy of the cylindrical battery, it can reduce the total amount of energy released in the initial spread of thermal runaway, and cylindrical batteries are better sealing than lipo batteries, which is not easy to occur leakage phenomenon, so the cylindrical battery has obvious advantages in safety aspects.In addition, the high consistency of cylindrical batteries can avoid the risk of overcharging, overdischarge and local overheating caused by battery inconsistency to some extent.
Benefiting from the material mechanical properties of the cylindrical structure itself, the cylindrical battery is compatible with high nickel and silicon carbon anode materials and is inclusive for material applications.In order to improve the battery energy density, high nickel cathode materials and silicon carbon cathode materials are applied to the battery material system, but the poor thermal stability of high nickel materials and the high volume expansion rate of silicon carbon materials bring a test to the safety of power batteries.Compared with square battery and soft pack battery, cylindrical battery structure itself strength is higher, the tolerance of silicon carbon anode expansion is higher, and the thermal runaway propagation blocking characteristics of cylindrical battery can to some extent make up for the disadvantages of high nickel material thermal stability, so in the application of high nickel material and silicon carbon anode material, cylindrical battery advantage.
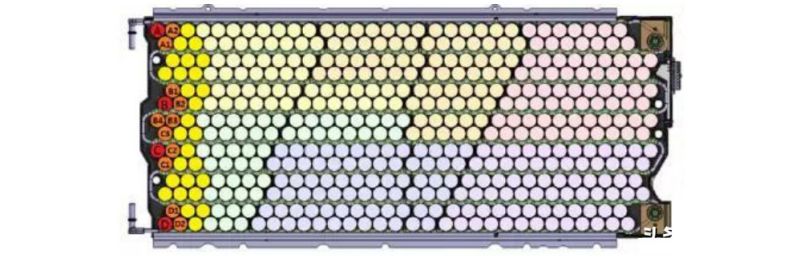
The arc surface of the cylinder inhibits the lateral heat transfer to some extent
1.3 The high group efficiency, low BMS difficulty and high voltage platform adaptability of the 4680 battery make it has a promising route
Large cylinder can improve the group efficiency and make up for the low efficiency of small cylinder battery group.According to the data of Juda lithium battery, the module group efficiency of cylindrical batteries in the industry is about 87%, the system group is about 65%, while square batteries are 89% and 70% respectively, and the module efficiency of cylindrical batteries is low.After the diameter of the cylindrical battery becomes larger, the aperture of the power battery support plate and the collector plate becomes larger, and the corresponding weight is reduced. In addition, the reduction of the number of cells in the power battery pack can reduce the amount of structural parts, and improve the group efficiency while improving the energy density of the battery.
cylindrical route has high requirements on BMS technology of automobile enterprises, and large cylindrical route can reduce the difficulty of BMS control.Single cylindrical cell capacity is small, to achieve a certain power performance, the need for a large number of cells.A 75KWh electric vehicle power battery pack needs about 700018650 batteries, even 21700 batteries also need 4400, high requirements for BMS, for the weak in the BMS field, and 4680 battery only need 950 batteries, the number of batteries required is significantly reduced, thus reducing the difficulty of BMS control.Therefore, the large cylindrical route can reduce the degree of technical dependence of car companies on midstream battery companies.
The 4680 battery no lug is designed to shorten the electronic transmission path, thus reducing the internal resistance.The lug is a metal conductor derived from the anode and cathode of the cell, which is the contact point of the battery when charging and discharging.Traditional cylindrical battery through single ear to realize the current collection, due to the existence of resistance, battery in the process of charge and discharge, especially in the process of large current charge and discharge will produce significant ohm, cause the rise of battery temperature, with the cell size, winding length is longer, will aggravate the internal current and temperature distribution, local high temperature in the lug.In order to reduce the internal resistance of the battery and reduce Ohmic heat during the charging and discharge process, Tesla uses lug technology for 4680 large cylindrical battery, that is, the whole fluid collection becomes lug, and the conductive path is no longer dependent on polar ear, so the lug technology is also called full lug technology.No lug technology changes the electron transmission path from lateral transmission along the lug to the collector disc to collector fluid longitudinal transmission, taking the average length of the electron transmission path from the copper foil length (2170. The battery copper foil length is about 1000mm) reduced to the battery height (80mm) to reducing the battery resistance by an order of magnitude.
The large cylindrical no lug battery design ensures the battery charging efficiency.Shen Li and others of Imperial College University in the UK compared the charging and discharge process of single lug and no lug batteries, and calculated that the no lug design can effectively reduce the local current density, and the heat production rate is two orders of magnitude lower than that of single lug batteries.The study shows that the no lug design can reduce the thermal effect of the charging process, thus ensuring the consistency, safety and charging efficiency of large cylindrical batteries.
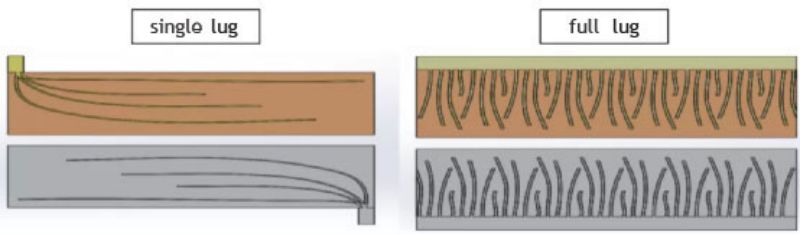
The full tab design can shorten the electronic transmission path and reduce the internal resistance of the battery
Benefit from the small internal resistance and high consistency of the large cylindrical battery, and the high adaptability of the large cylindrical battery, high energy density materials and high voltage fast charging system.To address consumer range anxiety, most manufacturers solve the problem by increasing battery capacity to improve range, increasing charging speed and reducing charging time.In order to increase the battery capacity, high nickel cathode material and silicon carbon cathode material with higher energy density need to be used; In order to reduce the charging time, the charging power of electric vehicles needs to be increased, that is, by increasing the charging current or the charging voltage, and the increasing voltage can reduce the line current and thus reduce the energy loss.Because high energy density materials and fast charging are easy to produce lithium precipitation, expansion and other side reactions during charging, so generally high energy density materials and fast charging system are not compatible.At present, 400V voltage system is commonly used in electric vehicles. Because the voltage of a single lithium ion battery is only 3~4V, it needs about 100 batteries in series to reach the 400V voltage requirement, while 800V high voltage fast charging system needs about 200 batteries in series, and 800V high voltage fast charging system puts forward higher requirements for battery consistency.Because large cylindrical battery has the characteristics of small internal resistance, and has the advantages of high consistency and high energy density materials, so large cylindrical battery can be compatible with high energy density materials and high voltage fast charging system.(Source: Future Think Tank)
2.Battery link: Battery manufacturers layout 4680 battery, and the multiple advantages of 4680 battery help increase the cylinder share
2.1 High concentration of power battery industry, and the technical route layout at home and abroad is different
The concentration of the power battery industry has increased, and in 2021, the market share of enterprises in China, Japan and South Korea will exceed 90%.According to SNE Research and starting point research statistics, CR3 of power battery industry increased from 45.9% in 2017 to 65.1% # CR5 in 2021 from 58.3% in 2017 to 79.5% in 2021, and the industry concentration increased significantly.In 2021, the top 10 global power battery enterprises in installed capacity are all enterprises from China, Japan and South Korea, accounting for 91.2% of the total installed capacity. The number of enterprises from China, Japan and South Korea is 6,1 and 3, respectively.
Battery manufacturers in China and other countries differ in the layout of cylindrical, square and pouch batteries. In 1998, Panasonic's 18650 cylindrical battery produced by Panasonic has been batch assembled in many world brands. Due to Panasonic's technology accumulation of cylindrical battery, Panasonic and Tesla cooperated to jointly create the era of cylindrical lithium battery application in pure electric vehicles.South Korean companies LG Chem and SKI mainly take soft-pack routes. LG Chem relies on the accumulation of pouch batteries in consumer electronics to apply pouch batteries to electric vehicles. Pouch batteries are especially favored by plug-in hybrid vehicles due to their flexible volume and shape variation.At the beginning of Chinese enterprises, considering the technical accumulation of Japan and South Korea respectively in cylinder and soft pack battery, and cylinder battery very tests the battery management level of car enterprises, the localization rate of aluminum plastic film is low, so domestic enterprises led by CATL and BYD are mainly square route.
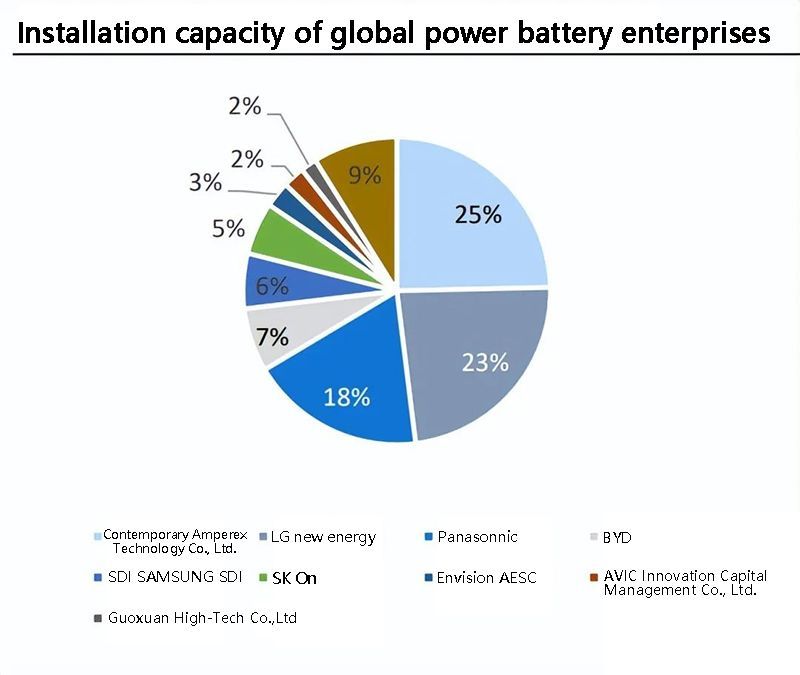
From 2017 to 2020, China's cylindrical battery market share fell sharply, while its overseas market share fell slightly.From the Chinese market, after 2017 affected by subsidies, initial cylindrical battery short range low-end models cannot get subsidies, cylindrical battery market share fell from 27.2% in 2017 in 2017 to 9.7% in 2020, its market share is mainly replaced by square battery. During this period, BAK, Optimumnano Energy and other companies based on the cylindrical route went bankrupt.From the global market, affected by the rapid increase in the penetration rate of new energy vehicles in Europe, overseas pouch battery shipments increased, occupying a certain market share of cylindrical battery market share decreased from 29% in 2018 to 23% in 2020.
Battery enterprises to accelerate the layout of 4680 battery, large cylindrical battery production capacity is about to be increased.In order to meet the demand for large cylindrical batteries, in addition to Tesla's own battery factory layout 4680 battery, battery manufacturers in China and other countries also accelerate the expansion of 4680: overseas enterprises Panasonic and LG Chemical are conducting product design and development to meet the requirements of Tesla; domestic battery enterprises EVE Energy, CATL, BAK are also actively layout related technologies.Currently, only Tesla battery factories and Panasonic can gradually mass-produce large cylindrical batteries by 2022, while EVE Energy and LG Chem plan to achieve mass-production by 2023.
