main content:
1. Land transportation
(1) Diesel locomotive
Even in gasoline or diesel internal combustion engine vehicles, electrical energy is an essential source of energy for the vehicle to function properly. Its most important role is the ignition and starting system of the car engine. In addition, there are some functions that cannot be achieved by mechanical energy, such as lighting and wiper driving.
Because electric systems are more flexible than mechanical or hydraulic systems, certain functions of the car, such as fan drive, power steering, and pump-assisted braking, have naturally shifted to electrification, which also makes the internal structure of the car more optimized and more efficient. Currently, all on-board air conditioning systems use electrical energy: including the control of fans and air valves. Ignition control and fuel injection control systems are electric and are developing towards electronically controlled (instead of camshaft) air valves (1~2kW), a turbo compressor with electronic assistance that improves combustion efficiency and reduces pollutant emissions. In this way, many functions normally performed by mechanical energy will be performed by electrical energy instead. The eventual trend in cars is towards "wires and drives", and the relationship to machinery will be reduced to a very limited extent. The annual growth rate of electricity consumption of newly listed cars is 120W.
In addition, some car assistance packages that facilitate driving and improve driving comfort are constantly appearing in cars, such as car radio, information control system with control and correction function (vehicle computer ECU), various sensors, car phone, GPS (Global Positioning System), and these all require electricity.
The electrical structure in the car is mainly determined by the large electrical load such as the starting system and headlights, and of course some low-power circuits and weak current signal circuits for control are also considered. Since various wired communication lines, multiplex lines, VAN bus (vehicle area network), CAN bus (controller area network) and power lines are often placed together, this will bring heat dissipation problems on the one hand, and EMC (electromagnetic compatibility) problems on the other hand. Disturbances and failures can have a fatal impact on critical functions such as ABS (Anti-lock Braking System), ESP (Electronic Stability Program), ASR (Acceleration and Anti-skid Control) or the speed control system and must be avoided.
①The source of car electricity
The electricity in the car comes from an alternator driven by an internal combustion engine, which is technically transitioning from a DC commutator generator to a claw-pole generator with a three-phase diode rectifier bridge, so that the generator can run to a higher speed range, and the required electric energy can still be obtained when the car is running at a low speed or decelerating. However, the efficiency of these generators is not very high, generally around 50%. The trend of increasing demand for electricity from vehicles year by year is driving the design and manufacture of generators towards higher power density and efficiency. Currently, the largest vehicle generators can reach 2.5kW with an efficiency of 85%.
②The voltage level of vehicle electricity
A long time ago, the electric power consumption of the car was very small, and it always used a 6V power supply network, which was powered by three lead-acid batteries in series. Soon, the power supply voltage level was increased to 12V, and large cars even required two separate battery packs to supply power. The increase in electrical power consumption has led to interest in the 42V power supply network, and the most immediate benefit for various drives in the car is that less copper is used. But there are still some problems to be solved before industrial application.
In order to adapt to the 42V power supply network, the design and performance of all automotive controllers must be modified and fully tested before new production lines can be established. Currently, although some argon headlamps require much higher voltages than 12V, we still cannot directly control the lighting circuit with 42V. So far there are no cars powered by the 42V voltage class. For hybrid vehicles, the situation is somewhat special, which requires a higher level of DC bus voltage, and some hybrid test vehicles use both 12V and 42V power supply networks.
Traditional cars use lead-acid batteries. In order to meet the peak power required for starting the car and the average power required to run all auxiliary functions, lead-acid batteries have made great progress in the corresponding technical characteristics. Since these auxiliary functions, especially those related to comfort, are generally not used at the same time, when designing energy, the configuration capacity of the battery will be appropriately reduced while taking into account the power generated by the vehicle.
The capacity of the battery is expressed in ampere-hour (A·h), and the battery manufacturer generally describes its capacity by the product of the battery's constant current discharge time and current, and the discharge current adopts the rated current. Advances in some key technologies can lead to improvements in energy density and power density of batteries, such as honeycomb anodes; gas synthesis (a separator made of glass microfibers is wetted by electrolyte, which is good for anode maintenance), battery casings with waterproof properties and explosion-proof valves [AGM batteries (glass fiber cotton battery)]; the use of silicone gel to fix the electrolyte.
The above technology can also greatly reduce the maintenance times of the battery, and significantly improve the reliability of the battery.
The volume limitation of the car and the demand for motorized operation determine the capacity of the installed battery to be 40~70A·h. Vehicles using diesel engines require batteries with higher power output capabilities due to their higher starting power.
(2) Buses and coaches
Buses and coaches generally use diesel internal combustion engines. For sightseeing buses, due to their relatively large size, in addition to the energy provided by the internal combustion engine, auxiliary equipment related to comfort also requires a lot of energy, such as air conditioners, lighting, and broadcasting equipment.
Nor can we ignore security systems that require electricity: pneumatic braking for passive security, which requires an electric motor-driven compressor and an eddy-current brake. Since the rotation of the wheel will cause a DC current to generate a magnetic field, the rotating part connected to the wheel will induce a current by cutting the magnetic field lines, causing loss and consuming the kinetic energy of the car.
