
Main content:
- Lithium battery separator is one of the key lithium battery materials
- The lithium battery separator industry has a high industry barrier
- The separator wet process occupies the mainstream technical route
- The market concentration of separators will continue to increase
- Expansion of separator companies is accelerated
1. Lithium battery separator is one of the key lithium battery materials
Lithium-ion batteries are composed of four main parts: cathode material, anode material, separator, and electrolyte. The lithium battery separator is located between the positive and negative electrodes inside the battery, which ensures the passage of lithium ions and hinders the transmission of electrons. The performance of the lithium battery separator determines the interface structure and internal resistance of the battery, which directly affects the capacity, cycle and safety performance of the battery. The separator with excellent performance plays an important role in improving the overall performance of the battery.
In the cost composition of electric vehicles, the power system accounts for the largest proportion, close to 50%. The power system is mainly composed of batteries, motors and electronic controls, of which the battery is the core. In the cost structure of the battery system, the cost of the cathode in the battery is about 45%, and the cost of anode is about 10%. The lithium battery separator accounts for about 10% of the cost of the battery, the electrolyte accounts for about 10% of the cost of the battery, and the other components account for about 25%.
The cost of lithium battery separator includes raw material cost, energy cost, labor cost and depreciation and amortization. Among them, the cost of raw materials accounts for the largest proportion, mainly for the main materials and auxiliary materials required for the production of diaphragms. Including the main material PE, PP and auxiliary material paraffin oil, dichloromethane and so on. Energy costs mainly include water and electricity costs, accounting for 18%. The high cost of lithium battery diaphragm equipment leads to a high proportion of depreciation and amortization, reaching 23%.
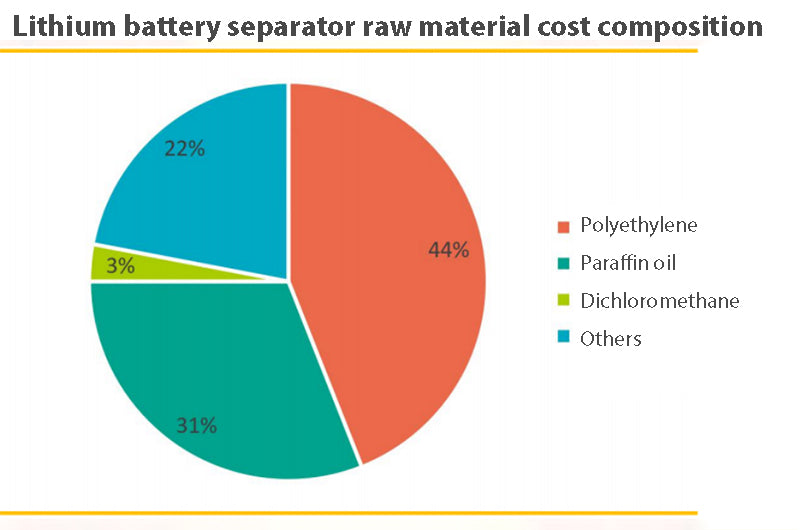
Lithium battery separator factories need to continue to reduce costs to maintain a competitive advantage, and leading separator companies can accumulate scale and cost advantages through capital barriers. The lithium battery separator is the best track among the four major materials. Due to high industry barriers, the concentration of the separator industry is higher than that of other lithium battery materials. In 2020, CR3 will reach 62%, and CR6 will reach 80%, which is higher than other lithium battery materials. In terms of profitability, the gross profit margin of the separator is also higher than that of the cathode, anode and electrolyte, which is at a high level.
2. The lithium battery separator industry has a high industry barrier
The lithium battery separator industry has a high degree of industry barriers, mainly reflected in technical barriers, capital barriers, equipment barriers and customer barriers, of which technology and equipment are the core barriers. Lithium battery separator is technology-intensive industries that require long-term technical accumulation. Lithium battery separator mainly involves many disciplines such as polymer material science, nanotechnology, surface and interface science, mechanical design and automation control technology, and complete set of equipment design.
China's mainstream lithium battery separator companies have long-term technical accumulation in technology research and development, production patent technology, raw material formulation technology and production line equipment construction. Mastering the biaxial stretching process and coating process, etc., they can ensure that the film's stability, consistency, safety and other characteristics meet the standards. Lithium battery separator is the link with the highest technical barriers in lithium battery raw materials, and has the highest requirements on equipment and production process. It belongs to the heavy asset industry.