The volume of 4680 large cylindrical battery is expected to become an important support for the increase of cylindrical share.According to the official materials of Tesla Battery Day, if the 4680 battery is successfully mass-produced in the future, upgrading from 21700 battery to 4680 battery can reduce the unit production cost by 14%, and narrow the cost gap between ternary batteries and lithium iron phosphate batteries, large cylindrical batteries will have an impact on the existing battery structure system with high cost performance.In the future, under the background of continuous technology optimization of large cylindrical batteries, we expect that the global proportion of cylindrical power batteries is expected to reach 27% in 2025, and the demand for cylindrical power batteries will reach 318.2 GWh.(Source: Future Think Tank)
3.Material link: The demand for large cylindrical batteries increases, improving greatly the application potential of high energy density materials
3.1 High nickel cathode: high nickel expansion peaks and and the integrated layout creates the high nickel cathode material leader
3.1.1 The proportion of NCM811 driven by mileage demand increases
The cathode material is an important part of the lithium-ion battery, which determines the performance of the whole battery, and its cost accounts for about 30% -40% of the battery.Common cathode materials used today are lithium cobalt oxide, lithium manganate, lithium iron phosphate and ternary materials.Ternary materials generally nickel cobalt manganese lithium (NCM), due to nickel, cobalt, manganese are in the fourth cycle of the periodic table adjacent position, ionic state of similar chemical properties and radius, according to any proportion to form solid solvent, so can adjust the proportion of nickel cobalt xuan elements in the material to selective amplification material some aspect of the advantages, to meet the different battery performance requirements:
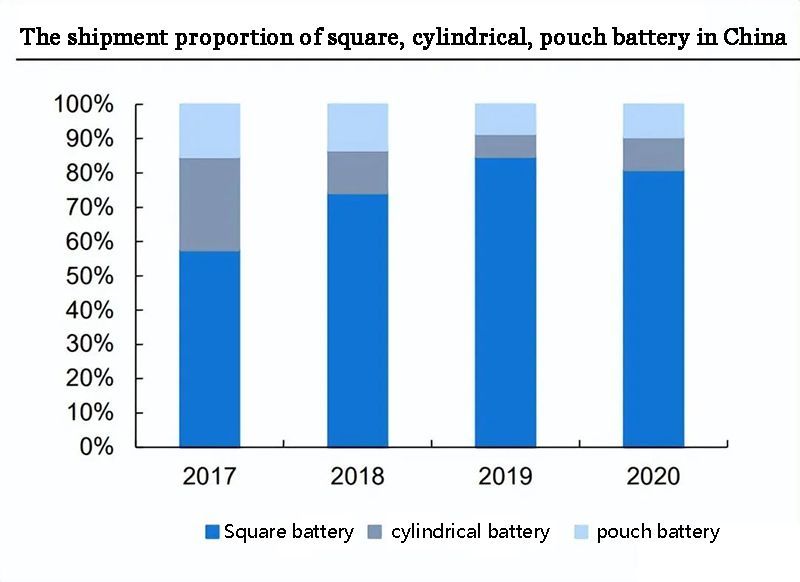
(1)Nickel:
redox reaction in the process of charging and discharging mainly depends on nickel valence, so the content of nickel in the cathode material determines the energy density of the battery, but high nickel proportion can cause serious cation mixing phenomenon (refers to the discharge, by external factors, second order Ni ions occupy Li ion lattice position phenomenon), affect the material performance;
(2)Cobalt:
Cobalt can inhibit cation mixing, stabilize the layered structure, improve the conductivity and reduce the impedance, but cobalt has expensive and other problems;
(3)Manganese:
manganese has good electrochemical inert, so that the material always maintains a stable structure, and cheap manganese can also play a role in reducing the battery cost, but too high manganese content will produce certain damage to the layered structure.
In ternary cathode materials, the mainstream NCM models in the industry include 523,622 and 811, high nickel cathode usually refers to the material model with a relative nickel content of more than 0.6.6.With the increase of nickel content and cobalt content, the energy density of ternary materials will gradually increase, but the capacity retention rate and thermal stability of the materials will be reduced, and the phenomenon of oxygen precipitation will be more obvious.At present, cathode material manufacturers mainly modify high nickel ternary materials by ion doping and surface coating, so as to improve the performance of high nickel NCM and NCA:
(1)Ion doping:
high nickel ternary material ion doping generally choose similar ion radius doping, distribution in the lattice of the doping elements supporting column, thus reducing the risk of the lattice volume in the cycle, so through the introduction of ions can stabilize the layered structure, improve the electrochemical properties of the material, especially the thermal stability;
(2)Surface coating:
Surface coating can inhibit the transformation of crystal type and the dissolution of transition metal during the charge and discharge process, To change the surface chemical properties of the material to improve its electrochemical properties, Avoid or reduce the direct contact between the electrolyte and the cathode material, Prevent the dissolution of the electrode transition metal; at the same time, The cladding layer acting as a conductive medium can facilitate the diffusion of Li ions on the particle surface, Thus improving the capacity maintenance performance, ratio performance and thermal stability; besides, High nickel NCM cathode material storage conditions requirements are higher, When a high-nickel ternary material burst is exposed to a wet environment, Material surfaces readily absorb water and carbon dioxide in the air, To generate impurities such as LiOH and Li2CO3, Seriously affecting its electrochemical properties, Cover modification can reduce the contact between cathode materials and air during mass production, Extended storage life; common surface coating include oxide, phosphate, lithium and conductive materials.
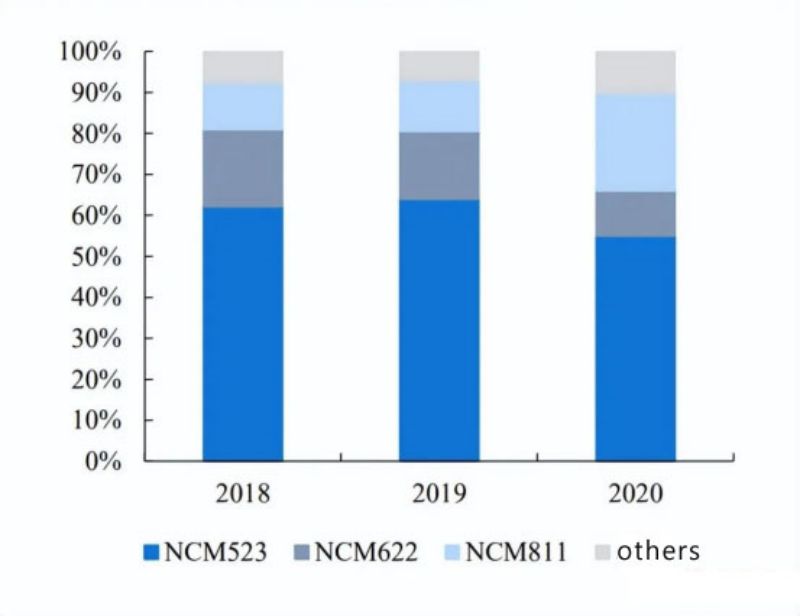
China lithium battery ternary cathode material product structure
The proportion of mileage demand-driven high nickel materials continues to increase.In order to solve the problem of consumer "range anxiety", manufacturers improve the range by increasing the battery capacity. High nickel ternary material has the characteristics of high energy density, and range advantage, and the proportion of high nickel cathode in ternary materials is rapidly increased.According to GGII data, NCM811's share of ternary materials has increased from 11.5% in 2018 to 24% in 2020. According to the data of Xinleng Information, the NCM811 penetration rate in China reached 41% in August 2021. With the release of high nickel production capacity of 2021Q4 head enterprises, ICCSINO expects that the penetration rate of high nickel materials (NCM811 and NCA) in China is expected to reach 40% in 2021. On November 18,2021, the Ministry of Industry and Information Technology issued the lithium ion battery industry specification conditions (2021) (draft), the specification requirements ternary material capacity X75Ah / kg, 5 and 6 series NCM ternary material capacity does not meet the requirements of the specification, and 8 series NCM and NCA high nickel ternary materials meet this requirements, national policy specification is conducive to further improve high nickel material.
3.1.2 High nickel large cylindrical battery has obvious advantages
The thermal runaway of lithium battery is mainly caused by the rising temperature inside the battery.The heat production of the battery is an inevitable product in the working process of the battery. If the heat production speed of the battery is faster than the heat release, namely the heat diffusion speed, the internal temperature of the battery will rise.Battery overcharging, short circuit caused by diaphragm defects and short circuit caused by external impact will produce a lot of heat, so that the battery temperature rise.When these heat can not be evacuated in time, it will aggravate the reaction, and trigger a series of self-heating reactions, cathode material reaction will aggravate the release of heat release and oxygen, battery temperature rises sharply, thermal runaway, and eventually lead to the combustion of the battery, even explosion in serious cases.
With the increase of nickel content in ternary materials, the risk of thermal runaway in batteries increases.The results show that the thermal runaway starting temperature of NCM811 is 163.0 C, 22.5 C lower than that of NCM622, and the heating rate of NCM811 is much higher than that in the temperature range of 150-200P. Moreover, the heat at the peak of release heat is NCM622 at 100% SOC.Studies show that high nickel materials have worse thermal stability, high nickel materials can cause thermal runaway at relatively lower temperatures, and release higher heat when thermal runaway, which will lead to an increased risk of battery thermal runaway.
During charging, low battery consistency will lead to overcharging, resulting in thermal runaway.During battery charging to a specific SOC, the SOC before charging, and batteries with a high initial SOC are overcharged during charging.Overcharging will first lead to electrolyte decomposition, positive interface battery temperature slowly increase, then excessive Li ions from the positive embedded, lead to unstable cathode material and oxygen, excessive Li ion deposition on the negative form lithium dendrite, lithium dendrite growth and puncture diaphragm cause power short circuit heating, cause thermal runaway and safety accidents.
