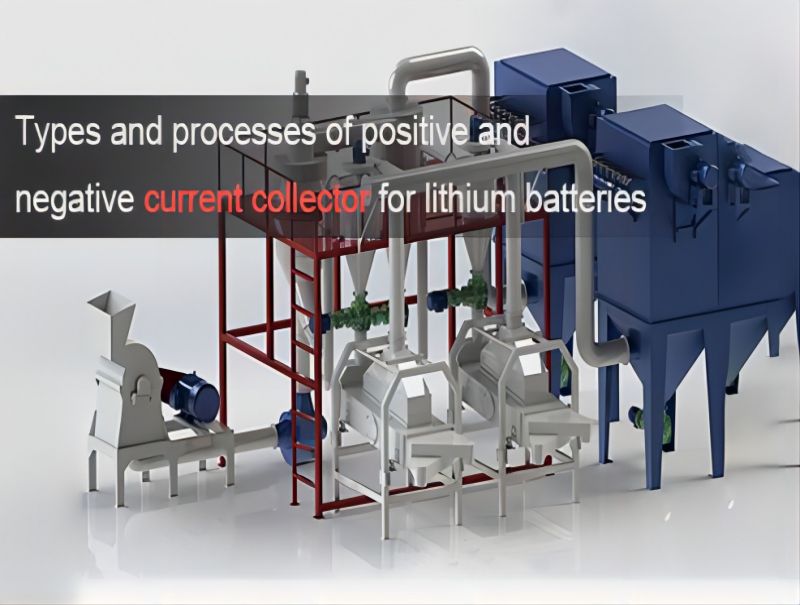
Main content:
- Basic information of current collector
- Thickness requirements of copper and aluminum foil for lithium batteries
- Surface roughness requirements of copper and aluminum foil for lithium batteries
- Why use copper foil for the negative electrode and aluminum foil for positive electrode
- Current collector type and preparation process
- Copper foil type
- Copper foil preparation process
- Types of aluminum foil
- The preparation process of aluminum foil
- Main suppliers of aluminum foil
- Some special current collector
Types and processes of positive and negative current collector for lithium batteries It is well known that the four main parts of lithium-ion batteries are positive electrode material, negative electrode material, separator and electrolyte. However, in addition to the main four parts, the current collector used to store the positive and negative electrode materials is also an important part of the lithium battery. Today we will talk about current collector materials for positive and negative electrodes of lithium batteries.
Basic information of current collector
For lithium-ion batteries, the commonly used positive current collector is aluminum foil, and the negative current collector is copper foil. In order to ensure the stability of the current collector inside the battery, the purity of both is required to be above 98%. With the continuous development of lithium battery technology, whether it is lithium batteries used in digital products or batteries for electric vehicles, we all hope that the energy density of batteries will be as high as possible, and the weight of batteries will become lighter and lighter. Reducing the thickness and weight of the current collector intuitively reduces the volume and weight of the battery.Thickness requirements of copper and aluminum foil for lithium batteries
With the rapid development of lithium batteries in recent years, the current collector for lithium batteries have also developed rapidly. The positive electrode aluminum foil has been reduced from 16um in previous years to 14um, and then to 12um. Now many battery manufacturers have mass-produced and used 10um aluminum foil, and even used 8um. As for the copper foil used for the negative electrode, due to its good flexibility, its thickness has been reduced from 12um to 10um, and then to 8um.
Up to now, most battery manufacturers use 6um for mass production, and some manufacturers are developing 5um/4um. are all possible to use. Since lithium batteries have high requirements on the purity of the copper and aluminum foil used, the density of the material is basically at the same level. As the thickness of the development decreases, the surface density also decreases accordingly, and the weight of the battery is naturally getting smaller and smaller, which is in line with our requirements for lithium batteries.
