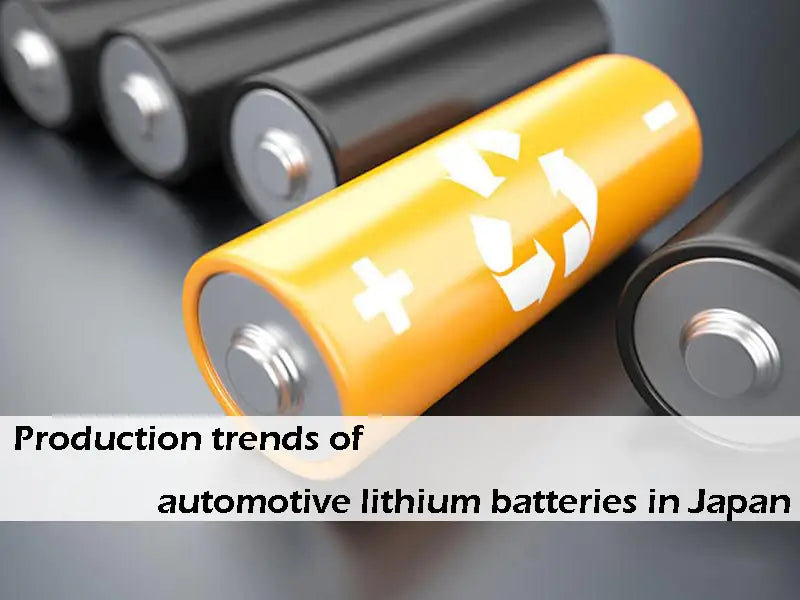
Main content:
At present, Japan's major automobile and battery companies have invested in the construction of vehicle lithium-ion power battery production lines, which will be put into production in 2010-2011. Japan's Fuji Economy believes that lithium-ion batteries will gradually replace nickel-metal hydride batteries in 2011, and there is no doubt that lithium-ion batteries will be the mainstream technology route in the future.
However, in the short term, the automotive power battery market will not use all lithium batteries. After the lithium battery technology matures, the nickel-metal hydride battery market will be gradually replaced by lithium batteries. Although lithium-ion power batteries are difficult to replace oxygen power batteries in 2 to 3 years, it cannot be ignored that lithium batteries will replace nickel-hydrogen batteries and become the mainstream of new energy vehicles in the future. After 2012, with the establishment of the absolute advantages of lithium batteries in technology, cost and market, the growth rate of demand for nickel-metal hydride power batteries will be greatly reduced or even shrink.
According to the Japan Automobile Research Institute, the number of hybrid vehicles in Japan will reach about 3.6 million by 2020, based on the current popularity of hybrid vehicles. If high-performance lithium batteries are more popularized, the usage may increase to the level of 7.2 million vehicles. And the Ministry of Economy, Trade and Industry disclosed that Japan strives to use new lithium batteries for next-generation electric vehicles in 2010.
1. Production trends of lithium-ion batteries in Japan in 2009
On May 15, 2009, Toyota, Nissan Motor Corporation and Panasonic Electric Corporation and other related companies signed an agreement to jointly develop a new generation of automotive lithium batteries with unified specifications, and plan to achieve mass production within 2 years. At the same time, Toshiba has also decided to spend 50 billion yen to develop lithium-ion batteries for electric vehicles. This high-efficiency power will enter semi-commercial production within two years. It plans to increase high-performance lithium-ion batteries to suit different characteristics by 2011. The three types of lithium-ion batteries will be developed to support high-output and high-energy-density lithium-ion batteries such as hybrid vehicles and electric vehicles, in addition to the current ordinary types.