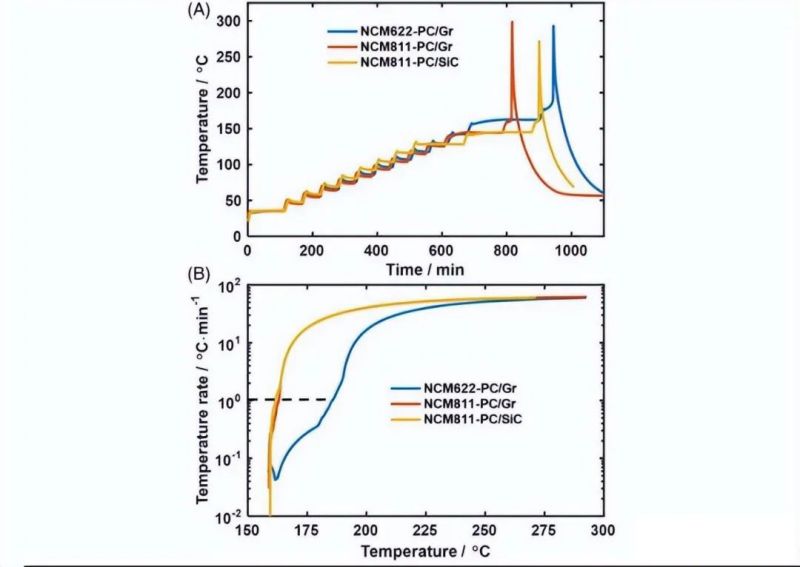
NCM811 has worse thermal stability than NCM622
Benefiting from the thermal runaway transmission blocking characteristics of cylindrical battery and the high product consistency, the adaptability of large cylindrical battery and high nickel ternary cathode material is very high.Cylinder battery uses quite mature winding process, high degree of automation, and high product consistency.The unique cylindrical curved surface makes it still have a large gap in full contact, which can inhibit the heat transfer between batteries to some extent.Therefore, cylindrical batteries are better than square batteries and pouch batteries in terms of consistency and heat dissipation performance. Cylinder batteries have advantages in dealing with thermal runaway. Applied high nickel ternary materials in cylindrical batteries can compensate for the defect of thermal stability difference of high nickel ternary materials.In addition, the unique no lug design of large cylinder battery can reduce the thermal effect of large cylindrical battery in the charging process, and further avoid the occurrence of thermal runaway of high nickel ternary lithium battery.High nickel ternary material application in large cylinder battery can give full play to the advantages of both, high nickel ternary material high energy density can make up for the cylindrical battery into low efficiency than the low capacity, large cylinder battery high consistency and thermal runaway transmission block characteristics can compensate for the high nickel ternary material thermal stability disadvantages.
3.1.3 The increased demand for high nickel is conducive to the leading enterprises in ternary precursors and cathode materials
The volume of large cylindrical batteries will increase the demand for high nickel materials, and in 2025, the demand for high nickel cathode batteries will reach 26. [10,000 tons.Tesla has used Panasonic's NCA battery since 2012, and has since increased its cathode nickel content, including the Panasonic 21700 battery. In July 2021, Tesla first used a new NCMA battery produced by LG Chem, which has raised 90% nickel at the cathode.The impact of large cylindrical battery on high nickel ternary cathode demand is calculated, referring to the replacement speed of 21700 to 18650, it is assumed that cylindrical battery in 2022 is mainly 21700,246800 gradually replace 21700 after 2023, and the permeability of large cylindrical battery is expected to reach 54.7% in 2025.Assuming that large cylindrical batteries adopt high nickel cathode such as NCM8 series, NCM9 series or NCA and NCMA, the demand for high nickel cathode of large cylindrical batteries in 2025 will reach 261,000 tons, nearly three times the global demand for high nickel cathode in 2020.In 2025 high nickel battery ternary cathode demand, nearly 45% of high nickel cathode will be used in large cylindrical batteries, large cylindrical batteries will greatly increase the demand for high nickel materials.
Ternary precursor: high nickel chemical good integration layout precursor enterprises
The ternary cathode material industry chain involves many links, and the industrial chain structure is more complex.The upstream of NCM ternary industry chain is mainly nickel, cobalt, yi, lithium and other auxiliary materials suppliers, the midstream is precursor and ternary cathode materials manufacturers, and the downstream is lithium battery manufacturers and applications of electric vehicles, 3C, energy storage and other fields.Among them, the precursor link is the key link of the cathode material industry chain. Taking NCM811 ternary cathode material as an example, the precursor accounts for about 60% of the total cost of the cathode.The ternary precursor is nickel cobalt pick / aluminum hydroxide mixed with lithium source (high nickel cathode materials; low nickel and medium nickel cathode materials generally use lithium carbonate).The upstream industrial chain of ternary precursor is long. Take nickel resources as an example, from the front primary ore (sulfide, laterite nickel ore) is processed into intermediate nickel (high ice nickel, MHP, MSP) to nickel sulfate, and finally processed into precursor.
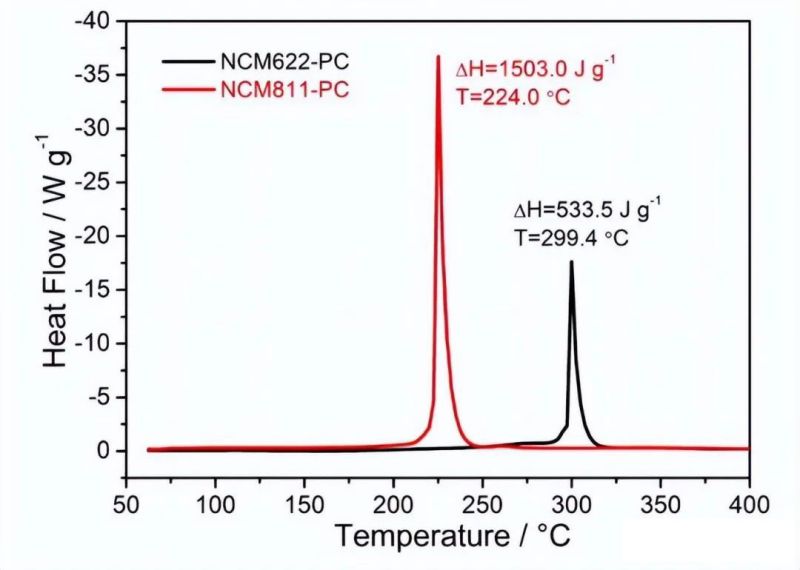
The NCM811 heat release peak is three times that of NCM622
China's ternary precursor industry concentration is relatively high, with CR5 reaching 65% in 2020.Under the background of the continuous strong demand for the global power battery market, the increased demand for ternary cathode has driven the continuous expansion of the ternary precursor industry. According to the statistics of ICCSINO, the total output of China's ternary precursor in 2021 was 620,600 tons, up 82.3% year on year.At present, China's ternary precursor industry concentration is high. According to GGII statistics, the top five market share in 2020 are Cngr Advanced Material, Guangdong Brunp Recycling Technology, GEM, Zhejiang Huayou Cobalt and Ghana Energy, with a market share of 21.8%, 15.5%, 12.1%, 11.2% and 4.5% respectively.
With the cathode extremely high nickel conversion, nickel increases in the cost of ternary precursor, which will be good for the integrated layout of ternary precursor enterprises.From the perspective of precursor cost structure, the cost of sulfate raw materials such as cobalt sulfate and nickel sulfate is relatively high. Taking the ternary precursor produced by Zhejiang Huayou Cobalt as an example, the raw material cost of sulfate accounts for 87%.With the increase of cathode nickel content, the use of a single ton of precursor nickel sulfate increases, and the cost proportion of nickel sulfate will increase.In the trend of high nickel conversion, the demand for upstream nickel resources will increase, resulting in tight nickel supply and significant increases in prices.According to ICCSINO, as of March 23,2022, the price of Chinese battery grade nickel sulfate is 48,500 yuan / ton, up 64.4% compared with 29,500 yuan / ton at the beginning of 2021. The cost ratio of nickel sulfate and the increase of nickel source price strengthen the willingness of precursor enterprises to integration.Through the integration of the upstream smelting industry chain layout, the upstream nickel sulfate and other raw materials supply into the production link, can give full play to the industrial chain synergistic effect, ensure the stable material supply and quality assurance, with cheaper for raw materials and improve ternary precursor material performance, and enhance the enterprise's cost advantage and profitability.At present, the precursor leading enterprises Cngr Advanced Material, Guangdong Brunp Recycling Technology, GEM and Zhejiang Huayou Cobalt have arranged nickel smelting capacity, the integrated layout will strengthen the cost advantage of leading enterprises, the industry concentration is expected to increase.
Ternary cathode materials: high nickel to improve technical barriers, cathode enterprises with technical reserves have development potential
China's ternary cathode material market pattern is relatively scattered, high nickel is expected to promote the industry concentration.As China's power battery field is in the stage of rapid demand growth, ternary cathode material enterprises expand strong production, the competition is relatively fierce, resulting in a relatively scattered industry.According to ICCSINO statistics, in 2021, China's ternary cathode market CR5 is 53%, the market share of 5 top enterprises are about 10%, there is no absolutely leading leading enterprises.With the development of ternary cathode to high nickel, due to the high technical barriers of high nickel materials, ternary cathode industry has an obvious concentrated trend. From January to October 2020, CR2 and CR5 in China's high nickel cathode material market are 56% and 84% respectively, and the leading advantages of high nickel ternary cathode materials market are obvious.
High nickel ternary cathode processing is difficult, high technical barriers.The ternary cathode is mainly made of tertiary sintering process, which is made of ternary precursor and lithium hydroxide mixed before sintering.Compared with conventional ternary cathode materials such as NCM523, the preparation process of high-nickel ternary cathode materials is relatively more complex, with higher equipment requirements and more technical difficulty:
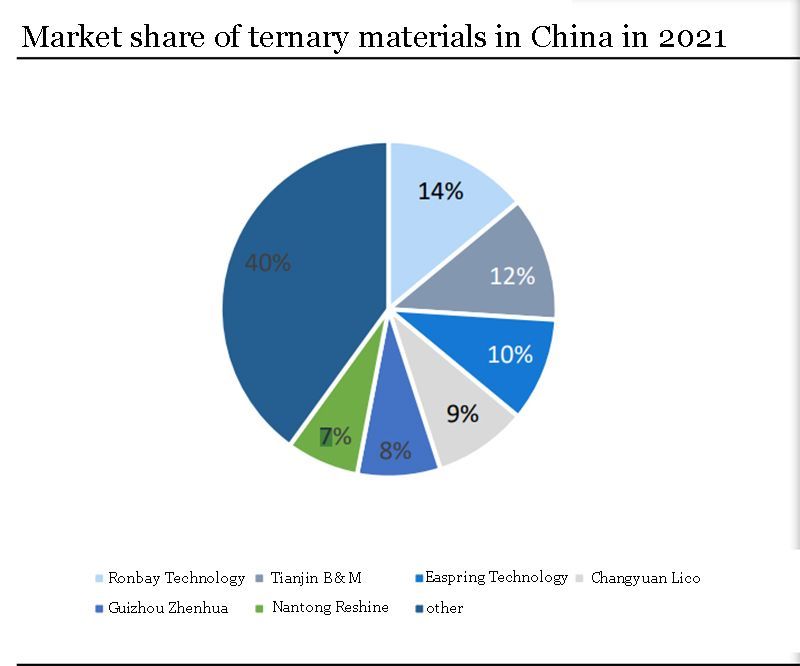
(1)Difficulty in mixing process:
due to the particle size and density difference between lithium hydroxide and high nickel ternary precursor, it is difficult to achieve solid phase uniform mixing; in addition, lithium hydroxide contains crystalline water, friction and heat during the dehydration, some lithium hydroxide will produce and reunite, affect the mixing effect; the lithium hydroxide, improve speed and easy to destroy the ternary precursor particles.Therefore, the high nickel mixer is high in the ternary production process;
(2)Difficulties in sintering process:
because the divalent nickel in high nickel ternary material is difficult to oxidation into trivalent nickel, must be synthesized at high temperature in pure oxygen atmosphere, so the kiln material must be resistant to oxygen corrosion resistance; in addition, high nickel material use lithium hydroxide as lithium source for high temperature synthesis, lithium hydroxide is volatile and strong alkaline, need the kiln material has strong alkali corrosion resistance;
(3)Difficult points in washing process:
the high residual alkali content of high nickel ternary material will bring many negative effects on the electrochemical properties of the material. Chinese manufacturers generally use washing and secondary sintering process at low temperature to reduce the residual alkali content of high nickel cathode surface; because high nickel ternary material is sensitive to humidity, the solid-liquid ratio, washing time, mixing time, filtration time and drying process cannot control the requirements of power battery.
