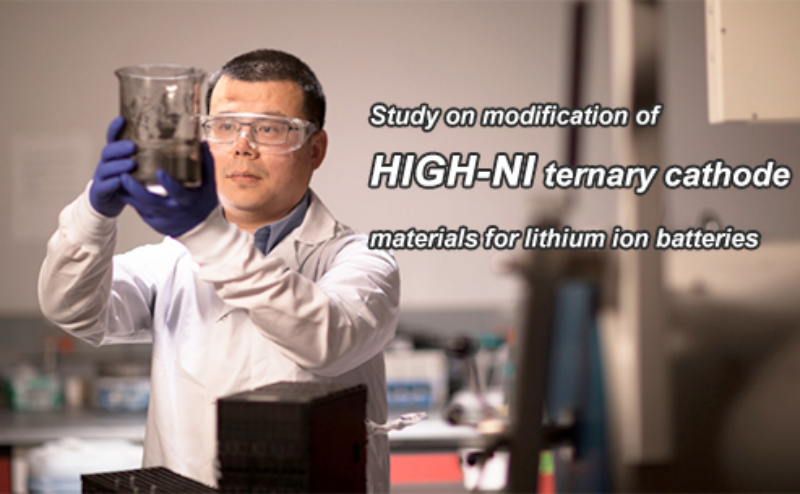
With the rapid development of new energy power vehicles and energy storage technology industries, higher requirements have been placed on lithium-ion batteries in terms of energy density, cycle stability and price. As the most critical material of lithium ion battery pack, the cathode material determines the performance and cost of the battery. LiNixCoyMn1-x-yO2, NCM, a high-Ni cathode material, which combine the advantages of three layered LiMO2 (M=Ni, Co, Mn) materials, are one of the most commercially valuable cathode materials.
Although high-Ni ternary cathode materials are considered by most scientific researchers and the electric vehicle industry as the most promising cathode materials for lithium-ion batteries. However, in practical production applications and scientific research, there are still many deficiencies in high-Ni ternary cathode materials. In pursuit of higher performance, the Ni content of high-Ni ternary cathode materials needs to be continuously increased, and 4 problems are exacerbated:
- The mixed arrangement of cations between Li and transition metals, mainly Li+/Ni2+, will seriously interfere with the migration of Li ions;
- Formation of microcracks during long-term cycling;
- Surface side reaction problems, resulting in a variety of side reaction products;
- The thermal stability is poor, and the electrochemical performance declines significantly under high temperature environmental conditions.
These problems seriously restrict the commercialization and large-scale application of high-Ni ternary cathode materials. In order to improve its performance, it is mainly modified by bulk doping, surface coating, single crystallization and gradient structure.
1.bulk doping
Bulk doping stabilizes the layered structure of the material by incorporating other elements, and enhances the thermal stability of the H3 phase from the microstructure, thereby improving the long-term cycling and electrochemical performance of the material under high current density. The choice of different doping elements can play different roles in the material, so the doping methods can be divided into three types: cation, anion and anion-cation synergistic doping.
Cationic doping is to preferentially occupy Li or Ni sites by doping elements to stabilize the layered structure of the material and improve the cycle stability of the material. Low-valence cations (such as K+, Mg2+) are preferentially doped into Li sites to stabilize the lattice structure by preventing Li+/Ni2+ intermixing, but adversely affect the material discharge capacity. Anion doping is to increase the bonding strength between transition metal elements and anions by replacing oxygen elements with more electronegative elements.
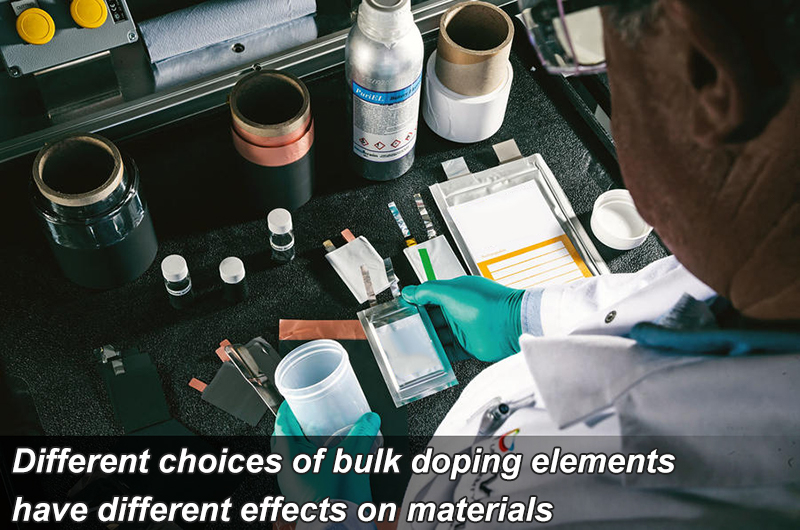
Commonly used doping anions are F-, Br-, BO33- polyanions, etc. Among them, the radius of F atom and O atom are closer to show better modification effect, which can effectively inhibit the dissolution of transition metal elements and avoid electrolyte reaction. The corrosion of the by-product HF plays a role in stabilizing the cathode-electrolyte interface and improving the cycle performance of the material.
Anion-cation co-doping is to select one or more anions and cations at the same time, such as Na-F, Mg-F, P-F, etc. This method combines the advantages of doping anions and cations, and can improve the high temperature, Cycle and rate capability. Bulk doping can stabilize the material structure from the microscopic level, improve the electrochemical performance, and has less difficulty in operation and obvious modification effect.