Japan's two major industrial giants, Nissan and NEC, together spent 20 billion yen, in the world's first mass production of lithium-ion batteries for environmentally friendly vehicles such as hybrid vehicles and electric vehicles. The two companies jointly established a plant in Kanagawa, south of Tokyo. The new plant was put into operation in early 2009. The initial lithium battery output can provide 10,000 hybrid or electric vehicles, and the future output will increase by five times. In April 2007, Nissan and NEC formed a joint venture "Automotive Energy Supply Company", "Automotive Energy Supply Company" at the same time to Nissan and its French partner Renault to provide this lithium battery. Nissan hopes to narrow the gap with its main rivals Toyota and Honda in the field of eco-friendly vehicle technology by developing the next generation of eco-friendly vehicle batteries. Nissan and NEC plan to launch electric sedans in Japan and the U.S. starting in 2010.
Volkswagen of Germany and Sanyo Electric of Japan announced in mid-March 2008 the development of lithium-ion batteries, key components for hybrid and electric vehicles. Volkswagen expects to start importing the batteries in 2012. The cooperation with Sanyo Electric will enable Volkswagen to develop economically friendly vehicles.
Toyota Motor Corporation and Matsushita Electric Industrial Co., Ltd. have successfully launched the Prius hybrid model. The Panasonic brand lithium-ion battery has been mass-produced and applied to Toyota Motor Corporation's hybrid vehicle in 2010. Toyota Motor Corporation and Panasonic Electric Industrial Corporation formed a battery joint venture in June 2008 to mass-produce lithium-ion batteries in 2010 for greater use in electric vehicles in the next few years. Toyota Motor Corporation is the world's top manufacturer of gasoline-electric hybrid vehicles. The formed battery joint venture, called Panasonic EV Energy, now produces nickel metal hydride batteries for use in Toyota Motor Corp. hybrid vehicles and is building two new plants. Toyota Motor Corporation, which launched the world's first hybrid car in 1997, aims to sell 1 million units a year globally after 2010, more than doubling its sales in 2007. Toyota Motor Corporation will use rechargeable lithium-ion batteries in hybrid vehicles in Japan, the United States and Europe in 2010.
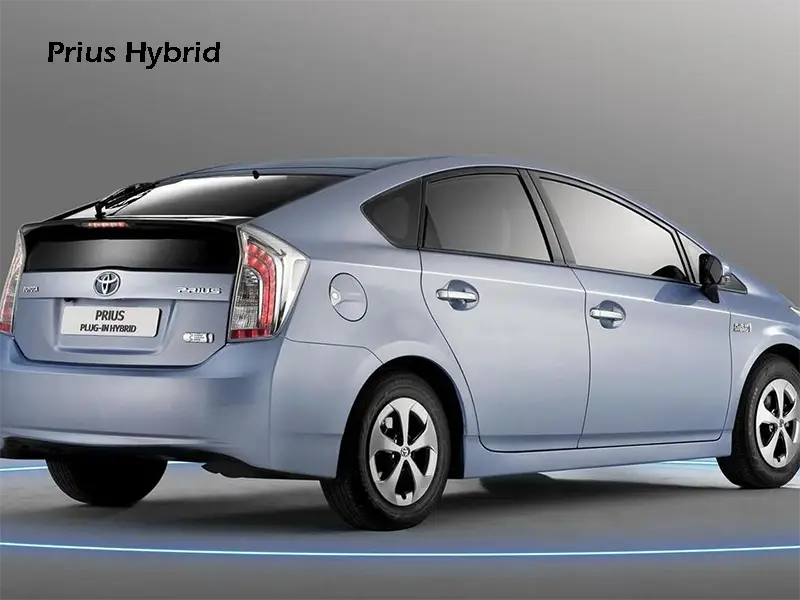
Sanyo Electric Co., Ltd. announced that it will strengthen investment in the research and development and production of lithium batteries for vehicles, and start mass production in 2009. Sanyo said that its Tokushima plant has started trial production of key battery samples for hybrid vehicles since March 2006, and by the end of March 2009, the Tokushima plant had built a mass production line of lithium batteries for vehicles. The plant's production capacity can meet the needs of 15,000 to 20,000 hybrid vehicles, and the products will be supplied to Volkswagen Group's environmentally friendly models. At the same time, Sanyo will also consider building a new lithium battery plant for vehicles in 2010 according to market demand trends. In order to develop and produce new lithium-ion batteries for vehicles with high capacity and long service life, the company will invest a total of 80 billion yen in the next 8 years, and strive to make the production capacity of lithium-ion batteries for new vehicles reach 10 million per month by 2015. Demand for 1.8 million hybrid vehicles. Since the beginning of 2006, Sanyo and the German Volkswagen Group have been working together to develop a new generation of nickel-metal hydride battery systems. The two parties are also working closely in the field of automotive lithium batteries. Sanyo Electric Co. and Volkswagen AG will develop lithium-ion batteries that are smaller than nickel-metal hydride batteries and are expected to be designed for use in vehicles that are lighter than conventional batteries. Sanyo Electric Co. now manufactures nickel-metal hydride batteries, which can be recharged repeatedly, and supplies Honda Motor Co. and Ford Motor Co. Volkswagen and its subsidiary Audi use nickel-metal hydride batteries made by Sanyo Electric in the first hybrid car launched by the Volkswagen Group in 2009.