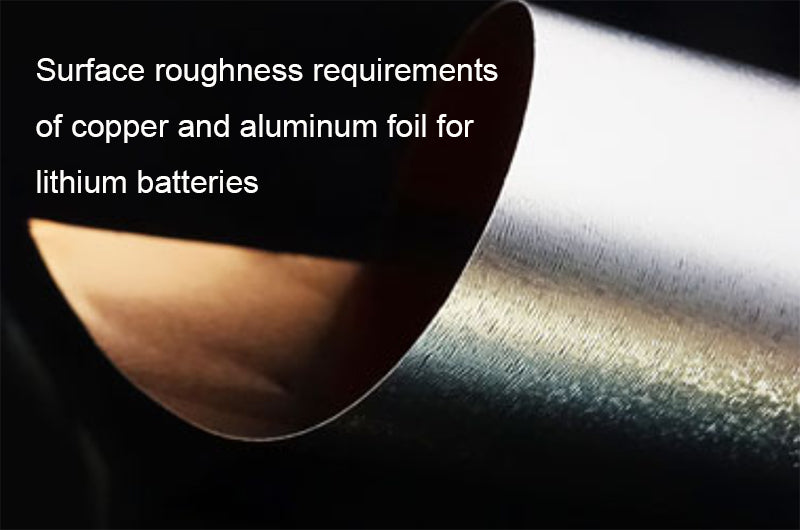
Surface roughness requirements of copper and aluminum foil for lithium batteries
For the current collector, in addition to the thickness and weight of the lithium battery, the surface properties of the current collector also have a greater impact on the production and performance of the battery. Especially for the negative electrode collector, due to the defects of the preparation technology, the copper foils on the market are mainly single-sided, double-sided, and double-sided roughened. This asymmetry of the two-sided structure leads to asymmetric contact resistance of the coating on both sides of the negative electrode, which in turn prevents the capacity of the negative electrode on both sides from being released evenly.
At the same time, the asymmetry on both sides also leads to inconsistent bonding strength of the negative electrode coating, which shortens the charge-discharge cycle life of the negative electrode coating on both sides. Severe imbalance will accelerate the decay of battery capacity. In the same way, the positive electrode aluminum foil is also developed to a double-sided symmetrical structure as much as possible.
However, due to the influence of the aluminum foil preparation process, the single-sided smooth aluminum foil is mainly used. Since aluminum foil is basically rolled from thicker aluminum ingots, the contact between the aluminum ingot and the roll needs to be controlled during the rolling process. Therefore, lubricants are generally added to the surface of the aluminum foil to protect the aluminum ingot and the roll. The lubricant on the surface has a certain impact on the battery pole piece. Therefore, for aluminum foil, the surface lubricant is also a key factor.
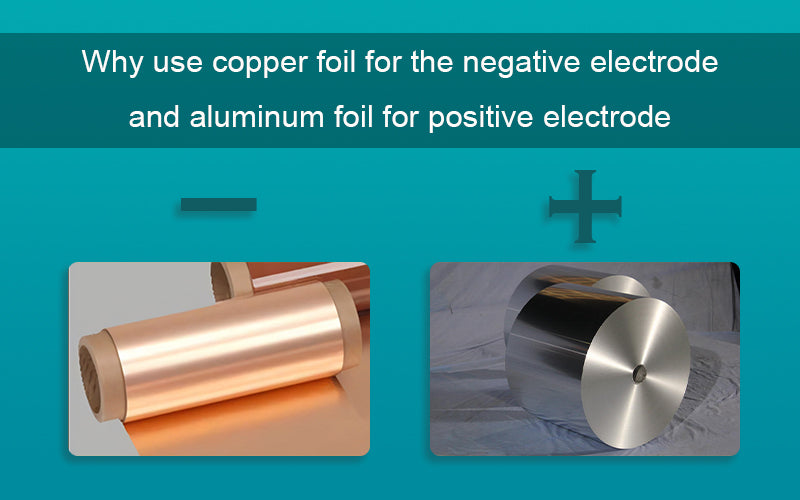
Why use copper foil for the negative electrode and aluminum foil for positive electrode
First, copper and aluminum foil has good conductivity, soft texture and cheap price. We all know that the working principle of a lithium battery is an electrochemical device that converts chemical energy into electrical energy. In this process, we need a medium to transmit the electrical energy converted from chemical energy, and here we need conductive materials. Among ordinary materials, metal materials are the most conductive materials, and copper foil and aluminum foil are the cheapest and best conductive materials among metal materials.