The power supply voltage of buses and coaches is usually 24V, which is composed of two 12V batteries in series, and the energy storage capacity can be as high as 300A·h. There is often a non-24V power supply network in the car, which is used for equipment related to in-vehicle comfort, such as audio and video equipment or security systems.
(3) Heavy goods vehicles and utility vehicles
Commercial vehicles under 3.5t can use the power supply network of the same voltage level as the sightseeing bus. Only special purpose heavy goods vehicles need to be considered separately. For example, a refrigerated truck needs to use an on-board power supply, and it requires a large amount of energy storage. The electric power required by a small refrigerated truck is about 1.5kW, so the corresponding power supply should be at least twice (3kW). This means that, firstly, a larger capacity generator must be installed; secondly, the capacity of the battery must also be increased; other application cases can also be deduced from this, and we will refer to these issues in the later section on heavy goods vehicles.
For heavy-duty vehicles, the safety measures are roughly the same as those for passenger cars (such as pneumatic brakes and electromagnetic retarders). At the same time, driver comfort must also be considered, such as power steering, heating and air conditioning systems in the cabin when the car is running or stopped. Therefore, at least a 200A·h battery should be installed for heavy-duty vehicles.
Energy storage in refrigerated or long-distance trucks is particularly important in Europe and the United States. Due to the strict requirements on the driver's rest time, the truck needs to stay in the service area for a long time. Keeping the engine running during this period is not an economical approach, as this heat engine is only 9% to 11% efficient when the vehicle is stopped.
One solution would be to have electrical sockets in the service area to power the vehicle with the necessary equipment and also to install auxiliary generators on the auxiliary hubs. A small 7kW generator is sufficient, and it only needs to start generating electricity when it is stopped, which can fully meet the continuous cooling needs of the refrigerated truck.
Equipped with auxiliary power supply (APU) is the more common method, which has led to a lot of research work on fuel cell applications. The higher efficiency of fuel cells is being considered for use in high-end cars, which can reduce fuel consumption by 0.5 to 1L per 100 kilometers, especially when air conditioners are heavily used.
A high-temperature fuel cell (SOFC) may be the most suitable choice, with a typical operating temperature range of 750-850℃. The reformer converts the used hydrocarbons into carbon monoxide and hydrogen, which are used as fuel for the SOFC, which is combined with air for combustion. There have been many studies on this system so far. In addition to the fuel cell's own issues such as lifespan and thermal cycling, the reformer also faces a thorny problem: the fuel it needs must be sulfur-free, which current gasoline and diesel cannot meet. Therefore, the fuel cell solution is only economically feasible when the vehicle's main engine and auxiliary power supply can use the same fuel.
For special purpose vehicles, such as container trucks or vans with liftable tailgates, the required power varies from 1.5kW to 30kW. When these electric devices operate, their electricity is provided by an internal combustion engine and an alternator. Since the voltage of the battery pack is 24V, a 400V AC power supply network must be built in order to utilize the mature engine products on the market.
(4) Two-wheeled motor vehicles
Motorcycles or scooters require very little electricity, and despite the development of electric assist functions (such as assist starting systems or engine control devices), the battery capacity can still be small. The voltage of the battery pack installed on the two-wheeled vehicle has been increased from 6V to 12V.
2. Air transport
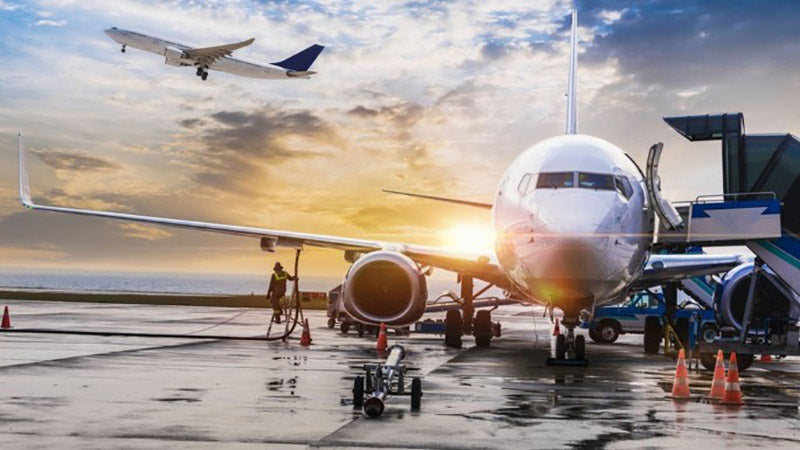
There is no doubt that the role of electrical energy in air transport is very important. The flight control of large aircraft usually uses mechanical and hydraulic drives, and electrical energy is used for various navigation instruments, various auxiliary equipment to improve passenger comfort, and engine starting.
In recent years, "fully electrified" aircraft have appeared, thanks to the installation of control units of a hybrid electro-hydraulic structure, which ensure the reliability and redundancy of the system. The power on the aircraft is gradually increased from 120kW of A320 to 500kW of A380. The power of the aircraft in the future planning is likely to reach more than 1MW, and the high-speed generator is driven by the turbine engine to provide electricity.