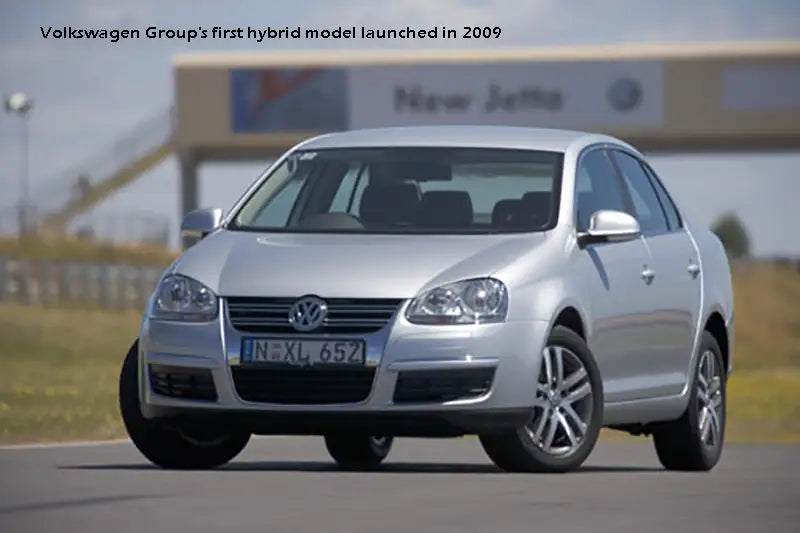
Nissan and NEC announced the joint production of on-board batteries, and Toyota and Panasonic also announced plans to jointly invest in increasing the production of on-board batteries. The addition of Sanyo and Volkswagen's "combination" will undoubtedly further intensify competition in the on-board battery market.
Nissan Motor Corporation and NEC Corporation announced at the end of December 2008 that they would invest 100 billion yen for their joint venture, Automotive Energy Supply, to increase the production of lithium-ion batteries for vehicles, which will be used in a total of 200,000 electric and hybrid vehicles in 2011. The annual output of batteries produced at the AESC plant in Kanagawa Prefecture will initially supply about 13,000 vehicles, and by 2011 will supply 65,000 vehicles.
