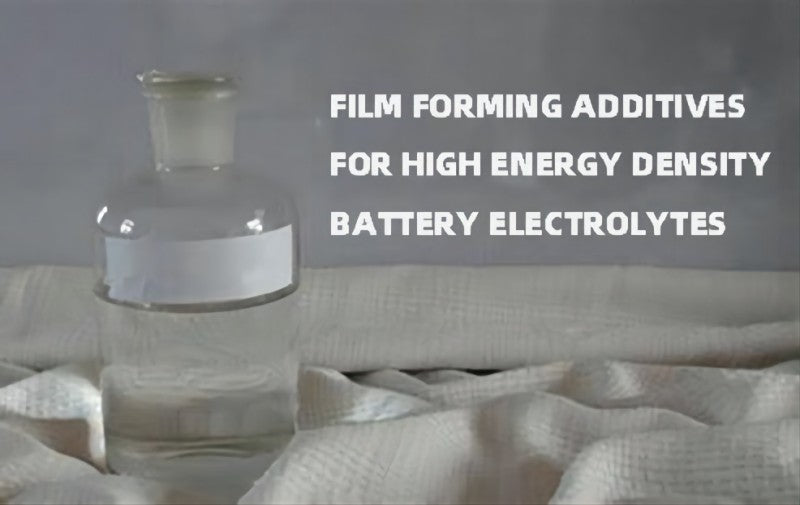
Main content:
- Main problems of high energy density electrode materials
- SEI film and the working mechanism of film forming additives
- Application of film forming additives
- Application of film forming additives in high energy density catholyte
- Application of film forming additives in high energy density anode electrolyte
- Summary
High energy-density electrode materials, such as nickel-cobalt-manganese ternary cathode materials, have problems such as decreased cycle performance and rate performance when they are matched with current conventional electrolyte systems.
The use of film-forming additives can promote the formation of a good solid electrolyte phase interface (SEI) film, solve the matching problem between high-energy-density electrodes and electrolytes, and improve the performance of lithium ion battery.
Main problems of high energy density electrode materials
The main problems of cathode materials
Since the capacity of the current lithium-ion battery anode material is higher than that of the cathode material, the energy density of the battery is mainly limited by the cathode. Improving the energy density of cathode materials is generally considered from two aspects of developing high-voltage and high-capacity cathode systems.
At present, the mainstream high voltage cathode materials is LiNixM2-xO4 doped with spinel transition metals, and the most typical material is LiNi0.5Mn1.5O4. Although the specific capacity of LiNi0.5Mn1.5O4 is only 146mAh/g, the specific energy can still reach 686Wh/Kg because the working voltage can reach 4.7V. At present, the conventional electrolyte system is LiPF6 dissolved in carbonate solvents such as EC, EMC, DMC, DEC or carbon PC.
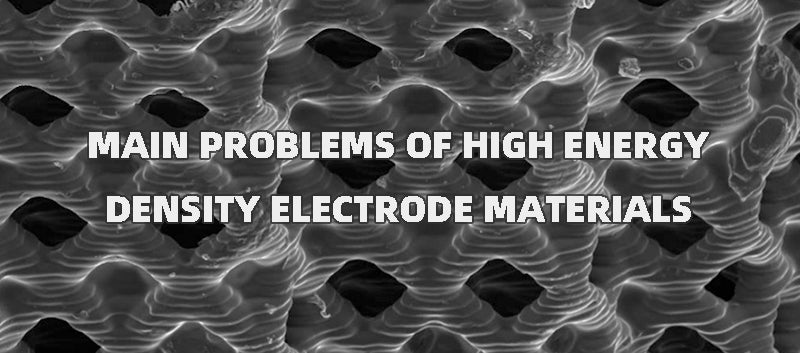
Deterioration of battery performance due to consumption of positive electrode active materials. The oxidative decomposition products of the electrolyte can easily dissolve the transition metal elements in the positive electrode material, causing the structure of the electrode material to be destroyed, resulting in capacity fading during the cycle of the battery.
One development direction of high-capacity cathode materials is to develop high-nickel ternary or multi-component systems, with Ni as the main active element, such as nickel-cobalt-manganese ternary materials.
The material capacity generally increases with the increase of the content of active metal components, but the increase of Ni content will make the surface stability of high-nickel materials deteriorate, causing the chemical reaction of electrolyte decomposition to produce HF to intensify, and HF will corrode high-nickel materials, so that the transition metal elements dissolve, leading to capacity fading, resulting in unsatisfactory cycle performance of high-nickel ternary or multi-element materials.