At the same time, in lithium batteries, we mainly have two processing methods: winding and lamination. Compared with winding, the pole piece used to prepare the battery needs to have a certain degree of flexibility, so as to ensure that the pole piece will not be brittle and broken when winding. Among the metal materials, copper and aluminum foil are also softer metals. The last thing is to consider the cost of battery preparation. Relatively speaking, the price of copper and aluminum foil is relatively cheap, and the resources of copper and aluminum elements are abundant in the world.
Second, copper and aluminum foil is relatively stable in the air. Aluminum is easy to chemically react with oxygen in the air, forming a dense oxide film on the surface of aluminum to prevent further reaction of aluminum, and this thin oxide film also has a certain protective effect on aluminum in the electrolyte. Copper itself is relatively stable in the air and basically does not react in dry air.
The third is that the potential of the positive and negative electrodes of the lithium battery determines the use of aluminum foil for the positive electrode and copper foil for the negative electrode, not the other way around. The positive electrode potential is high, copper foil is easily oxidized at high potential, and the oxidation potential of aluminum is high, and the surface layer of aluminum foil has a dense oxide film, which also has a good protective effect on the internal aluminum.

Current collector type and preparation process
Copper foil type
According to the preparation method of copper foil, there are mainly two kinds of rolled copper foil and electrolytic copper foil. In the early days of battery invention, due to the limitation of copper foil preparation process equipment technology, etc., mainly used rolled copper foil with high cost. Rolled copper foil is the original foil made by repeated rolling of copper plate ( also called wool foil), roughened according to requirements. Electrode posited copper is to dissolve copper to make a solution, and then deposit copper sulfate electrolyte under the action of direct current in a special electrolytic equipment to make the original foil, and then make the original foil according to the requirements.
Carry out a series of surface treatments such as surface treatment, heat-resistant layer treatment and anti-oxidation treatment. Electrodeposited copper foil is different from calendered copper foil. The two sides of electrolytic copper foil have different crystal forms. The side close to the cathode roller is relatively smooth, which is called the smooth side.
Copper foil preparation process
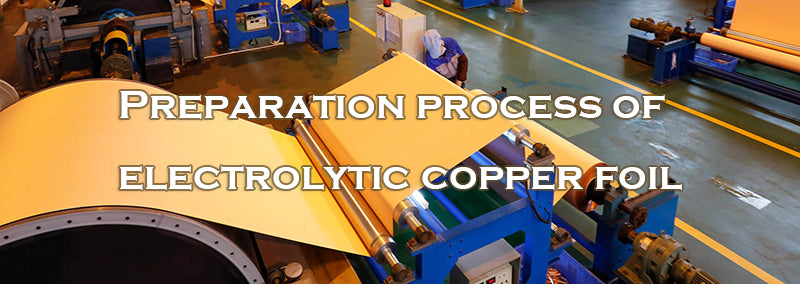
- Preparation process of rolled copper foil
Rolled copper foil is made by repeatedly rolling copper sheets, annealing at a certain temperature, and repeated pickling and rolling. Copper foil rolling process parameters are strictly controlled, and the requirements for equipment and process control are very high. At present, it is mainly produced in Japan, and a small amount is used for lithium batteries.
- Preparation process of electrolytic copper foil
Electrolytic copper foil is made by dissolving copper to make a solution, and the copper sulfate electrolyte is deposited under the action of direct current in a special dissolution container to make the original foil, and then the original foil is subjected to surface treatment and heat-resistant layer treatment according to requirements. And a series of surface treatment such as anti-oxidation treatment. Compared with rolled copper foil, the preparation of electrolytic copper foil is relatively simple, the equipment requirements are relatively simple, and the cost is relatively low.