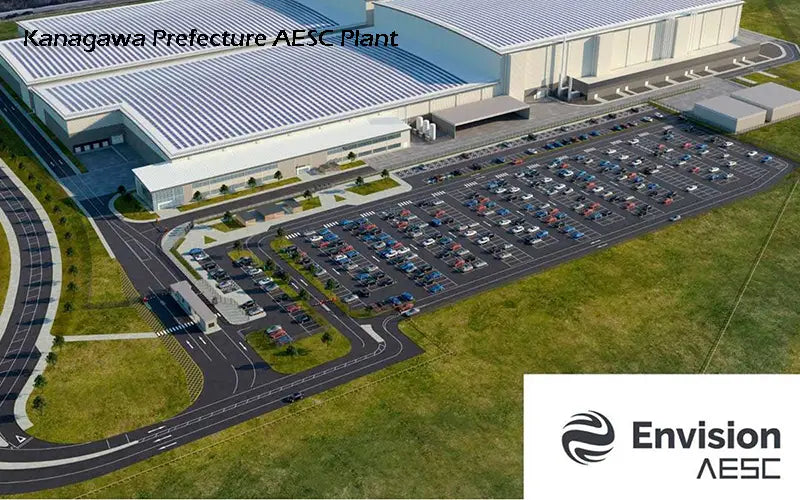
After Japan's Panasonic Corporation announced in July 2008 that it would spend 100 billion yen to build a new lithium battery factory, Sony Corporation also said in August that it would invest 40 billion yen in three years to increase the current lithium battery production capacity by 80%. So far, Sanyo Electric, Panasonic and Sony, the three Japanese lithium battery giants that account for more than 60% of the global market share, have announced plans to increase production. Sony will invest 40 billion yen in its subsidiary Sony Energy Equipment Co., Ltd. in the fiscal years 2008-2010 to build a new lithium battery electrode factory at the Hongu Factory in Fukushima Prefecture, and strengthen the battery at the Kargi Factory. A production line for the core components of components. In addition, Sony has also increased its lithium battery production capacity in China, and since October 2008 began producing lithium batteries for mobile phones in its Singapore factory. Through the above-mentioned series of measures, by the end of 2010, Sony's total production capacity of lithium batteries can be increased from the current 41 million pieces per month to 74 million pieces. At the same time, Sony is also adjusting the supply scheme of lithium batteries in a targeted manner. In view of the popularity of wireless power tools and the continuous introduction of new products such as small and high-power electric shavers, Sony sees the strong demand for lithium batteries in small home appliances, so it will increase the supply in this area. At present, about half of the lithium batteries produced by Sony are supplied to mobile phone manufacturers and about 20% are supplied to notebook computers. Previously, Sanyo Electric and Panasonic have announced plans to build new factories to increase battery production capacity. With the addition of Sony, the competition between Japan's top three in the lithium battery industry and South Korea's Samsung Electronics will undoubtedly intensify.
Panasonic announced on March 2, 2010 that it will begin production of its new 4.0A·h lithium-ion secondary battery in fiscal year 2012, which features a nickel-rich cathode and a silicon alloy anode. The battery was successfully developed in December 2009 and will be mass-produced in fiscal 2013. Initially, it will be used in notebook computers. This 18650-style lithium-ion battery has a high volumetric energy density of 800W·h/L, while the current 2.9A·h battery is 620W·h/L, but the weight density is about 252W·h/ kg, comparable to existing graphite designs. The new high energy density cells weigh about 54g each, which is about 10g heavier than the NCR18650A model. The lithium-ion battery can still maintain at least 80% of its capacity after being charged and discharged 500 times.
Nissan and NEC decided in January 2009 to advance the original production increase plan by one year, and will start mass production of high-capacity lithium batteries for pure electric vehicles and hybrid vehicles after 2011, with an annual production scale of 200,000 units. At the same time, new factories will be established in Japan, the United States and Europe, and the total investment is expected to reach 100 billion yen.
In addition, Honda Motor also established a joint venture with Yuasa Corporation in December 2008 to produce and sell lithium batteries for hybrid vehicles.
Toshiba said in late 2008 that it would build a new plant to increase production of advanced rechargeable batteries used in hybrid and electric vehicles. The plant, which will start production in late 2010, will increase Toshiba's monthly production capacity from the current 150,000 cells to several million cells. Lithium-ion batteries are lightweight and well-suited for use in electronics such as laptops and cell phones, but have the disadvantage of gradually losing their ability to charge, and are often the subject of large-scale product recalls due to safety concerns such as overheating and even explosions . Dongyi said that the new battery it produced is safer than existing batteries, can be charged quickly, and has a longer service life than existing batteries, which can be used continuously for 10 years when charged once a day. The company calls the new battery a "super rechargeable lithium battery" and has already started shipping in April 2008. While the battery can be used in appliances, Toshiba is preparing to expand its application to areas such as electric vehicles and industrial power supply.