In addition, lithium-rich cathode materials with high specific capacity are also research hotspots. This type of material has the advantages of high theoretical capacity, high working voltage, and low cost, but there is a problem of oxygen evolution on the surface of the material after Li+ is released from the crystal lattice during the first charging process, and the released Li+ cannot be fully embedded back during the discharge process. This results in a large irreversible capacity loss for the first charge and discharge, and the cycle performance is not ideal.
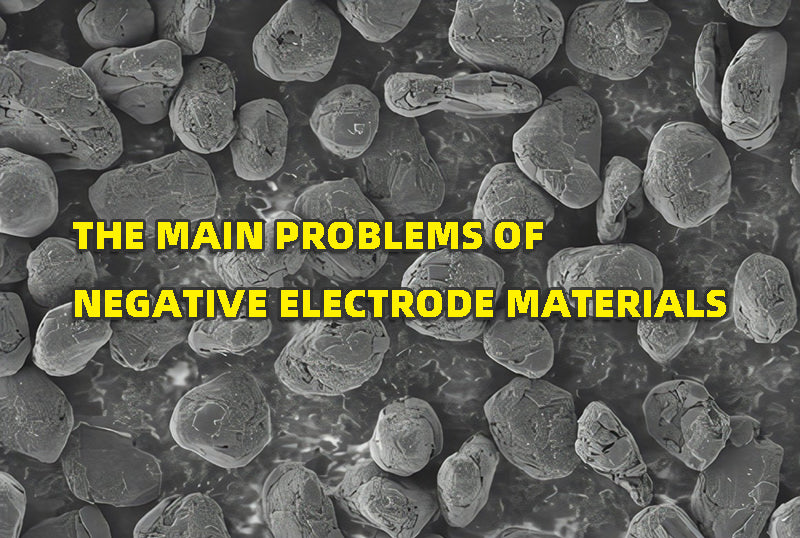
The main problems of negative electrode materials
Although the energy density of lithium-ion batteries is mainly limited by the cathode material, there is also a lot of room for performance improvement in the anode material. High energy-density anode materials need to have a large lithium storage capacity and a low lithium intercalation and extraction potential.
For the currently commonly used graphite anodes, the energy density and power density are both low, and it is easy to lead to a security issue. Silicon anode can undergo electrochemical alloying/dealloying reaction with lithium at room temperature, so it has high lithium storage capacity and low voltage platform, and has the advantages of sufficient source and cheap price.
In this way, there are lots of silicon based anode materials suppliers in China and they have much experience in this area. They can provide high cost effectively products for every customers.
The volume effect of silicon-based anode materials makes it easy to pulverize, break, and even fall off from the current collector during the process of intercalation and delithiation, which limits the cycle performance of silicon-based negative electrodes. Alleviating or inhibiting the volume expansion of silicon-based materials and improving cycle stability are the focus of developing silicon-based anode systems.

SEI film and the working mechanism of film forming additives
During the first charging and discharging process of the liquid lithium-ion battery, the electrode material and the electrolyte react at the solid-liquid phase interface to form a passivation layer covering the electrode surface, that is, the SEI film. The charging and discharging of the battery is completed through the intercalation and detachment process of Li+ in the electrode. The intercalation and detachment of Li+ must pass through the SEI film covering the electrode.
Therefore, the characteristics of the SEI film determine the dynamics of lithium intercalation and detachment and the stability of the electrode/electrolyte interface. , which determines the performance of the entire battery. The introduction of film-forming additives on the basis of selecting a suitable electrolyte to promote the formation of high-quality SEI films is a hotspot of related research.
In general, the working mechanism of film-forming additives can be divided into film-forming mechanism and film-decorating mechanism. For positive electrode film-forming additives, the film-forming mechanism means that the oxidation potential of the additive is lower than that of the electrolyte solvent, and it can be decomposed on the surface of the positive electrode before the electrolyte solvent, and the decomposition products participate in the formation of the SEI film.
The surface film is rich in polymers, which reduces the oxidation rate of the electrolyte. The film decoration mechanism is that the additive itself does not participate in film formation, but has the functions of removing water, reducing acid or complexing, etc. The products of the action can improve or cover the active points on the electrode surface, inhibit A side reaction occurs between the electrode and the electrolyte, thereby ensuring the stable formation of a good SEI film on the electrode surface.
For negative electrode film-forming additives, the film-forming mechanism means that the additive has a high reduction potential, and its affinity with electrons is greater than that of electrolyte solvent molecules. The surface forms an SEI film, thereby preventing the subsequent electrolyte reduction reaction from damaging the electrode. There are many types and quantities of such film-forming additives, and representative substances include SO2, VC and ES.