Most lithium battery copper foil uses electrolytic copper foils as negative electrode base materials. During the preparation process of electrolytic copper foil, since the copper foil is produced on the titanium roller by the copper-containing electrolyte during electrolysis, the surface of the copper foil close to the titanium roller is smooth, called the smooth surface; the other side is convex and concave. The uneven crystal structure surface is relatively rough and is called the rough surface.
In the preparation process of electrolytic copper foil, factors such as electrolyte temperature, electrolyte concentration, additive content, and electrolyte flow rate during foil production need to be controlled. For electrolytic copper foil for lithium batteries, the factors controlled in the early foil making process will affect the purity, thickness/weight uniformity, strength and elongation of the copper foil itself. The thickness of the electrolytic copper foil after electrolysis is generally the thickness required by the manufacturer.
In the later stage, the surface of the copper foil needs to be cleaned to remove the residual electrolyte on the surface, and the surface is treated with anti-oxidation and drying. In this process, the degree of surface treatment directly affects the surface finish of the copper foil and the tension of the copper foil surface. After surface treatment, it needs to meet the coating requirements of copper foil for lithium batteries.
Too smooth coating effect is poor, and too rough will affect the uniformity of battery performance. The preparation process plays an important role. After the surface treatment of the copper foil is completed, it needs to be cut into the width and length required by the lithium battery manufacturer. For manufacturers who use a large number of copper foil substrates, it is hoped that the width of the copper foil is appropriate, and the length of the copper foil is within the handling range. The longer the better, this can improve mass production efficiency and reduce production costs. However, due to the influence of foil-making equipment and slitting equipment, the length of copper foil is generally within 2500m.
Types of aluminum foil
Aluminum foil is mainly prepared by rolling, and its classification method is mainly based on the type and content of impurities. Aluminum foil for lithium batteries mainly includes 1 series, 3 series and 8 series aluminum foil, which are industrial pure aluminum, aluminum manganese series and aluminum and Other uncommon elements.
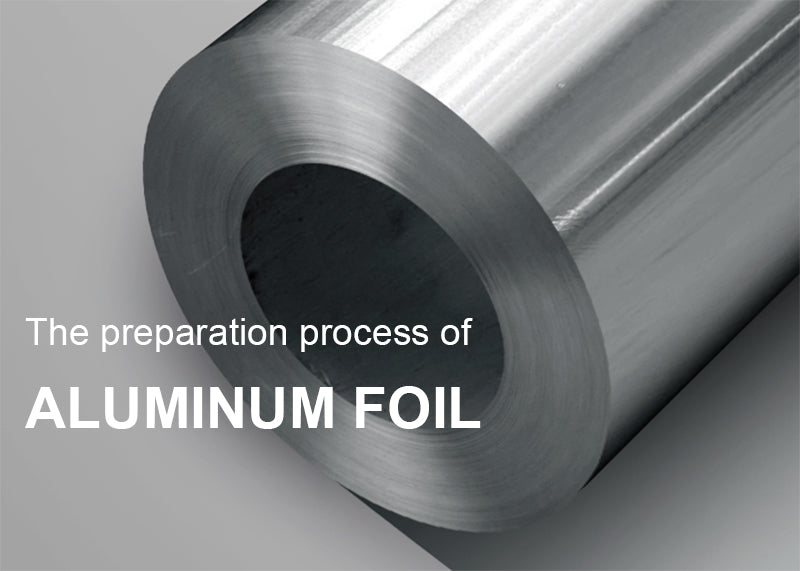
The preparation process of aluminum foil
The production of aluminum foil is mainly by rolling the aluminum foil blank to the required thickness through multiple rolling and multiple heat treatments. In this process, there are mainly two processes: rough rolling and finishing rolling. After finishing rolling, the surface of the aluminum foil will be treated, and finally the aluminum foil will be cut into the width and length required by the lithium battery manufacturer. In this process, the aluminum foil needs to be well controlled.