The manufacturing equipment of dry-process separators for lithium batteries has achieved import substitution, while the core manufacturing equipment of wet-process separators mainly relies on imports. At present, the lithium battery separator equipment is jointly designed and customized by the separator manufacturer and the equipment manufacturer according to the production situation. There is no standard equipment available, which is a test of the production process and production line design capabilities of the separator companies. And the current separator companies have been bound with major lithium battery separator equipment manufacturers.
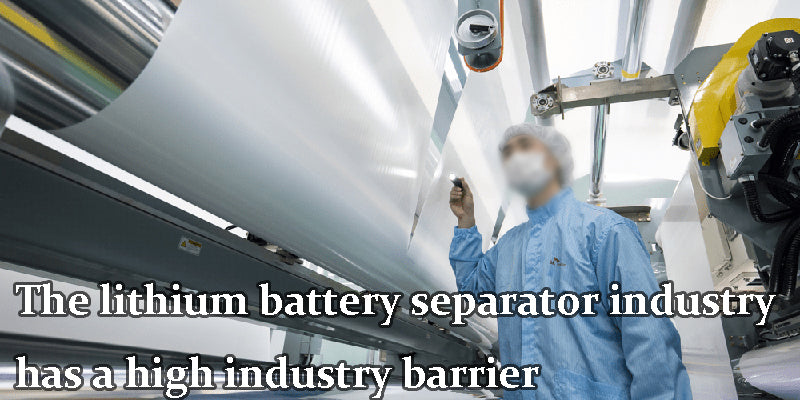
At present, there is a bottleneck in the supply of lithium battery separator production equipment, and upstream core equipment manufacturers have limited production capacity, which cannot match the increase in the demand for diaphragms due to the global development of new energy vehicles. Therefore, the expansion speed of the lithium battery separator production line largely depends on the supply of lithium battery separator equipment. Equipment manufacturers are cautious in expanding production, and the industry's supply and demand are tight, resulting in a production expansion cycle of about 2-3 years.
The lithium battery separator industry has high customer barriers and long certification time. Because power batteries and 3C products have high safety requirements, lithium battery companies in the world will be very cautious in selecting and replacing separator suppliers, and usually need to carry out strict product function, performance and other technical parameters and product overall quality control system certification work. Under normal circumstances, the overall certification period takes about 1-2 years, and it is not easy to change suppliers after certification, and the cooperative relationship is stable.
3. The separator wet process occupies the mainstream technical route
The production process of separator includes many processes such as raw material formulation and rapid formulation adjustment, micropore preparation technology, and independent design of complete sets of equipment. Among them, the micropore preparation technology is the core of the lithium battery separator preparation process. The manufacturing of the separator base film is mainly divided into two types: dry method and wet method according to the mechanism of micropore formation.
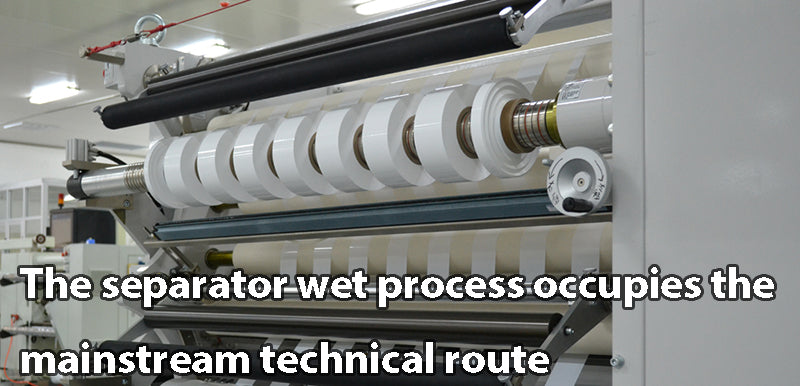
At present, ternary material power lithium batteries basically use wet-process separators, and mainstream manufacturers such as CATL and GOTION HI-TECH also use wet-process separators for lithium iron phosphate batteries that also need to continuously improve energy density. The wet-process separator can improve the energy density of lithium batteries, and the wet-process process can better control the pore size, distribution and porosity. Wet-process separators have higher porosity and air permeability, and can produce thinner and lighter separators, so they are generally used in the manufacture of high-end films.