GS Yuasa Corporation and Honda Motor Corporation announced on March 24, 2009 the formation of a joint venture to manufacture, sell and develop lithium-ion batteries for hybrid vehicles. The new company formed can manufacture lithium-ion batteries based on GS Yuasa's 6A·h grade EH6 and is ready to develop improved cathode materials and battery structures to optimize the performance of next-generation hybrid vehicles. GS Yuasa Corporation and Honda Motor Corporation hold 51% and 49% of the joint venture, respectively. In addition, GS Yuasa has also formed a joint venture with Mitsubishi Lithium Energy Japan to manufacture high-capacity and high-performance lithium-ion batteries for electric vehicles.
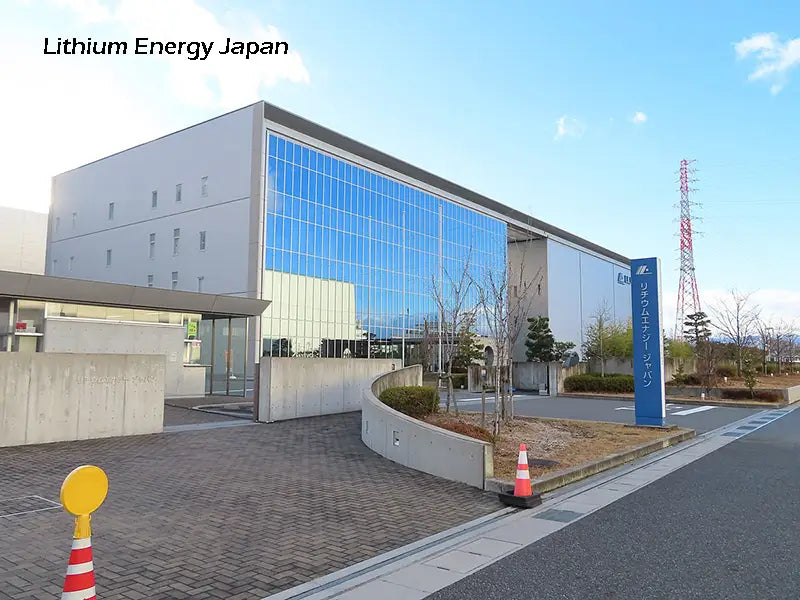
Toshiba is preparing to mass-produce fast-charging lithium-ion batteries for gasoline-electric hybrid vehicles, which have the highest output power among similar batteries. It is reported that Toshiba's SCiB battery power has been tripled to 3900W. This battery can be charged in 90s at the fastest, so it is suitable for use in rechargeable gasoline-electric hybrid vehicles and can be charged more than 10,000 times. Toshiba has already started shipping the battery to large automakers in Japan, the U.S. and Europe for trial use. According to reports, Toshiba has developed a high-power lithium battery for electric vehicles, which can continuously release power for a long time. Samples have been shipped in the fall of 2009. Toshiba is currently producing 150,000 SCiB cells a month, and a factory was built in the fall of 2009. The initial output is about 2 million cells per month, and it hopes to increase to about 10 million cells by 2015.