Generally, manufacturers of aluminum foil for lithium batteries use aluminum ingots provided by upstream suppliers for rolling, so the composition of aluminum ingots is basically determined, and the demand for strength and elongation of aluminum foil in the later stage is realized by controlling the rolling pressure and heat treatment process. Major suppliers of copper foil with the continuous development of electronic products, the world's dependence on lithium batteries is becoming stronger and stronger, and the demand for lithium-ion battery materials is also increasing, which brings more material suppliers.
Suppliers of negative electrode current collector copper foil are also gradually shifting from abroad to domestic. For the world, copper foil suppliers are mainly distributed in Asia, mainly Japan's Mitsui Metals, Nippon Energy, Furukawa Electric, Fukuda Metal, and Nikko Materials, as well as South Korea's largest factory, Nissin Corporation, and Taiwan's Changchun. Copper foil and Nan Ya plastic. The world's largest copper foil factory is Mitsui Metals, which is distributed in Japan, Taiwan, the United States, France and Malaysia.
Chinese suppliers mainly include Shanghai Jinbao, Guangdong Meixian Meiyan Electrolytic Copper Foil, Lingbao Huaxin Copper Foil, Zhongke Yinghua High-tech, Huizhou United Copper Foil and some other smaller manufacturers, mainly producing electrolytic copper foil. The output of China's copper foil products is relatively low, which generally cannot fully meet the needs of lithium battery manufacturers, and some products need to be imported from other countries. At the same time, China also lacks medium and high-end copper foils, such as high-strength, high-toughness, and ultra-thin copper foils.
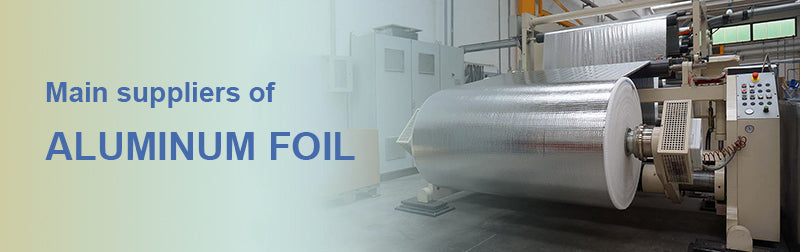
Main suppliers of aluminum foil
There are relatively few aluminum foil suppliers. In China, there are mainly suppliers such as Fulaishun, Hangzhou Five Star, Huaxi Aluminum, Nannan Aluminum, Sifangda, Zhongnan Aluminum, Shanghai Alcoa, and Shenzhen Zhenxin Foil Electronic Packaging Materials. There are other countries including Japan, mainly Japan's Toyo Aluminum and Hitachi Metals.Some special current collector
Special current collector are mainly for lithium batteries with special performance requirements, or current collector that have not been developed for higher performance materials. Some time ago, relevant experts proposed "no negative electrode battery", which actually imagined that the negative electrode copper foil was replaced by metal lithium, and the lithium layer was very thin; at the same time, some experts proposed to replace the higher-priced copper with cheap iron.
However, this information was quickly questioned after it was released: From the perspective of lithium layer and iron foil materials themselves, the performance cannot meet the high performance required by lithium batteries. From the perspective of manufacturing processes and equipment, it is difficult to meet the production requirements. The cost issue is also basically difficult to solve. There are also R&D teams that do not use other materials to replace the copper foil of the negative electrode substrate, but start from the copper foil itself and process it accordingly to improve performance and optimize the performance of lithium batteries.
The most intuitive way is to cooperate with copper foil suppliers to develop high-strength and high-elongation copper foil, and develop thinner copper foil to improve battery energy density; in addition, copper mesh is used to increase battery energy density. For aluminum foil, it is mainly to carry out surface treatment on the existing aluminum foil, such as roughening treatment, cleaning treatment, or coating conductive carbon on the surface of aluminum foil.
Recently, more research has been done on carbon-coated aluminum foil, in which a thin layer of conductive carbon is coated on the surface of normal aluminum foil to optimize battery performance.
Related article: composite copper foil companies, Top 10 battery aluminum plastic film brands, aluminum ion battery