Leading enterprises production expansion accelerated, high nickel is expected to help enterprises with technical reserves to further improve the market share.Due to high nickel ternary cathode material for precursor system, sintering process and process control and production environment requirements, so cathode material enterprises in addition to high requirements for continuous research and development ability, the performance of the core production equipment and production line design detail requirements are also high, so for new entrants, both material formula design and key equipment selection or process detail design constitute a big challenge.In addition, due to the harsh requirements of high nickel ternary cathode materials on safety performance, high nickel ternary cathode material manufacturers need to meet the customer certification requirements are much higher than ordinary ternary cathode materials, high nickel ternary cathode products have high customer viscosity. In the context of a substantial increase in high nickel positive electrode demand, with mass production capacity and through customer certification, Ronbay Technology, Tianjin B & M, Easpring Technology, Zhenhua E-chem to accelerate the expansion of high nickel cathode. It is expected that in 2023, the domestic high nickel cathode production capacity will exceed 50 0,000 tons, up nearly 370% compared with the end of 2020, and the concentration of the ternary cathode industry is expected to further improve.
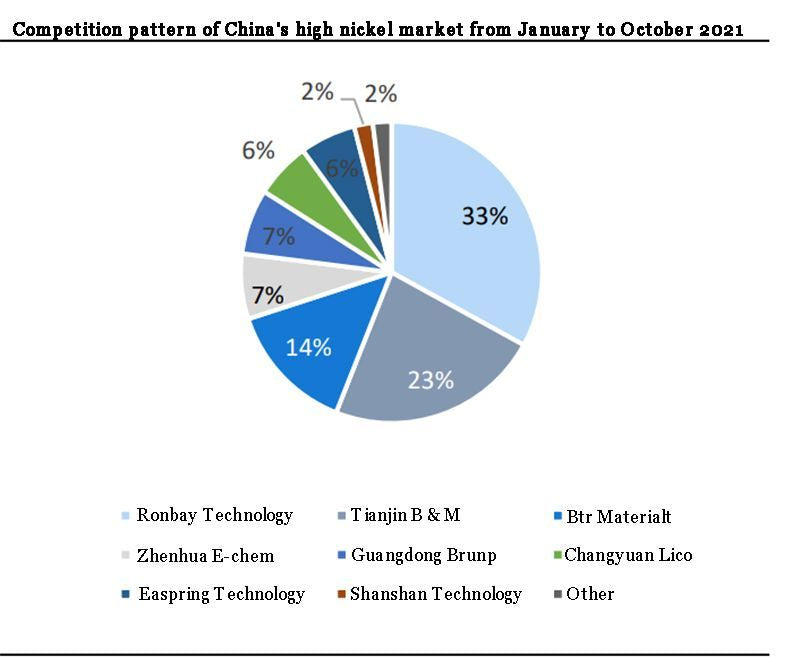
3.2 Silicon-based anode: The demand for silicon-based anode is upward, and the commercialization process is expected to accelerate
3.2.1 High specific capacity silicon materials have attracted much attention
At present, the cathode material is mainly graphite.The shuttling of lithium ions between the cathode and anode forms the basis for lithium-ion batteries to work as a power supply.Therefore, the lithium ion insertion capacity of the anode is the main factor determining the performance of the lithium ion battery, and its off-embedded voltage and specific capacity have a great influence on the energy density of the battery.Currently, the commercial cathode materials are mainly carbon-based materials (natural graphite, artificial graphite and amorphous carbon), silicon-based materials and lithium titanate. Because of its good electrical conductivity, small volume expansion, good cycle stability and other advantages, the most widely used: artificial graphite is mainly used for large capacity automotive power battery and ratio battery and high-end electronic products lithium ion battery; natural graphite is mainly used for small lithium ion battery and low-end electronic products lithium ion battery.At present, the power battery cathode materials is mainly graphite. According to GGII statistics, 2021H1 artificial graphite and natural graphite negative shipments accounted for 85% and 14% respectively, and graphite negative shipments accounted for 99%.
The anode of the graphite material is close to the upper limit of the theoretical specific capacity.At present, the specific capacity of high-end graphite anode material has reached 360-365mAh / g, close to its theoretical specific capacity value of 372mAh / g.With the continuous improvement of the endurance requirements of new energy vehicles, in order to further improve the battery energy density, it is necessary to develop cathode materials with higher specific capacity, and the silicon elements with high specific capacity attract the attention of researchers.
The theoretical specific capacity of silicon material is more than ten times that of graphite material. Due to the high volume expansion rate and unstable SEI layer, the commercialization degree of silicon-based anode is low.Silicon is widely distributed in nature, accounting for about 26.3% of the earth's crust, second only to oxygen.In the process of lithium ion embedding, Li22Si5 phase is formed, and the corresponding theoretical capacity is more than ten times that of natural graphite. At the same time, the voltage platform of silicon is about 0.4 V. There is no hidden danger of lithium analysis in the charging process, which greatly improves the safe performance of lithium ion batteries.Although silicon materials have many advantages such as high theoretical specific capacity and rich reserves, silicon materials, as lithium ion battery cathode materials, face the problems caused by volume expansion, repeated regeneration of SEI layer and poor electrical conductivity that seriously hinder the commercial application of silicon cathode materials:
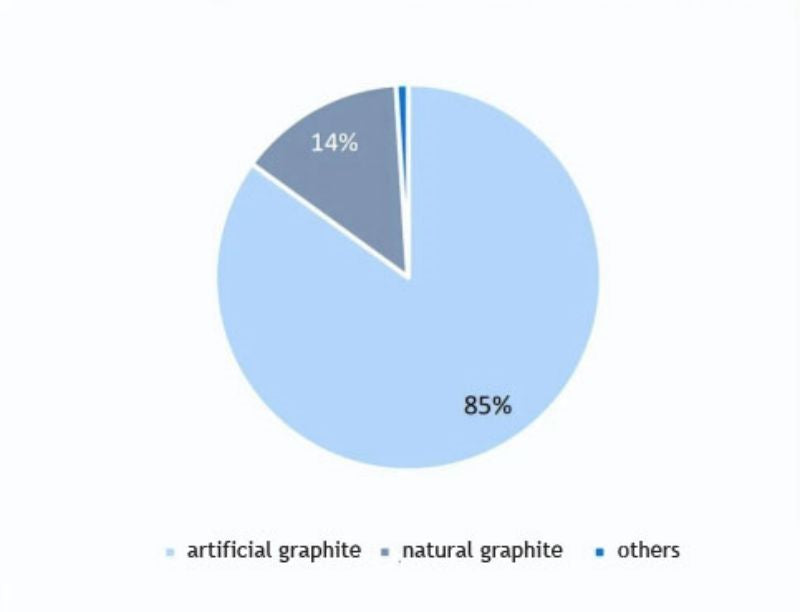
2021H1 negative pole market ratio
(1)Material powder and electrode destruction:
silicon in the process of charging and discharging will have a huge volume expansion effect, Li-Sj alloy with volume expansion of up to 320%, This constant contraction and expansion can cause cracks in the silicon anode material until pulverization, To break the contact between the electrode material and the fluid collection, Disach the active material from the pole, Causes the rapid attenuation of the battery capacity; next, Expansion creates great stress inside the battery, Form an extrusion against the polar sheet, With multiple cycles, The risk of fracture, And this stress may also cause the internal porosity of the battery, Reduce the lithium-ion mobility channels, Cause the precipitation of lithium metal, Impact on battery safety;
(2)Unstable SEI layer:
in the process of lithium embedded, electrolyte will decompose and deposition on the silicon surface to form SEI film, due to the continuous change of silicon volume in the process of embedded lithium, exposed to the electrolyte new silicon surface SEI film thickness continues to increase, continuous growth of SEI film will constantly consume lithium and electrolyte from the cathode, eventually lead to battery internal resistance increase and capacity rapid attenuation;
(3)Poor conductivity:
the conductivity of silicon is poor, which is not conducive to the effective release of battery capacity under the high ratio.
Manufacturers can improve the electrochemical properties of silicon-based anode through pre-lithium technology, nano-chemical technology and composite material technology to accelerate the commercialization process of silicon-based anode:
(1)Pre-lithium technology:
the use of pre-lithium technology can effectively compensate the active lithium loss of silicon anode caused by the SEI layer instability in the first cycle process, improve the first Kulun efficiency, energy density and cycle life of the battery; stable lithium metal powder (SLMP) is the most widely used in commercial production;
(2)Nanometer technology:
the atoms on the surface of nanomaterials also have a higher average binding energy, therefore, nanomaterials can better release stress in the process of volume expansion, the nanometer of silicon particles can effectively alleviate the volume expansion of silicon lithium removal process; but its larger specific surface area will aggravate the silicon surface SEI layer formation, and small nanoparticles are easy to agglomeration and speed up the capacity decay, so usually introduce carbon materials, design low-dimensional nano silicon tube silicon carbon composite material;
(3)Silicon carbon composite technology:
by covering the hail carbon material on the surface of silicon particles can effectively buffer the volume expansion in the cycle process, this evening carbon can increase the conductivity of particles, the porous structure of carbon is conducive to the rapid transmission of lithium ions and electrons between silicon particles and electrolyte;
(4)Silicon oxide composites:
Silicon oxide reacts with lithium ions in the first cycle to form Li4SiO4, Li2O and nanossilicon particles. Li4SiO4 and Li2O can effectively alleviate the volume effect of silicon particles. Tesla's all-new silicon material is expected to promote the promotion of silicon-based anode.Tesla unveiled a new silicon anode, which improves battery stability and safety by adding a high-elastic ionic polymer coating to restabilize the silicon surface structure.Raw silicon anode can improve battery range by 20% and drive battery costs down by 5%.Raw silicon anode technology is expected to reduce the manufacturing cost to $1.20 / kWh, and a significant cost reduction is expected to promote the promotion of silicon-based anode.