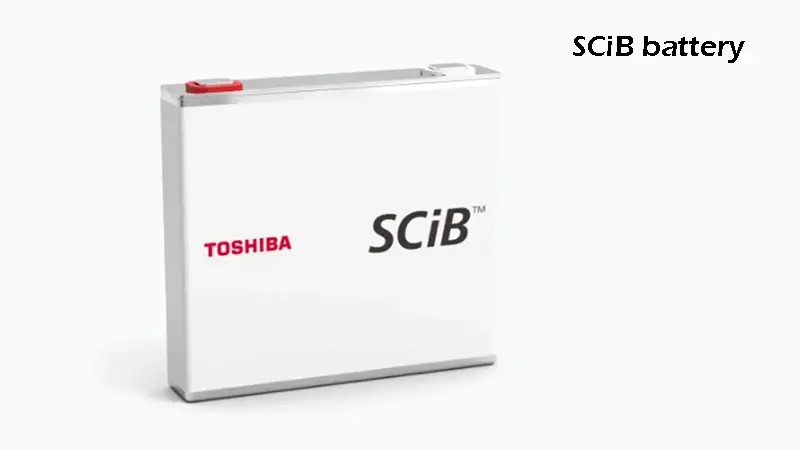
Hitachi disclosed the company's lithium-ion battery business strategy in late April 2009, aiming to achieve 100 billion yen in sales from the automotive battery business by fiscal 2015. The company's batteries are mainly used in fields such as automobiles, consumer products, and industrial machinery, and it plans to expand sales to social innovation businesses in the future. At present, the company's batteries are only provided for some hybrid and electric vehicles, but starting in 2010, it will provide 100,000 vehicles for GM in the United States every year, with sales expected to reach about 100 billion yen. Hitachi Vehicle Energy, which produces on-board batteries, started a production line capable of producing 300,000 units per month in the fall of 2009, and further expanded its production capacity to achieve a scale of 100 billion yen. The company will produce the third-generation vehicle battery in 2010, with higher output density and energy density than the second-generation product. Taking batteries for hybrid vehicles as an example, the output density will be increased from 2 500W/kg in the second generation to 3 000W/kg, and the energy density will also be increased from 60W·h/kg to 70W·h/kg. The on-board battery unit is a cylindrical design, and the cathode material uses the same manganese compound as the original. It is estimated that the sales volume of consumer batteries in 2007 is about 30 billion yen, which will reach 65 billion yen in 2011, of which the consumer battery will be produced by Hitachi Wansheng, and the sales volume of mainstream batteries will reach about 50 billion yen. In addition, cylindrical batteries have been developed, and laminate type batteries are currently being developed. Laminated batteries are mainly used in electric motorcycles, and batteries with a capacity of 10A·h are currently being developed. In the future, Hitachi Wansheng will also develop batteries for electric motorcycles with motors ranging from several hundred watts to about 1kW. In terms of industrial use, it is envisaged to be used for backup power supply and power storage devices, such as construction machinery and hybrid trains, and Shin Kobe Electric is mainly responsible for production. The sales volume in fiscal 2015 is expected to be 13 billion yen, but it will continue to focus on the development of social innovation in the future.
Hitachi announced on April 25, 2009 the development of lithium-ion batteries for high-power hybrid electric vehicles. The characteristic power output density of this type of lithium-ion battery is 4 500W/kg, which is 70% higher than that of existing similar batteries, and 50% higher than that of the new type mass-produced by Hitachi in 2010. Hitachi began commercial production of this new vehicle lithium-ion battery in mid-2010. The service life of this type of lithium-ion battery is 20% longer, reaching 10 years, which is basically the same as that of a car.
Lithium Energy Japan, a joint venture between GS Yuasa and Mitsubishi Motors, announced on May 23, 2009, that it will build a lithium-ion battery production plant for Mitsubishi Motors to increase production for its iMiEV electric vehicle. The joint venture will invest 2 billion to 3 billion yen to build a lithium-ion battery production plant in Kyoto. The battery stacks produced by the plant can be used for 15,000 vehicles a year. Rapid growth, Mitsubishi Motors plans to double iMiEV production to 20,000 units by fiscal 2011. In 2008, Lithium Energy Japan built a production plant in Kusatsu, Shiga County, to achieve mass production of about 10,000 vehicles, and plans to add a second production plant by 2012 to double the output.