Since VC has a C=C bond, the reduction potential is high, and it can be reduced and decomposed on the surface of the negative electrode before the electrolyte to form a polymer film to protect the negative electrode material. The film decoration mechanism is that the additive does not undergo reduction and decomposition in the electrolyte, but has a strong property of chelating with Li+, which can preferentially solvate Li+ in the electrolyte and prevent Li+ from solvating with solvent molecules in the electrolyte.
Thereby inhibiting the intercalation of solvent molecules and Li+ into the negative electrode layer, improving the lithium insertion and extraction capacity of the electrode, and prolonging the cycle life.

Application of film forming additives
High safety and high cycle stability are the basic requirements of high energy density electrodes for the electrolyte, and film-forming additives are introduced into the electrolyte to form a stable protective film on the positive and negative electrodes of the battery and stabilize the electrode/electrolyte interface. It has become a key development trend to realize high energy density electrode electrolyte.Application of film forming additives in high energy density catholyte
For LiNi0.5Mn1.5O4 high-voltage cathode materials, tris(2,2,2-trifluoroethyl)phosphite (TFEP), trimethylphosphite (TMP) and tris(pentafluorophenyl)phosphine ( TPFPP) and other phosphorus-containing film-forming additives can inhibit the decomposition of conventional electrolytes and the dissolution of transition metals in positive electrode materials by preferentially oxidizing the surface of the positive electrode over the solvent and forming an SEI film, thereby improving various performances of the battery.Application of film forming additives in high energy density anode electrolyte
Fluoroethylene carbonate (FEC) has been extensively studied as a film-forming additive and can also be used in silicon-based anode electrolytes. Based on a high-concentration lithium salt electrolyte system with lithium bisfluorosulfonyl imide (LiFSI) as the lithium salt and PC as the solvent (the molar ratio of the substances is 1:3), the scientists studied LiODFB and tris(trimethylsilane) The influence of borate ester (TMSB) on the cycle performance of lithium-ion battery with silicon negative electrode.
After 1C constant current charge and discharge (0.01 -1.20V) test, it was found that both LiODFB and TMSB can improve the cycle performance of silicon negative electrode battery by participating in film formation. With the addition of 3% LiODFB and TMSB groups, the capacity retention rate after 300 cycles was increased by 17% and 38%, respectively, compared with the base group.

Some scientists used 1.0mol/L LiPF6/EMC+DMC+EC (volume ratio 1:2:1) as the basic electrolyte to study the effect of TTFEB as an electrolyte additive on the cycle stability of silicon negative lithium-ion batteries. Electrochemical performance tests found that TTFEB can be reduced and decomposed on the surface of the silicon negative electrode prior to the electrolyte components at 1.8V, and form a protective film on the surface of the silicon particle in situ, improve the stability of the SEI film, and inhibit the structural change of the silicon electrode.
Thereby improving the cycle performance and coulombic efficiency of the silicon negative electrode lithium-ion battery. Using 1.0mol/L LiPF6/EC+DEC (mass ratio 1:2) as the blank electrolyte, the influence of the additive SA on the lithium-ion battery with LiNi0.5Mn1.5O4 as the positive electrode and Li as the negative electrode was investigated, and the electrochemical impedance spectroscopy test.
It shows that the interfacial film resistance and charge transfer resistance of the sample added with 3% SA decrease continuously during the cycling process, which is conducive to the intercalation and desorption of Li+, and the capacity retention rate of the battery is 200 times at 1C and 2C at 3.0-4.9V. Stay at 90% and 92%.
Summary
With the development of the field of long-range power batteries, there is an urgent need to further increase the energy density of lithium-ion batteries. High-voltage, high-capacity cathode materials have become the main way to greatly increase the specific energy of power lithium-ion batteries. It has also become an industry consensus that silicon-based anode materials can fully replace other anode materials.
Considering factors such as cost and existing battery preparation technology, liquid electrolytes composed of carbonate organic solvents and LiPF6 will still be the first choice for power batteries in the near future. Therefore, the main direction for the development of electrolytes for battery high energy density is to develop high Performance film-forming additives to match the high-voltage positive electrode and solve the capacity fading of high-nickel multi-component materials.
At the same time, it takes into account the high-capacity silicon-based negative electrode to avoid the repeated rupture of the SEI film caused by the volume expansion of the silicon negative electrode during the cycle and excess electrolyte caused by regeneration. consumption etc.
Related article: top 10 lithium battery electrolyte companies, lithium ion battery electrolyte, battery-grade lithium carbonate companies