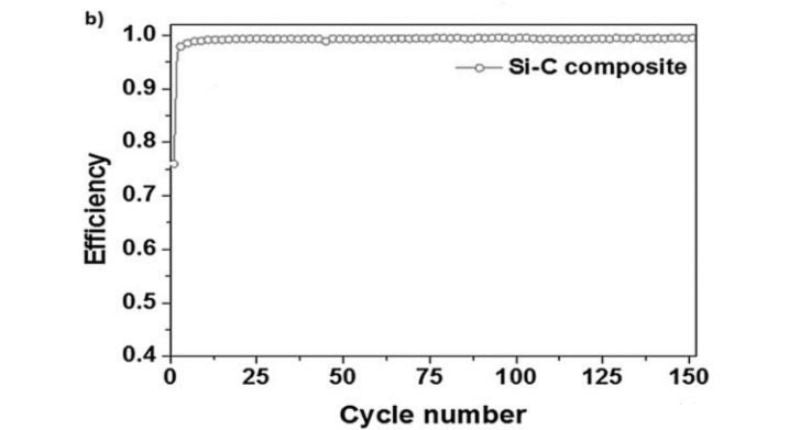
The cycle stability of the silicon-carbon composite negative electrode is good
3.2.2 Silicon-based anode is used in 4680 battery, and the commercialization process of silicon-based anode is accelerated
At present, commercial silicon-based anode is mainly used in cylindrical batteries, 4680 battery will increase the demand for silicon-based anode. Nanocrystalline silicon carbon and silicon oxide are two kinds of silicon based anode materials with the highest commercial degree at present. Silicon based anode materials are used in graphite by doping in a certain proportion (5%-10%). Because square cells and pouch cells are very sensitive to expansion, silicon-based materials are still difficult to apply to these two types of cells. At present, silicon-based anodes are mainly used in cylindrical steel shell cells with higher structural strength. Tesla has used silicon carbon anode as a new material for power battery in some models by adding silicon based material to artificial graphite. With the increase of Tesla's 4680 battery in the future, the demand for silicon based anode will be greatly increased.
Compared with graphite anode materials, the preparation process of silicon-based anode materials is complicated and has a higher technical threshold. Silicon carbon anode material is the nano silicon and matrix material through the granulation process to form the precursor, and then through the surface treatment, sintering, grinding, screening, demagnetization and other processes prepared from the cathode material; Silicon oxygen anode material is pure silicon and silicon dioxide synthesis silicon oxide, forming silicon oxygen anode material precursor, and then by crushing, grading, surface management, sintering, screening, demagnetization and other processes prepared from the cathode material. In order to ensure the product has high consistency, high safety, high cycling and low swelling, there are some difficulties in large-scale production, and different processes are different, there is no standardized process at present. At present, chemical vapor deposition, sol-gel, high temperature pyrolysis and mechanical ball milling are commonly used. The difficult production process and mass production capacity are the main threshold for entering the field of silicon - based anode materials.
Chinese enterprises accelerate the layout of silicon - based anode, scale commercialization process accelerated. Silica-based anode started earlier in Japan, and the material has been used in batches in Japan. The NCR18650C battery released by Panasonic of Japan has a capacity of up to 4000mAh/g, and was mass-produced in 2013. In addition, Hitachi, Shin-Etsu and Mitsubishi have realized the mass production of silicon carbon anode. At present, only a small part of China enterprises to achieve mass production, most are still in the pilot or experimental stage. Research and development or production of silicon based anode enterprises mainly include: anode enterprises such as Shanshan, Putailai, Kaijin Energy, etc.; School-enterprise cooperation teams such as Tianmu Leader, Xin 'an Stock, etc.; Enterprises that have crossed into the anode field such as Guoxuan High-tech (battery enterprise), Shida Shenghua (electrolyte enterprise), Jiibao Technology (chemical material enterprise), etc.
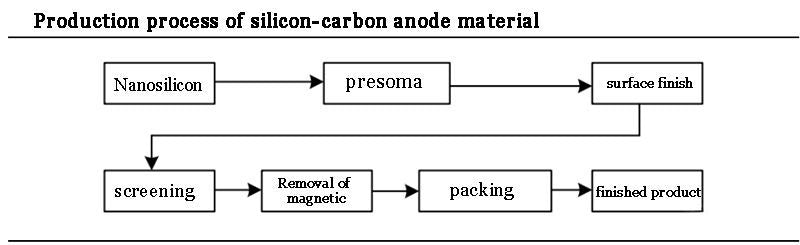
3.3 LiFSI: 4680 battery drives the demand of LiFSI to increase, and the large-scale layout of China enterprises accelerates
3.3.1 LiFSI has obvious performance advantages, and high nickelization helps to increase the demand for LiFSI
Electrolyte is one of the four key materials of lithium battery. Its main components are organic solvent, lithium electrolyte and additive. Lithium salt is a key part of the electrolyte, the selection of lithium salt has great influence on the capacity, energy density, power density, working temperature, cycling performance and safety performance of the battery. Therefore, high quality lithium salts need to have high ionic conductivity, high solubility, low crystallization point, high stability, SEI film forming ability, strong hydrolysis resistance and aluminum foil passivation:
(1) high ionic conductivity:
high conductivity electrolyte can rapidly conduct lithium ions, improve the efficiency of charge and discharge; Because the dissolution of lithium salt in the solution is accompanied by the dissociation of anion and anion in lithium salt, the formation of solvated solution structure, so the low dissociation can ensure that the electrolyte formed after the dissolution of lithium salt has a high conductivity, and then realize the high rate of battery;
(2) High solubility:
high solubility ensures that there are enough lithium ions in the electrolyte for transmission;
(3) Low crystallization point:
low crystallization point can avoid the crystallization precipitation of lithium salt in the temperature range of battery work, can avoid the risk of sudden drop of electrolyte conductivity, so as to ensure that the battery can work normally in low temperature environment;
(4) High stability:
Lithium salt should have good thermal stability, chemical stability and electrochemical stability. When the battery works under high pressure and high temperature, lithium salt will not react with other components (except the process of forming SEI layer);
(5) Have SEI film forming ability:
Electrode surface after the first cycle will form a layer of solid electrolyte film (SEI), the passivation film can allow by lithium ion and block, and prevent the continuous consumption of electrolyte, it is of great significance on the stability of cell cycle, so good SEI film performance can ensure follow-up cycle fluid CLP solution will not be continuously drains; Both lithium salts and additives in electrolyte affect the performance and stability of SEI layer.
(6) Strong resistance to hydrolysis:
The anions of some lithium salts will hydrolyzate after contact with water (especially at high temperature and high voltage), forming HF, which will seriously affect the battery life and increase the extra cost of preparation, storage and treatment of lithium salts;
(7) Passivation of aluminum foil:
lithium salt needs to have a good passivation effect on aluminum foil collector to prevent electrolytic solution from corroding aluminum foil under high voltage.

LiPF6, lithium hexafluorophosphate with stable performance, is the mainstream solute lithium salt at present, but it has some disadvantages such as easy decomposition in heat, hydrolysis resistance, easy crystallization at low temperature and so on, and its performance is not good in high temperature, low temperature, humidity and other environments. LiPF6 is chemically unstable and sensitive to temperature and moisture. It is prone to decomposition under high temperature and humidity, resulting in dangerous HF, which seriously affects battery life. LiPF6 is easy to crystallize at low temperature, which leads to the decrease of electrical conductivity of electrolysis solution.
With the increase of nickel content in the cathode, the thermal stability and safety of the material decrease, and the high nickel battery requires higher matching of electrolyte. Due to the high catalytic activity of nickel ion, with the increase of nickel content in the cathode material, nickel will catalyze the decomposition of electrolytic liquid oxygen; In addition, trace water in the electrolyte will react with LiPF6 to generate ACIDIC HF, which erodes the cathode of the battery, leading to the dissolution of transition metal and the dissolution of transition metal ionons. The dissolved transition metal ions will accumulate in the gap of the diaphragm and the surface of the anode, hinders the transmission of lithium ions and degrades the INTERFACE SEI layer structure of the anode side. Even lead to continuous decomposition of electrolyte on the anode surface, affecting the normal operation of the battery; Due to the poor thermal stability of high nickel materials, high temperature will accelerate the dissolution of transition metal, further deteriorate the battery state. In order to ensure the normal operation and safety of high nickel cathode battery, it is an important trend to replace ordinary electrolyte with high safety and high energy density electrolyte.
Compared with LiPF6, lithium difluorosulfonimide (LiFSI) has the advantages of high conductivity, strong hydrolysis resistance and good thermal stability, and is more suitable for high-nickel batteries:
(1) High conductivity:
The fluorine atom in LiFSI molecule has strong electron-absorbing ability, which can delocalize the anode charge on N. The ion association pairing effect is weak, which makes Li ion more easily dissociate, so LiFSI has high conductivity.
(2) Strong hydrolysis resistance:
The results of hydrolysis tests on LiPF6 and LiFSI showed that the water content and HF concentration in LiFSI solution remained almost unchanged during the test period, while the water in LiPF6 solution was exhausted on the 9th day, and HF concentration increased significantly, indicating that FSI- anion had better hydrolysis resistance.
(3) Good thermal stability:
The results show that LiPF6 electrolyte and LiFSI electrolyte have the same battery cycle performance at 25℃, but at 60℃, LiPF6 battery capacity is only half of LiFSI battery, indicating that LiFSI has better thermal stability. LiFSI added batteries perform better at high temperatures.
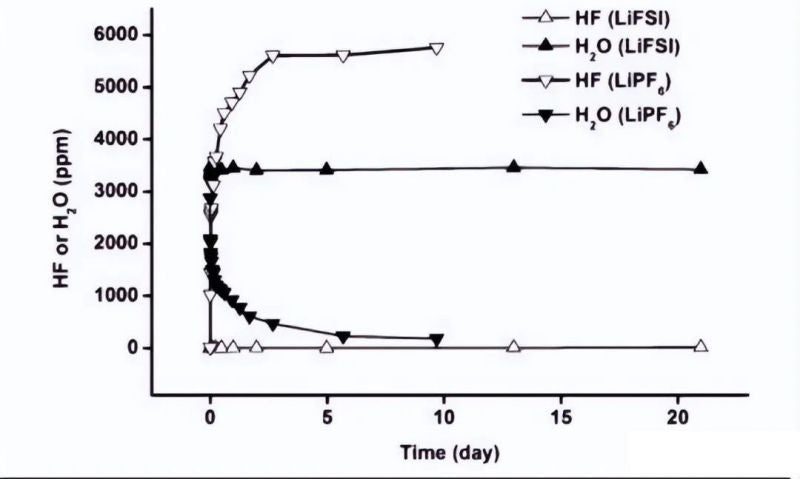
The LiFSI has a better resistance to hydrolysis
Although LiFSI has a certain corrosion effect on aluminum foil, it can be solved by adding a small amount of additives, such as aluminum foil additives containing fluorine passivation. In addition, LiFSI has a lower crystallization point, which makes it less susceptible to crystallization at low temperatures, thus avoiding the risk of a sudden drop in electrolyte conductivity and ensuring that the battery can work properly at low temperatures. Therefore, compared with LiPF6, LiFSI can significantly improve the service life of new energy batteries, improve the range and charge-discharge power of new energy vehicles in summer and winter, and improve the safety of new energy vehicles under extreme conditions. LiFSI is expected to become the next generation of mainstream lithium salt.
At present, LiFSI is mainly used as LiPF6 additive. The results show that the electrolyte with a special ratio of LiFSI and LiPF6 has better low temperature discharge and high temperature performance retention, longer cycle life, higher discharge rate performance and higher safety performance. Compared with the existing LiPF6 solute electrolyte, the battery with LiFSI added to the electrolyte can improve its service life, summer or winter range, charge and discharge power, and overall safety. Currently, the addition proportion of LiFSI in the mainstream formula is 2-10%. With the high nickelization and high pressure of power batteries, the proportion of LiFSI is expected to increase.