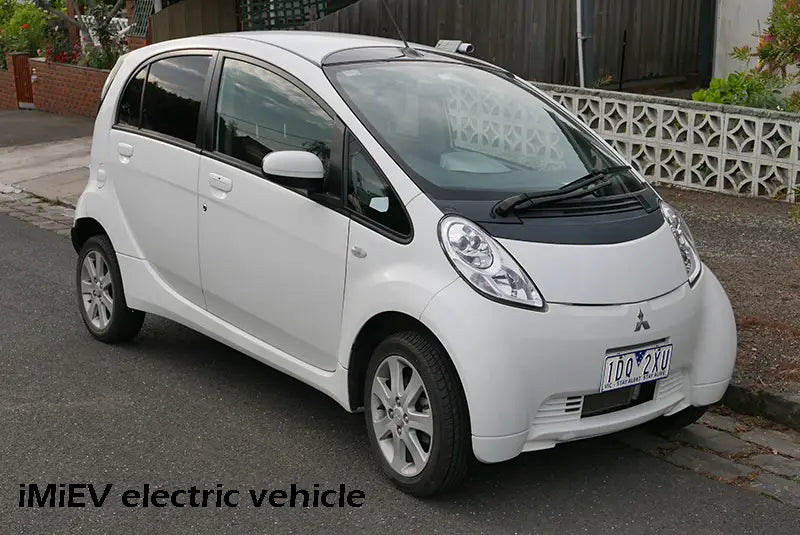
Hitachi announced on July 2, 2009 the expansion of lithium-ion battery production, and will invest 20 billion to 30 billion yen to improve the production capacity of lithium-ion batteries for light-load hybrid vehicles. It is a 70-fold increase in production by 2015. Hitachi has contracted with General Motors to start supplying lithium-ion batteries for its 100,000 hybrid vehicles in 2010. Hitachi has also signed contracts with domestic and other overseas automakers to enable its lithium-ion battery production capacity to meet the annual demand for 700,000 hybrid vehicles. Each vehicle is generally equipped with 30 to 50 sets of lithium-ion batteries.
Hitachi will mass-produce two new types of lithium-ion batteries for next-generation hybrid vehicles that, in addition to vastly improved power output density, are half the weight and size of conventional nickel-metal hybrid batteries. Hitachi manufactures at the company's subsidiary Hitachi Auto Energy's plant in Ibaraki Prefecture.
General Motors has contracted Hitachi to supply lithium-ion batteries for its second-generation Belt Alternator Starter hybrid vehicle system.
Nissan Motor Corporation, NEC Corporation and NEC Tokin Corporation announced on July 16, 2009 the formation of the Automotive Energy Supply Company, a joint venture to manufacture automotive lithium-ion batteries, to produce advanced lithium-ion batteries for a wide range of automotive applications at its inter-seat production center . The initial capacity of AESC's cell stacks is 13,000 units/a. By 2010, the production capacity will be increased to 65,000 sets/a. AESC is now using manganese spiked stone cathode materials to produce laminated lithium-ion batteries. The lithium-ion batteries produced by AESC will be supplied to Nissan Motor Company's electric vehicles entering the US and Japanese markets, and will be used in Nissan Motor Company's hybrid vehicles in 2010. In addition to Nissan, AESC plans to expand sales to global automakers. The lithium-ion rechargeable battery manufactured by AESC uses a manganese-based positive electrode with excellent thermal stability, and adopts a laminated structure with high heat dissipation. The output density is about twice that of the original nickel-metal hydride rechargeable battery. By combining modules composed of laminated units, the product size can be reduced and can be equipped without sacrificing interior space. The real vehicle driving test of the Nissan hybrid vehicle has confirmed that the battery can travel more than 100,000 km, with excellent safety and long life.
2. Production trends of lithium-ion batteries in Japan in 2010
Hitachi and Hitachi Automotive Energy announced on January 12, 2010 that the two companies have developed a lithium-ion rechargeable battery with both high energy density and high output density for plug-in hybrid vehicles. The battery developed this time achieved an energy density of 120W·h/kg and an output density of 2400W/kg. Compared with the batteries for hybrid vehicles that are being mass-produced, the output density is basically the same, and the energy density is about doubled. The dimensions of the battery for PHEV are 146mm x 110mm x 30mm, the weight is 0.75kg, and the average voltage is 3.6V. The company claims that the positive electrode material uses oxides including Mn species; the negative electrode uses carbon material. The company plans to use the cylindrical battery currently in mass production as the second-generation product, and supply the third-generation product to the mild-hybrid vehicle of General Motors in the United States in 2010, and will mass-produce 300,000 units per month. . The third-generation product is a cylindrical battery with a diameter of 40mm × length of 92mm, a current capacity of 4.4A·h, an average voltage of 3.6V, and an output density of 3 000W/kg.