However, the wet process has high cost, large investment, high equipment requirements, long construction and production cycle, and large energy consumption in the production process, and organic solvents are used. Wet process separators dominate the market. According to relevant statistics, the total output of separators in China in 2021 will be 7.904 billion square meters, of which the total output of wet-process separators will be 6.060 billion square meters, a year-on-year increase of 132%. The market share of wet-process separators continues to increase.
In 2021, the performance of the power market will continue to exceed expectations, and the new production capacity of wet-process separators will continue to be released. The downstream performance requirements of lithium battery separators are gradually improved, and the thickness of wet separators is thinner, which can improve the energy density of lithium batteries. At the same time, the downstream demand is strong, and the industry supply and demand is tight. The production capacity of wet separators is larger than that of dry separators, which promotes the shipment of wet separators.
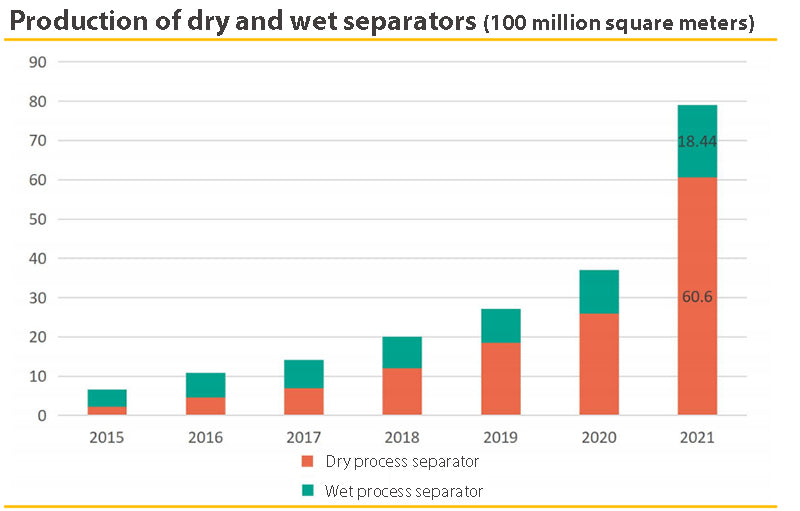
4. The market concentration of separators will continue to increase
The global separator production capacity continues to concentrate in China, and the Chinese market continues to move closer to the leading companies. The global separator competition pattern is dominated by four countries. China, South Korea, Japan and the United States have market shares of 43%, 28%, 21% and 6% respectively. China's share has increased significantly. The production capacity of China's mainstream separator companies has been greatly expanded, and at the same time, the pace of global supply has accelerated. The separator is expected to become the third lithium battery midstream material to achieve full export after the anode and electrolyte.
China's lithium battery separator market continues to focus on leading companies. In recent years, many separator production companies have gone bankrupt and eliminated, and many companies have been merged and acquired. Under the influence of high barrier barriers, difficulty in making profits, and the merger and integration of superimposed leading companies, the current industry pattern is gradually becoming clearer. Separator leading companies have advantages in technology, financing, production expansion, etc., and the global share is expected to continue to increase in the future.
In the context of the continuous improvement of the industry's prosperity, leading companies have increased the production of lithium battery separator. In terms of wet-process separators, the first echelon continued to increase production of wet-process separators, further consolidating the leading edge of the first echelon. In terms of dry process separators, Yunnan Energy New Material's production capacity planning of 2 billion square meters of dry process separators will reshape the future dry process market pattern. At the same time, companies with strong capital in other industries have cross-border layout of the lithium battery separator industry.