3.3.2 The demand for LiFSI is expected to increase significantly, and the leading company will be stronger
LiFSI entered the stage of large-scale production, and the price drop accelerated the industrialization process. Because LiFSI decompose easily when exposed to heat or high temperatures in the presence of water, other metal ions introduced during conventional manufacturing can adversely affect its performance. In order to meet the requirements of the use of electrolyte, LiFSI has strict limits on water, metal ions, ionizing acid and other indicators, leading to a high technical threshold of LiFSI production. Therefore, the price of LiFSI at the beginning of application is high, which restricts the rapid industrialization of LiFSI. With the continuous optimization of LiFSI production process, the price keeps decreasing. According to the data, the price of LiFSI per ton in 2018, 2019 and 2020 is 52.9, 49.0 and 41.4 ten thousand RMB respectively. The lower price accelerated the industrial application of LiFSI.
LiPF6 price continues to rise, LiFSI economy gradually emerged. From 2018 to 2020, the price of LiPF6 per ton has been maintained at about 100,000 RMB. LiPF6 with low cost and relatively stable performance has become the mainstream solute lithium salt. In the context of the rapid growth of downstream installed demand, LiPF6 market is in a state of short supply, combined with the impact of upstream raw material bottlenecks and the epidemic, LiPF6 production expansion rate is slow, resulting in a sharp rise in LiPF6 price. As of December 15, 2021, LiPF6 reached 550,000 RMB/ton, up more than 400% from 107,000 RMB/ton at the beginning of the year. LiPF6 price is expected to remain high before 2023. GGII estimates that LiPF6 price is expected to break through 600,000 RMB/ton. In the context of the high price of LiPF6, the economics of LiFSI gradually emerged, which is expected to accelerate the replacement of new lithium LiFSI.
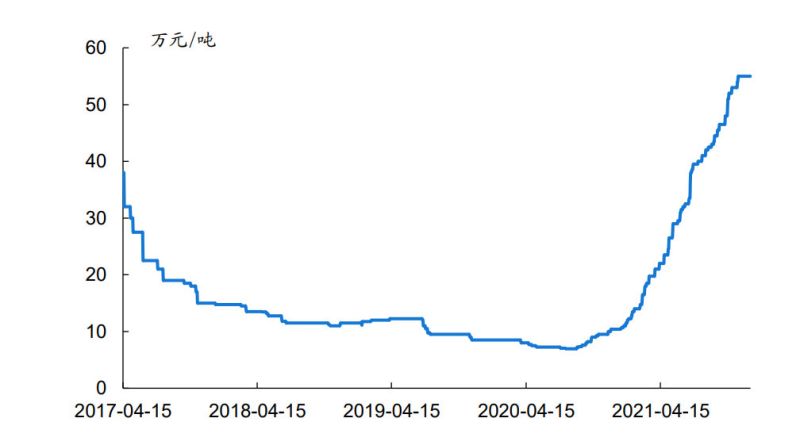
LiPF6 price trend
High nickelization of batteries and falling LiFSI costs are fueling demand for LiFSI. New energy battery electrolyte with LiFSI can greatly improve the charge and discharge times, but also can make nickel, high voltage cathode and other highly active electrode materials remain stable, so as to prolong the battery life, and flammable electrolyte play a flame retardant role. Therefore, with the high nickelization of power cells and the reduction of LiFSI cost, the addition ratio of LiFSI is expected to increase. Assuming that the proportion of HIGH-nickel battery LiFSI added in 2025 is 10%, the demand for HIGH-nickel battery LiFSI will reach 47,000 tons, with a compound growth rate of 132.5% in the five years from 2020 to 2025.
The demand for LiFSI is about to increase, and manufacturers' expansion process is accelerating. At present, LiFSI's China production capacity is mainly concentrated in the hands of Tianci Materials, Kangpeng Technology, DFD, Yongtai Technology, Xinzhubang and other enterprises. The total annual production capacity is about 6,500 tons, of which tianci material production capacity accounts for nearly 40%, is the absolute leader of LiFSI market. Global production capacity is mainly concentrated in South Korea Tianbao and Japan catalyst, the total capacity of about 1 thousand tons. With the increase of downstream demand for LiFSI, Chinese enterprises began to accelerate the LiFSI capacity planning, Tianci Materials, Yongtai Technology and Duofudo have formulated 10,000-ton expansion plans. Most of the LiFSI capacity currently under construction and planned will be put into production in 2023-2025. It is expected that China's LiFSI capacity will exceed 110,000 tons by 2025, an increase of more than 1000% from the current capacity.
Tianci Materials promotes difluorosulfonimide (HFSI), the integrated layout promotes LiFSI cost reduction, benefits from industrial chain circulation and cost advantages, leading companies are expected to be strong and strong. Tianci Materials will increase the production capacity of 60,000 tons HFSI, which is about 55-60,000 tons of LiFSI supply capacity. The integrated layout is expected to promote the reduction of LiFSI cost. In addition, as the leading electrolyte in China, Tianci Materials takes full account of the connection between products in the industrial chain in business layout, and creates a lithium ion battery material product group with recycling advantages. Tianci Materials' "annual output of 400,000 tons of sulfur acid production project" plays an important role in this cycle. It not only provides part of the raw materials for LiFSI, but also reduces the cost of LiFSI device and exhaust gas treatment, thus reducing the cost and emission reduction of the cycle. Tianci Materials, by producing the core and key raw materials of its main products, builds a circular industrial chain system and obtains a continuous cost competitive advantage, which will consolidate and expand the company's position and influence in the industry and is expected to remain strong.
3.4 Carbon nanotubes: 4680 battery helps improve the permeability of carbon nanotubes
3.4.1 The performance of carbon nanotubes is superior, and the permeability of carbon nanotubes is promoted by the 4680 battery
As the key auxiliary material of power battery, conductive agent can increase the conductive contact between active substances, improve the transmission rate of electrons in the electrode of lithium battery, so as to improve the rate performance and cycle life of lithium battery. The charging and discharging process of lithium-ion batteries requires the joint participation of lithium ions and electrons, which requires the electrode of the battery to be a mixed conductor of ions and electrons. Cathode active material is mostly transition metal oxide or transition metal phosphate, they are semiconductors or insulators, poor conductivity, must add conductive agent to improve conductivity; The conductivity of graphite anode material is slightly better, but in many charge and discharge, the expansion and contraction of graphite material, so that the contact between graphite particles is reduced, the gap is increased and even some away from the collector, no longer participate in the electrode reaction, so it is also necessary to add conductive agent to maintain the stability of the conductivity of the anode material in the cycle process. In order to ensure that the electrode has good charge-discharge performance, a certain amount of conductive agent is usually added during the production of the electrode sheet to collect the micro current between the active substances and between the active substances and the collector fluid, so as to reduce the contact resistance of the electrode and accelerate the movement rate of electrons.
At present, the commonly used conductive agents for lithium batteries mainly include carbon black, conductive graphite, VGCF (gas phase grown carbon fiber), carbon nanotubes and graphene. Among them, carbon black, conductive graphite and VGCF are traditional conductive agents, which form point, surface or line contact type conductive network between active substances. Carbon nanotubes and graphene are new conductive materials, in which carbon nanotubes form a wire contact conductive network between active substances, and graphene forms a surface contact conductive network between active substances.
Conductive agent content in anode material to the theory of seepage threshold, i.e. without adding or adding a small amount of guide electrical agent, conductive material cannot build effective conductive network, when adding quantity increased to a certain value, the conductive material mass energy can be formed in the active substances in the anode materials conductive network effectively, improve the conductivity of the anode material, Furthermore, increasing the content of conductive agent can not significantly improve the conductivity of the cathode material. Due to the new conductive material formed between the active substances in the line contact type, surface contact type conductive network is more sufficient, can more obviously improve the conductive property of the active material of the cathode material, and then reduce the amount of conductive agent in the cathode material. According to Sanshun Nano's prospectus, the amount of traditional carbon black conductive agent is generally about 3% of the weight of the cathode material, while the amount of new conductive agent such as carbon nanotubes and graphene can be reduced to 0.5% to 1.0%.
As a hollow tubular structure, carbon nanotubes can improve the liquid absorption of the electrode, thus reducing the electrolyte loss in the use of the battery, and improving its life performance. In addition, compared with traditional conductive agents, carbon nanotubes have better conductivity, thermal conductivity and structural strength, so as to maintain good electron and ion conduction during the cycle of lithium battery, thus greatly improving the cycle life of lithium battery:
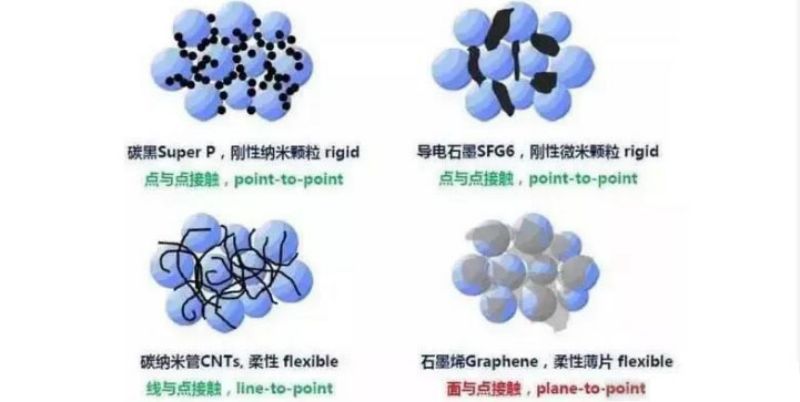
Schematic diagram of conductive agents of different contact types
(1) Advantages of conductivity:
The carbon atoms of carbon nanotubes form a basic monomer structure in a regular hexagonal microscopic form. In this structure, the conjugation effect is significant, and electrons can break away from the bonds of a single carbon atom and move freely in a wide range; Carbon nanotubes are similar to fibers, and their fibrous structure can form a continuous conductive network in the active electrode material. The same conductive effect can be achieved with the amount of carbon nanotubes only 1/6-1/2 of the traditional conductive agent. In addition, carbon nanotubes have double layer effect, which can effectively improve the rate performance of lithium battery.
(2) Thermal conductivity advantages:
Carbon nanotubes have excellent thermal conductivity, which can rapidly conduct heat along the length of the tube. Their good thermal conductivity also contributes to heat dissipation during battery charging and discharging, reduces battery polarization, improves battery high and low temperature performance, and improves battery cycle performance;
(3) Structural strength advantage:
Carbon nanotubes have extremely high strength and toughness, and the addition of carbon nanotubes has high toughness, which can improve the spalling caused by material volume changes in the charging and discharging process and improve the cycle life.