Hitachi Corporation and Hitachi Automotive Energy Corporation announced that they will develop and manufacture lithium-ion batteries for automobiles and supply products to Japanese and overseas automakers from spring 2010. The newly developed battery has a capacity of 25A.h, which is 4 to 5 times the capacity of the lithium-ion battery for hybrid electric vehicles currently developed by Hitachi, with an energy density of 120w·h/kg and a power density of 2400W/kg. The battery pack is based on a heat-resistant separator based on ceramic technology, which prevents short circuits in internal circuits and greatly improves safety. In 2000, Hitachi Group became the world's first large-scale manufacturer of lithium-ion batteries for safe and high-performance automobiles. Since then, it has delivered a total of 900,000 lithium-ion batteries to the market for commercial hybrid vehicles.
On January 25, 2010, Mitsubishi Motors announced that it will switch the assembly of lithium-ion rechargeable battery packs in the electric vehicle "i-MiEV" to its Mizushima Works. The battery pack of the i-MiEV is currently produced at the Shiga Office of Lithium Energy Japan, a lithium-ion rechargeable battery production company jointly established by GS Yuasa Power Supply, Mitsubishi Corporation and Mitsubishi Motors. The production process is to purchase battery carriers, carrier covers, and battery cross members from component manufacturers for batteries produced by Lithium Energy Japan, and then make battery packs and supply them to Mizushima Works. The switch to in-house production this time refers to the transfer of the assembly process of the battery pack to Mizushima Manufacturing Co., Ltd. In the second half of 2010, the i-MiEV was officially sold in Japan, exported to Europe and supplied to the French PSA Peugeot Citroen Group. To this end, Mitsubishi Motors has ensured room for production increase by optimizing logistics and production management. Mitsubishi Motors has taken the policy of constructing an assembly line while making full use of existing equipment, thereby shifting the assembly process of battery packs in a short time and reducing equipment investment. Mizushima's new battery pack assembly line started production in June 2010.
GS Yuasa and others announced on February 21, 2010 that they will increase production of large lithium-ion batteries by 50% for the production of Mitsubishi Motors' i-MiEV electric vehicle. GS Yuasa Corporation, Ryo Motor Corporation and Mitsubishi Corporation are partners in Lithium Energy Japan's joint venture to manufacture and sell large lithium-ion batteries. Production of large lithium-ion batteries for 2,000 vehicles at the Shiga prefecture plant in fiscal 2009 and preliminary plans to produce large-scale lithium-ion batteries for 7,000 vehicles in fiscal 2010. In addition, GS Yuasa will produce large-scale lithium-ion batteries for i-MiEV electric vehicles at its Tokyo plant by the end of 2010, and plans to produce large-scale lithium-ion batteries for 2,000 vehicles in fiscal 2010. Together with the output from Lithium Energy Japan, the In fiscal 2010, large lithium-ion batteries can be produced for 9,000 vehicles. The i-MiEV electric vehicle went on sale in Japan in April 2010.
Nippon Chemical Sanyo, a medium-sized chemical producer, announced on March 1, 2010 that it has mass-produced cathode materials for automotive lithium-ion batteries. The company is developing materials that combine nickel, cobalt and manganese, and is also improving its lithium-nickel oxide material. Two samples have recently been introduced to the battery market for automotive battery applications, with mass availability after mid-FY2011. The company produces positive electrode materials for lithium-ion batteries at its Fukushima and Saitama factories, with a total production capacity of 1,000t/a, with almost all of its output being supplied to manufacturers of lithium-ion batteries for mobile phones.
Read more: Production trends of automotive lithium batteries in USA