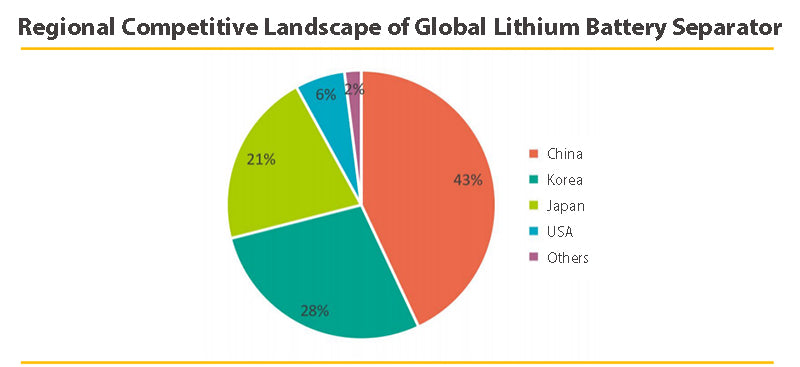
5. Expansion of separator companies is accelerated
● Driven by new energy vehicles and energy storage, the demand for separators has grown rapidly
The explosive growth of the global new energy vehicle and energy storage markets has driven the demand for upstream lithium battery separators. According to EVTank data, in 2021, the overall global shipments of lithium-ion batteries will be 562.4GWh, a significant increase of 91.0% year-on-year. In terms of structure, the global automotive power battery shipments were 371.0GWh, a year-on-year increase of 134.7%. The shipment of energy storage batteries was 66.3GWh, a year-on-year increase of 132.6%; the shipment of small batteries was 125.1GWh, a year-on-year increase of 16.1%.
China's lithium battery separator products are globally competitive. Driven by the substantial growth in global power battery shipments, China's separator exports have increased rapidly. Downstream segments such as the energy storage market have grown by over 100%, driving the growth of lithium battery separator shipments. Relevant data show that in 2021, China's lithium battery separator shipments will be 7.8 billion square meters, a year-on-year increase of more than 100%. From 2015 to 2021, the shipment volume of lithium battery separator will increase from 652 million square meters to 7.8 billion square meters, and the growth rate of shipments will remain above 30%.
● Power battery companies lock in the supply of separators, and the expansion of separator companies is accelerated
Under the background that the head lithium battery separator companies are almost full of production and sales, the leading power battery companies in the world lock the supply of separators in advance. In the world's mainstream lithium battery separator companies, the supply and demand are in a tight balance. According to the current expansion rhythm, superimposed separator equipment manufacturers restrict the release of production capacity. It is expected that the global separator will maintain a tight balance for at least 2-3 years.
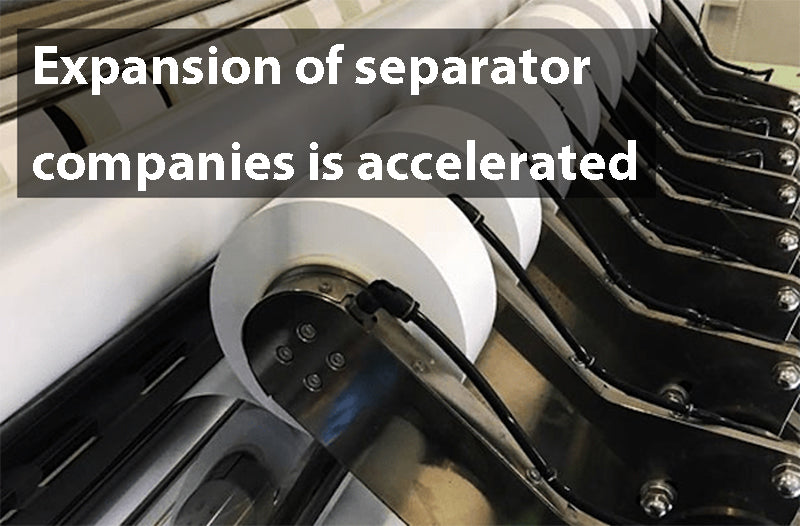
In the next 1-2 years, the expansion of separator production is mainly concentrated in leading companies, the supply of separators is limited, and the mismatch between supply and demand in the industry is expected to continue. In order to ensure the supply of raw materials, power battery companies have signed cooperation agreements with separator manufacturers to lock the supply of separators. In 2021, the new energy market is in strong demand, and leading companies are the first to announce production expansion.
Then, second and third tier and cross-border companies also participated in the expansion of separator production. With the continuous boom in the downstream market of new energy, the investment in the lithium battery industry continues to be hot, and the supply of lithium battery separators, one of the key materials for lithium batteries, continues to be tight. In order to seize market opportunities, related companies have accelerated the pace of production expansion.
Related articles: lithium ion battery anode material companies, lithium ion battery cathode materials