Although carbon nanotubes are obviously superior in performance, the market of conductive agent in China is still dominated by traditional conductive agents such as carbon black and conductive graphite. According to statistics show that in 2020, China's conductive agent market accounted for nearly 80% of the traditional conductive agent. As a new material, carbon nanotubes have a high price in the early stage of market application, which is the main obstacle for carbon nanotubes to replace carbon black as the mainstream conductive agent in the early stage of power lithium battery. According to the prospectus of Tiannai Technology, in 2018, the powder prices of carbon nanotubes and SP were 450-550,000 RMB/ton and 56-65,000 RMB/ton respectively, and the price of carbon nanotubes powder was nearly 10 times that of carbon black. In addition, carbon nanotubes need to be dispersed into a paste and then imported into the battery, so the cost of conducting carbon nanotubes is much higher than that of carbon black. Although the amount of carbon black is less than that of carbon black in lithium batteries, due to the influence of the current high unit price, the lithium cell manufacturers still need a gradual acceptance process for the use of carbon nanotube conductive agent.
The 4680 battery has high compatibility with the high nickel anode + silicon base anode material system. In order to improve the energy density of the battery, high nickel anode materials and silicon carbon anode materials are applied to the battery material system, but the poor thermal stability of high nickel materials and high volume expansion rate of silicon carbon materials bring a test to the safety of the power battery. Compared with square cells and pouch bag, cylindrical battery structure itself strength is higher, to the expansion of the silicon carbon anode tolerance is higher, the characteristics of good heat dissipation performance and cylindrical battery can to a certain extent, make up for the poor thermal stability of high nickel material lack of points, so in the carbon anode materials in the application of high nickel materials and silicon, cylindrical battery obvious advantages. In addition, compared with small cylindrical batteries, 4680 batteries have advantages of high energy density and low cost, and the trend of large-scale cylindrical batteries is clear. 4680 battery volume will promote cost reduction and efficiency improvement of the industrial chain, and promote the penetration rate of high nickel cathode and silicon based anode.
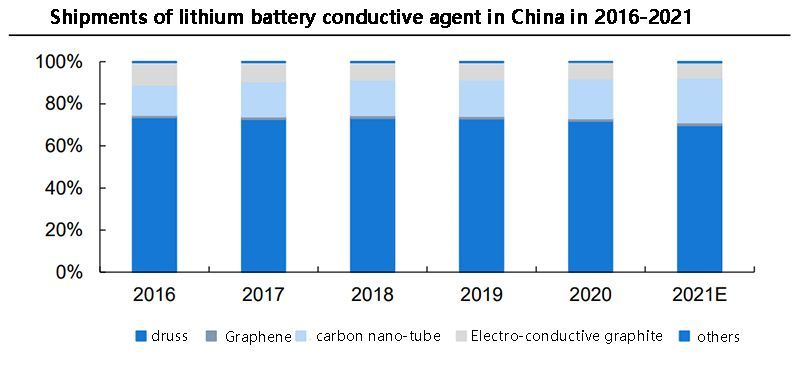
Due to carbon nanotubes have excellent electrical conductivity, thermal performance and structural strength, 4680 battery capacity with high nickel and to the cathode + silica based anode market demand trends will create carbon nanotubes:
(1)excellent electrical conductivity of carbon nanotubes can make up for the high nickel ternary cathode and silicon electrode itself defects of conductive performance is poor;
(2)Carbon nanotubes have high structural strength and high toughness, which can improve the SPalling of SEI layer caused by volume expansion effect of silicon material in the process of charge and discharge, thus improving the cycle life of the battery;
(3)Carbon nanotubes have excellent thermal conductivity, which helps to dissipate heat during charging and discharging of batteries, and can make up for the defect of poor thermal stability of high-nickel ternary materials;
(4)Compared with carbon black, carbon nanotubes can further improve the rate performance of lithium batteries by virtue of their high aspect ratio and double layer effect.
(5)Carbon nanotubes can further improve the energy density of lithium-ion batteries by increasing the filling amount of cathode and anode active substances with less additive amount. In the future, with the proliferation of 4680 batteries and the popularization of large-scale industrialization of carbon nanotubes, carbon nanotubes with excellent performance are expected to accelerate the replacement process of carbon black. It is predicts that carbon nanotubes will account for 55% of China's conductive market by 2025.
3.4.2 Technology and performance to build core competitiveness, leading companies expand capacity
Because the production of qualified carbon nanotube conductive agent has a high requirement on the comprehensive strength of carbon nanotube conductive paste enterprises, the concentration of carbon nanotube conductive agent industry is high, CR5 is close to 90%. As a conductive agent for power lithium battery, carbon nanotube conductive paste not only requires high aspect ratio and purity of carbon nanotubes, but also puts forward higher requirements for dispersion technology of carbon nanotube conductive agent manufacturers. At the same time, lithium cell enterprises have strict inspection procedures for conductive paste suppliers, and comprehensively evaluate their product quality, stability, uniformity and sustainable supply ability. Therefore, they have high requirements for comprehensive strength of carbon nanotubes conductive paste enterprises, so the concentration degree of carbon nanotubes industry is high. According to statistical analysis, the top three companies in China's carbon nanotube conductive paste shipments in 2020 are Tiannai Technology, Jiyue Nano and Cabot (acquiring Sanshun Nano), with market share of 32.3%, 23.8% and 19.6%, CR3 and CR5 are 75.7% and 89.2%, respectively. Industry concentration is high.
The preparation of catalyst and dispersion of carbon nanotubes are the key steps and difficulties in producing carbon nanotubes conductive agent. The key step of the preparation of carbon nanotubes powder is the preparation of catalyst, because the growth of carbon nanotubes depends on catalyst, the quality and performance of catalyst will directly affect the quality of the subsequent production of carbon nanotubes powder. At the early stage of the promotion of carbon nanotubes as a conductive agent, they were provided to lithium battery manufacturers for trial use in the form of powder. However, due to the high specific surface area and large aspect ratio of carbon nanotubes, agglomeration phenomenon is easy to occur, and it is difficult to directly disperse carbon nanotubes evenly in the electrode material of lithium battery. Therefore, in the production process of lithium battery, carbon nanotubes are usually separated and dispersed in a specific solvent to make conductive paste of carbon nanotubes and then used. The dispersion process is the difficulty of preparing conductive paste of carbon nanotubes.
The preparation technology of carbon nanotube catalyst mastered by Tiannai Technology can control the directional growth of carbon nanotube and directly control the diameter, length and purity of carbon nanotube. Of tsinghua university "based on the principle of nanometer poly group fluidization is high purity carbon nanotube bulk preparation of basic research" in principle to solve the carbon nanotube continuous production, preparation of macro day nai technology to achieve the above invention patents related to the study of the exclusive licensing rights, laid the company product industrialization on the basis of the first generation of carbon nanotubes. After the industrialization of the first generation of carbon nanotubes, inspired by the concept of layered support catalyst from Tsinghua University, Tiannai Technology independently developed the second generation of directed growth catalyst with controllable length of carbon nanotubes through the selection and optimization of catalyst active elements and cocatalytic elements and surface modification of the carrier. Under the action of this kind of catalyst, the diameter of carbon nanotubes is controlled by the particle size of catalyst active center, and the length of carbon nanotubes grown is controllable, so the length of carbon nanotubes produced is large. Tiannai technology independently developed the third generation of spinel based composite structure catalyst, in addition to further improve the length to diameter ratio of carbon nanotubes to enhance the conductivity, but also improve the carbon purity of the product. The carbon nanotubes have lower residual metal content and better electrical conductivity.
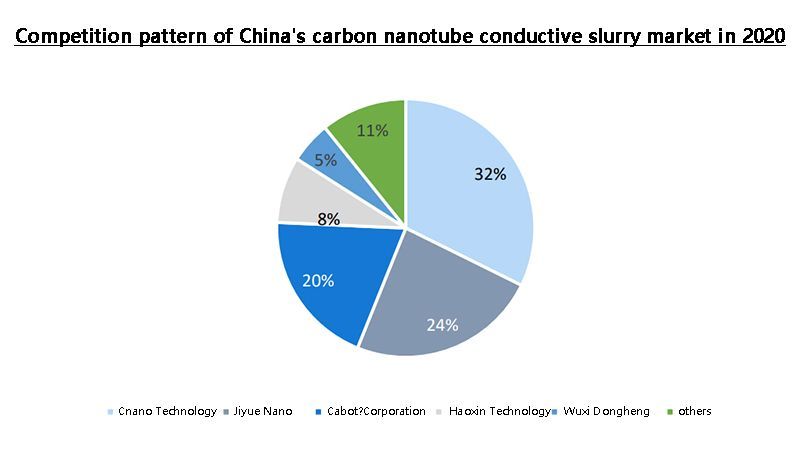
Tiannai Technology accelerated capacity expansion, deep binding lithium customers in a stable leading position. At present, the company has an annual production capacity of 2000 tons of carbon nanotube powder and 30,000 tons of carbon nanotube conductive paste, which has exceeded other companies in the same industry in China. With the rapid growth of the demand for high nickel cathode and silicon carbon anode of power battery, the permeability of carbon nanotubes will increase. In order to meet the demand for carbon nanotubes, Tiannai Technology actively plans to expand production. In terms of future capacity additions, The new production capacity in the future mainly comes from "annual output of 300 tons of carbon nanotubes, 2,000 tons of conductive masterbatch, 8,000 tons of conductive paste project", "Carbon nanotubes and by-product hydrogen and related composite product production project", "Carbon nanotubes composite product production project" and "annual output of 8,000 tons of carbon nanotubes conductive paste production line item". When the project is completed, it is expected that the annual production capacity of carbon nanotube conductive paste will reach 106,000 tons in 2027. After years of development, the day nai technology on carbon nanotubes and conductive paste market has already formed the brand competitive advantages in many aspects, technology, talent reserves, nuclear heart to accumulate a batch of stable customers, with the CATL, byd, ATL, CALB and EVE. Tiannai Technology, which is deeply bound to a number of major lithium customers, is expected to steadily expand the market scale after the project is completed and further improve the company's market share.
4.Structural parts: 4680 battery demand increase, open the incremental space of cylinder structural parts
4.1. 4680 batteries have broad prospects, and the cylindrical structural parts market is expanding rapidly
The precision structural parts of lithium batteries mainly include the shell and top cover of lithium batteries. The precision structural parts account for 10-16% of the cost of battery materials, and are one of the important components of lithium batteries. As the outer shell of lithium battery, precision structural parts play the role of energy transmission, carrying electrolyte, safety protection, fixed support battery, appearance decoration and so on. Therefore, as a key component of lithium battery, precision structural parts need to have high dimensional accuracy, high surface quality, high performance and other characteristics.
According to the different battery packaging technology route, the corresponding structural parts of cylindrical battery, square battery and pouch package battery are divided into cylindrical structure parts, square structure parts and aluminum plastic film. The cylindrical and square structure parts are collectively referred to as hard shell, usually steel shell or aluminum shell.
The shell is an important part of the battery shell as the barrier of the whole life cycle between the active substance in the cell and the outside world. Cylindrical shell specifications and models are relatively uniform, according to the size of the battery is divided into 18 series, 21 series, 26 series and 46 series. The standardization degree of square shell is low, and the specifications and models are scattered.