The power supply voltage of aircraft has been diversified from the original 115V AC 400Hz. The frequency is no longer the same standard, the bus voltage can be set to different levels such as AC115V, AC230V, DC270V and DC28V, and the various voltage levels are interconnected through DC-DC or DC-AC converters. Among them, DC28V can supply power for the control system, switchgear and control equipment of the aircraft. The onboard power supply must ensure the normal operation of necessary functions such as aircraft starting, control and navigation.
Distributed power sources such as fuel cells are currently under study, but the main problem is that no matter what energy storage method is used, it is unimaginable to let the aircraft take off with hydrocarbon fuel.
3. Rail transport
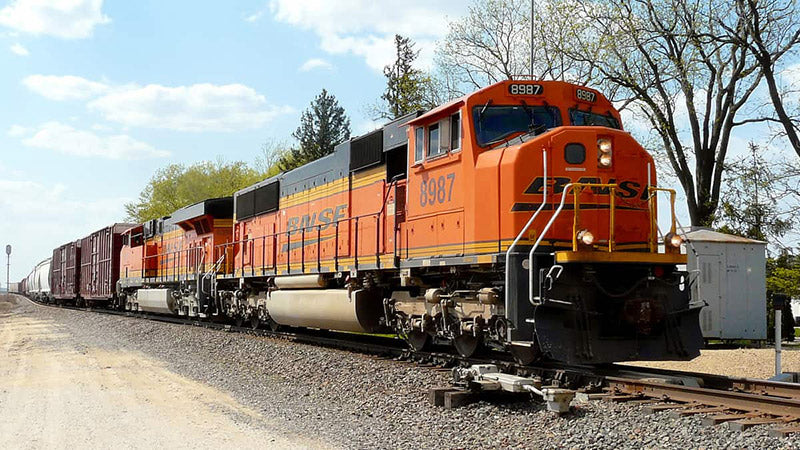
Rail transport can be divided into two categories: one type belongs to the pure electric energy supply system, which obtains electric energy from the high-power power supply network through the pantograph or trolley line system; the other belongs to the hybrid energy supply system, and the required electric energy is obtained through the diesel engine and the generator. Strictly speaking, only the latter belongs to the content discussed in this section, and its main energy source is diesel generators, and there is no special energy storage system except the 72V power supply network to supply the necessary instruments and equipment.
4. Shipping by sea
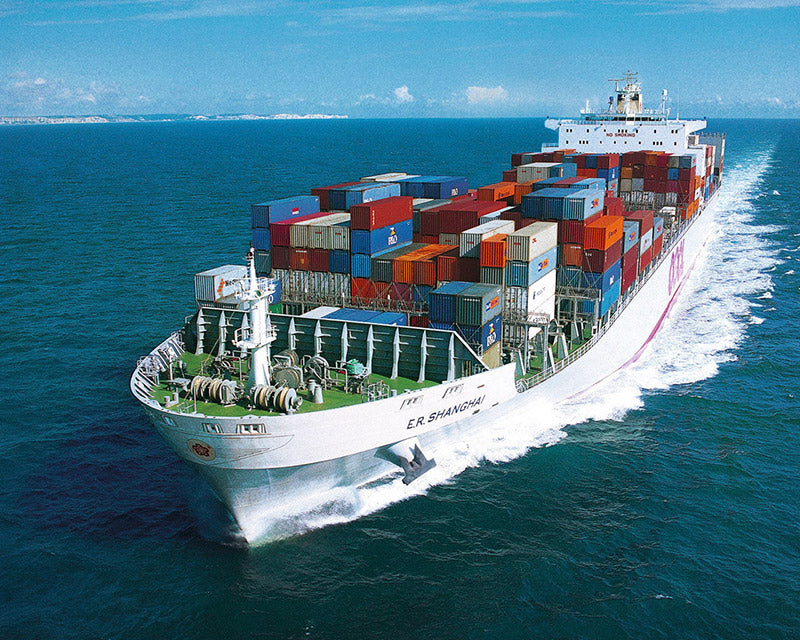
Cruisers, ferries and even freighters are often electrically driven to provide a smooth drive. This is especially true for ships equipped with podded (POD) thrusters, which directly drive the propellers through electric motors on adjustable brackets. Vessels have a high demand for energy and are powered by diesel generator sets to power the ship's electrical network. In addition, battery packs are specially configured to power the ship's safety equipment, instruments and signalling systems.
For small boats like yachts, the demand for electrical energy is also high. When it travels in the sea, electricity is provided by diesel generators, which is no problem. However, a bigger problem arises when the ship is docked at the dock, as the engine has to be kept running, creating noise and pollution. Therefore, an economical and environmentally friendly solution is being researched. For example, when using solid oxide high-temperature fuel cells to provide energy for stationary yachts, the thermal stress on the engine is greatly reduced due to the coordinated work of the generator and the fuel cell.