2.Surface coating
Surface coating is to physically or chemically treat the surface of the cathode material to isolate the cathode material from the electrolyte and prevent the cathode material from direct contact with the lithium ion battery electrolyte to cause side reactions. Furthermore, the electrochemical properties such as dispersibility, thermal stability and discharge rate of the cathode material are improved.

If you want to improve the electrochemical performance of the cathode material by surface coating, it is necessary to choose appropriate materials and coating methods. At the same time, it is necessary to protect the structure of the cathode material to prevent the lattice of the active material from being damaged during the charging and discharging process. The most commonly used surface coating materials are: carbon materials, phosphates, fluorides, metal oxides, etc.
3.Single crystallization
Single crystallization is a modification strategy proposed for the secondary particles of high-Ni ternary materials that are easily broken, pulverized, and easily reacted with the electrolyte. At present, high-Ni ternary products are secondary particles formed by agglomeration of primary particles, and the compaction density is small. It is easy to break when the pressure of the battery pole piece is too high or under high pressure working conditions, which increases the contact and reaction between the internal primary particles and the electrolyte, accelerating the capacity decay and causes gas production problems.
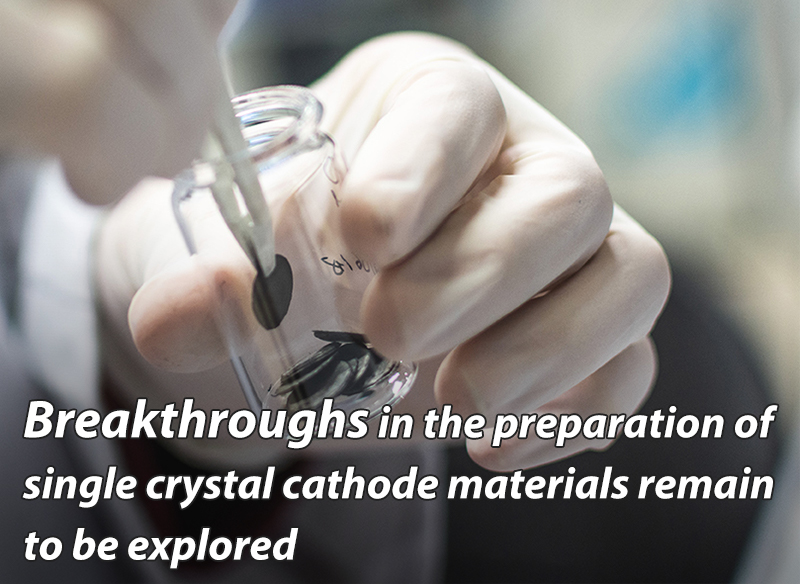
If single crystals can be grown purposefully by controlling the reaction parameters, it can not only improve the compaction density, but also ensure that the material achieves better safety and cycle performance. Commonly used single crystal preparation methods are co-precipitation-high temperature solid phase method and co-solvent method. Although single crystal materials show excellent characteristics in terms of cycle stability and capacity retention, the experimental parameters are difficult to control, and it is difficult to prepare single crystal pure phases. Moreover, due to the small particle size of single crystal particles, the discharge specific capacity is still difficult to meet the actual requirements, so it is still necessary to explore breakthroughs in the preparation of single crystal cathode materials.
4.Gradient structure
The gradient structure is derived from the core-shell structure. In traditional core-shell structural materials, the core (rich Ni) and shell (rich Mn) play the role of providing specific capacity and stabilizing the material structure, respectively, but the content of the internal and external components is large, and faults will appear between the core and shell after long-term cycling, resulting in destroy the Li+ transport channel, causing severe capacity fading. On the other hand, the concentration gradient structure makes the core-shell composition change gradient from the inside to the outside on this basis, which improves the structural fracture caused by the large difference between the core and the shell composition.
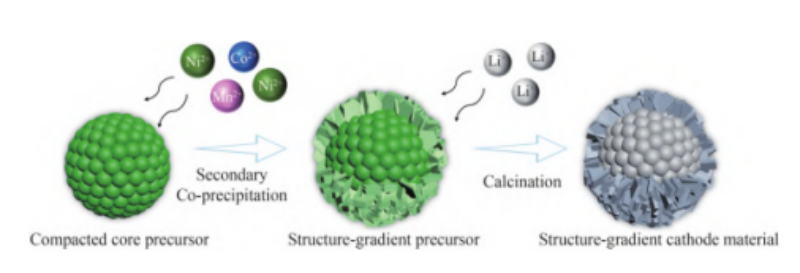
Schematic diagram of the synthesis of structurally graded LiNi0.8Co0.1Mn0.1O2 cathode materials
5.Summary
Among many modification methods, bulk doping and surface coating strategies are simple and easy to control, and are mostly used in industry. However, the effect of single modification is still not ideal. Currently two methods are used at the same time to achieve the effect of co-modification. The single-crystal material exhibits significantly improved structural stability and electrochemical performance, but is still in the research stage due to factors such as low specific capacity and difficult control of process parameters, and exploring a simple and controllable single-crystalization method is a difficulty in future research.
The concentration gradient proposed for the instability of the material structure is a relatively novel direction at present, and the scientific design of the transition metal concentration gradient will hopefully become the next generation of high-Ni ternary material technology solutions. After reading the introduction of high-Ni ternary cathode materials in this article, you may be interested in the layout of the ternary cathode material industry. Reading the Top 10 lithium battery ternary material companies on our website will help you better understand the dynamics of the ternary cathode material industry, this article details the information on the leaders in the field of ternary cathode materials.