Cylindrical battery cover (safety valve) is mainly used for power outage and pressure release when the battery is overloaded to prevent the explosion caused by high internal pressure of the battery. It is an essential part for safety protection of lithium battery and other high energy density batteries. Cylindrical battery top cover is composed of sealing ring, explosion-proof aluminum sheet, steel cap, isolation ring and connecting aluminum sheet, the working principle of each component is as follows:
(1)Sealing ring:
located outside the safety valve, mainly plays the role of sealing battery and isolation package shell and safety valve;
(2)Steel cap:
located at the top of the safety valve, used for protection of explosion-proof aluminum sheet and connection between the battery pack;
(3) Explosion-proof component:
it is composed of isolation ring, explosion-proof aluminum sheet and connecting aluminum sheet. When the internal pressure of the battery reaches the critical value, the circuit is disconnected in time and the internal pressure of the battery is released, so as to realize the explosion-proof function.
4680 batteries will increase the demand for cylindrical structures, with a CAGR of 32% in 2021-2025. The market size of power battery structural parts is calculated according to the demand for power battery, the penetration rate of cylindrical battery, the cost of lithium battery shell/top cover of CATL and the battery sales of CATL. The specific assumptions and calculation are as follows: According to the prospectus of CATL, the cost of purchased shell/top cover was about 723 million RMB in 2017, while the sales volume of CATL battery in that year was 11.84GWh. It is estimated that the price of lithium battery structural parts in 2017 is about 61 million RMB /GWh. According to the change of unit sales price of power battery in CATL from 2019 to 2020, it is assumed that the unit price of power battery drops 7.5% annually; Assuming that the cost ratio of structural components remains unchanged, it is assumed that the unit value of structural components will decrease 7.5% annually from 2017 to 2025. It is estimated that the market space of cylindrical structure parts of power battery will reach 11.77 billion RMB in 2025, increasing by more than 200% compared with 2021, and the CAGR will reach 32% in 2021-2025.
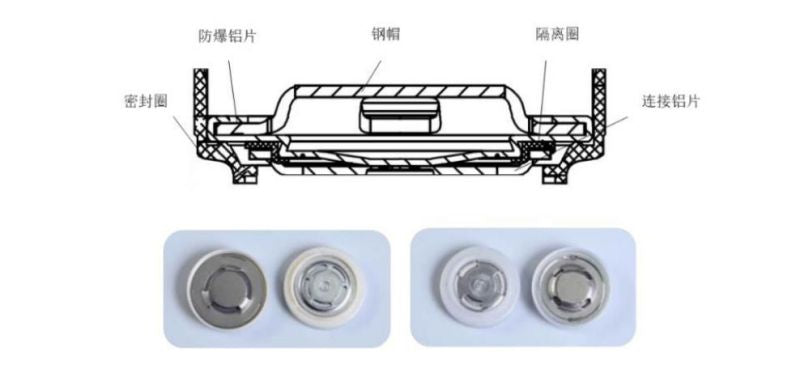
Schematic diagram of the cylindrical battery top cover (safety valve)
The trend of 4680 battery leads to the reduction of unit battery structure cost, which helps the profitability of structural parts manufacturers and the cost reduction of the industrial chain. Benefiting from the continuous growth of cylindrical structural parts market, cylindrical structural parts manufacturers are expected to steadily increase shipments. By in powered lithium battery power battery for precision components quality, performance and security of all has the very high request, power lithium battery precision components suppliers before entering the lithium battery production procurement system must be through the strict certification process, after certification, battery companies won't easily switch suppliers, structure enterprise high binding with battery business. Therefore, leading enterprises in structural parts are expected to benefit from the growth of downstream demand and further improve their market share. In the trend of large-scale cylindrical batteries in the future, the consumption of single GW structural components will be reduced, and the cost of unit junction components is expected to be further reduced, which will help improve the profitability of structural component manufacturers and reduce the cost of the industrial chain.
4.2 Technical barriers to build the industry moat, production equipment enterprises appear technological advantages
Precision structure parts of power battery (including top cover and shell) are stamping parts processed by stamping. Stamping processing refers to the use of mold installed in the press to exert deformation force on the material deformation or separation of a pressure processing method. Power battery precision components of semi-finished products from silicon steel, aluminum, copper belt clamp force to produce precision structural deformation or separation is the key step in the production, and the stamping process through the analysis of stamping die is completed, so the result of the stamping die determines the efficiency of stamping, stamping major aspects, so the mold technology is the core of the production of precision components technology.
In precision mold design and manufacturing, mold quality determines the precision and quality of the product, especially the key processing and manufacturing technology of the core components explosion-proof sheet and reverse sheet. At the same time, due to the current power lithium battery product specifications, models and types, each product needs to manufacture molds independently, enterprises with strong mold development ability may timely respond to customer needs, mold development enterprises have innate advantages in the field of structural parts. Chinese enterprises slacker and Zhenyu Technology are traditional mold development enterprises, and then enter the field of lithium battery structural parts by virtue of the advantages of mold development.
The production technology of battery precision structural parts has an impact on the safety, life, consistency, connectivity and battery capacity of lithium batteries:
(1) Safety:
safety and explosion-proof technology of structural parts can avoid or reduce safety accidents caused by excessive battery pressure when abnormal electrochemical reaction inside the battery occurs;
(2) Service life:
the sealing technology of structural parts in high and low temperature state can reduce the leakage failure of cathode and anode poles in battery service state, thus improving the safety and service life of the battery;
(3) consistency:
the use of automatic assembly, welding, riveting, detection function, traceability system in one of the cover plate automatic assembly technology and precision tensile technology to make aluminum shell production precision, product consistency is better;
(4) connectivity:
the copper and aluminum pouch connection technology can overcome the loosening or shedding problem of the connection between the battery and the battery of new energy vehicles in the rough use conditions such as turbulence and vibration, enhance connectivity and reduce circuit breakers;
(5) Capacity:
On the premise of maintaining the strength of the shell, the deep drawing technology of the aluminum shell can improve the tensile strength of the aluminum shell, and the strength is not affected while the wall thickness is thinner, so as to increase the battery capacity per unit volume.
The production of battery precision structural parts belongs to the integration of multiple technologies, integrating the technologies of metal materials, mechanical engineering, mold development, chemistry, electronics, electromechanical, precision control and other disciplines. The technical level of each link will have a direct impact on the quality and performance of the product. At the same time, the manufacturing process and quality control of precision structural parts need to accumulate production experience through a large number of production practices, especially in the early stage of product research and development, mold development and rapid response to different products of customers, etc., need to accumulate profound industry experience before good docking and cooperation with downstream customers; In addition, the precision structure of power lithium battery has higher requirements on product precision, quality, consistency and manufacturing process, and the production process is generally guaranteed by precision production equipment and high level of production environment. Therefore, it is difficult for new enterprises to realize interdisciplinary integration and master core processes and key technologies in a short period of time. The high comprehensive technical accumulation requirements of battery precision structural parts create high technical barriers in the industry.
Power lithium battery precision structural parts as an important supporting industry of power battery, due to the high concentration of downstream lithium battery production industry, the market pattern of power battery precision structural parts is relatively concentrated, the industry presents a super many small market pattern, Codali global market share of more than 40%. Other companies in the industry include Sangsin EDP (South Korea), FUJI SPRINGS (Japan), Jinyang Co., LTD., Zhenyu Technology co., LTD., Slack, etc., with relatively scattered market shares.
Codali has been deeply engaged in the power battery precision structural parts industry for many years and has the most extensive customer base in the industry. Customers cover CATL, Panasonic, LG, BYD, EVE, AVIC Lithium and other high quality power lithium battery manufacturers. Division of Dali in east China, south China, northeast China, the China lithium battery industry such as key areas and outside Germany, Sweden and Hungary have formed the global capacity layout of 12 production bases, the total reaches producing production base including production base in huizhou 1st and 2nd stage, first phase of the production base in jiangsu, and the original production base in shenzhen, Shanghai, west Ann. The capacity expansion of these production bases will form an effective support for the increasing capacity demand of Codali customers, and meet their capacity expansion demand at the fastest speed. After more than 20 years of development, Codali has accumulated rich product and technical experience in the field of precision structural parts of power batteries. With high precision and high consistency production process, codali is capable of producing precision structural parts of 4680 batteries. In the future, with 4680 battery battery volume, Codali is expected to provide customers with 4680 battery battery precision structural parts deeply bound with downstream leading enterprises, further improve the company's market competitiveness and market share, to ensure sustainable profitability.
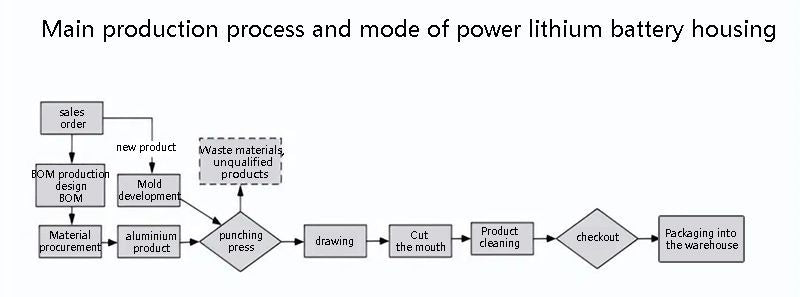
Slack takes advantage of the can field to expand the power battery structural parts business. The structure of the cylindrical battery is similar to that of the two-piece can. The production equipment is basically the same as the technology used in the production equipment of the can. The slacker power battery structure production equipment only needs to be partially adjusted on the basis of the existing high-speed production equipment of the can. At present, slacker's high speed production line has the highest production efficiency of 3000 cans/min, and the product performance is in the forefront of the international. With its r&d achievements and production experience accumulated in the field of easy-pull cover and tank production equipment, Slacker launched the production speed of power battery structural parts production equipment is 1200 PCS/min, much higher than 50 PCS/min of China equipment and 150 PCS/min of imported asahi precision machine. Increasing the production speed of structural parts production equipment can reduce the amount of equipment invested, thus avoiding or reducing the consistency problems caused by the production of different equipment and the problems of labor intensive and high production cost in mass production.
In addition, the high precision and innovative process of the battery case production line developed by Slacker makes the high finish battery case (called "mirror case") more suitable for the high quality of the power battery field. Under the background of the upgrading of China's manufacturing industry, the rapid development of new energy vehicle industry and the large-scale demand for new energy batteries, Slack battery case production line is expected to have an impact on the existing traditional single-machine punch production process of battery case. In addition, the 4680 cylindrical shell is similar in size to the 330ml can (58mm in diameter and 102mm in height), and the production line layout is similar. Slater's production of 4680 battery has a unique advantage that no other company in the industry has.
5. Investment analysis
With the advancement of battery technology, the improvement of product strength and the continuous improvement of infrastructure, the penetration rate of new energy vehicles accelerates, driving the release of power battery demand. The large-scale development of power battery will further promote the reduction of industry cost, making the development of new energy vehicles form a cathode feedback.
4680 battery is expected to start mass production next year to support some Models of Tesla. We pay attention to battery manufacturers with 4680 battery production capacity. Because 4680 battery has high adaptability with high energy density materials, Attention is paid to the growth opportunities of high-nickel cathode, silicon-based anode, LiFSI and carbon nanotube links in the lithium electric industry chain brought by the capacity expansion of 4680 battery, as well as the increasing demand of 4680 battery for cylindrical structure parts. In addition, because the large cylindrical full pole lug technology adopts laser cutting and laser welding, it will be beneficial to laser welding and cutting equipment.