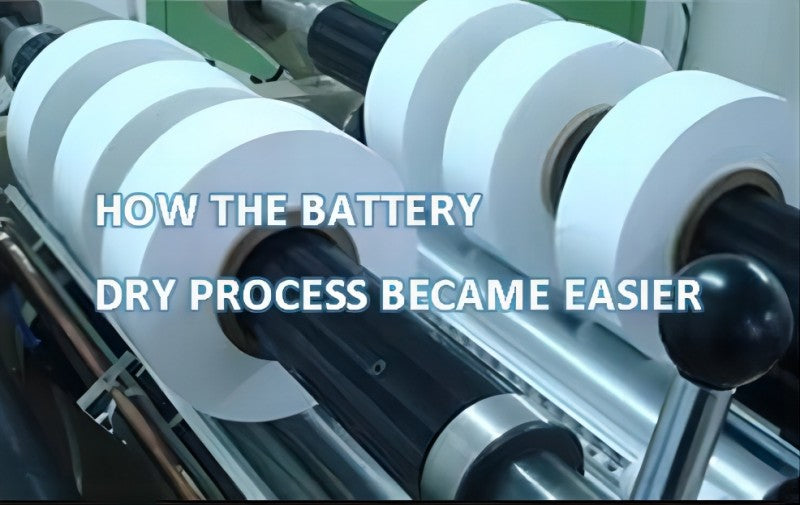
Main content:
When technology makes it possible to reconstruct manufacturing logic, equipment becomes the source of industrial vitality. In the front end of lithium battery manufacturing, changes happened quietly. Some companies are looking for a way to simplify the preparation of electrodes, and have begun to try to prepare pole pieces by dry method.
In 2019, Tesla bought Maxwell with a market value of 235 million US dollars at a premium of over 55%. The company's core technology is dry electrode technology. The following year, Tesla launched the 4680 cylindrical battery, saying that it would apply dry electrode technology to the new cylindrical battery system.
In the process of applying the dry electrode technology to the positive and negative electrode materials, it can not only save the solvent, but also enhance the performance advantages of the electrode sheet, and because the process is simplified, the investment in equipment is less.
In contrast, there is still a gap between the dry method and the wet method in terms of industrialization. Earlier this year, Tesla produced its millionth 4680 battery. The industrialization of 4680 cylindrical batteries is sweeping, and it is imminent to overcome the technical difficulties of dry electrodes.
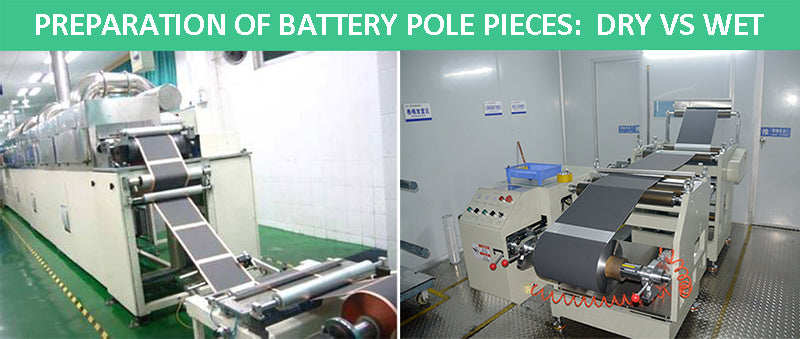
Preparation of battery pole pieces - dry VS wet
In the front stage of lithium battery manufacturing, the process of wet electrode preparation is very mature, mixing materials, coating, drying, NMP recovery, rolling, and the electrode sheet is from dry to wet and then to dry. The wet process is relatively simple. With the support of the "wet" state, the slurry has good fluidity and less air bubbles.
The simple operation greatly improves the efficiency of pole piece preparation and lays a solid foundation for the power battery to move towards the TWh era. Compared with the wet method, the innovation of the dry method has four major advantages:
- Simplify the production process
The core of the dry method of preparing pole pieces lies in the discarding of wetness. The dry method does not use binders and solvents, which simplifies the pulping, coating drying and solvent recovery processes in the wet method.
- Improve energy density
Electrodes prepared by dry method can have higher compaction density and accommodate more active materials. Moreover, in the process of gradually discarding the solvent, the fusion of the negative electrode material is better, which facilitates lithium supplementation of the negative electrode and reduces the loss of the first cycle capacity. At present, the energy density of dry electrodes exceeds 300Wh/kg, and can reach 500Wh/kg in the long run.
- Adapt to the battery system
The power battery material system is gradually developing towards high nickel doped silicon. Dry electrode technology can not only weaken the influence of humidity on the performance of high-nickel positive electrodes, but also have a stronger ability to withstand the expansion of silicon-based negative electrodes.
- Extend the service life
Because no binder is used, the service life of the battery is significantly improved.
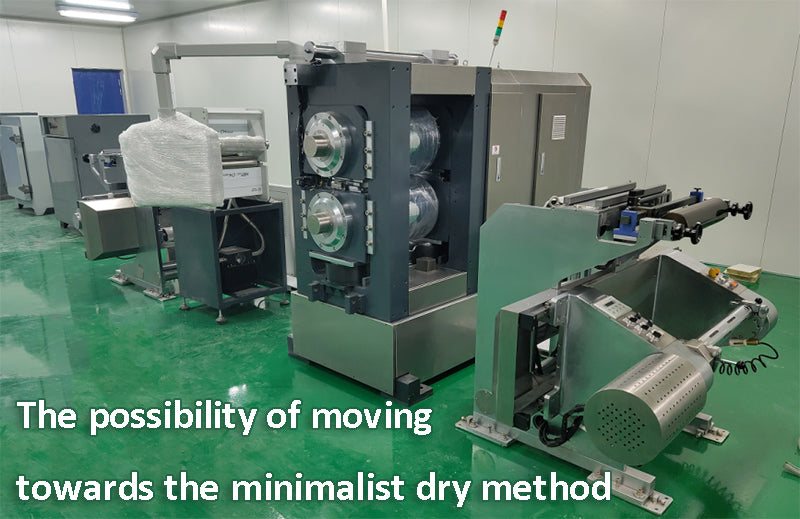
The possibility of moving towards the minimalist dry method
Comparing the two methods, the process of wet preparation of pole pieces is mature at this stage. The dry mass production is a possibility to become minimalist. The vision of dry electrode preparation is beautiful: smaller plant and equipment area, less energy consumption, and lower battery cost, but it is not easy to implement the discarding of wetness in commercial use.
In 1991, Sony explored the wet method for commercial use, and now the wet method has become the mainstream of electrode preparation, precisely to avoid the problems of poor feasibility, low efficiency, and poor consistency in dry method preparation. However, it should be seen that changes are taking place with regard to dry electrode preparation. The industrialization of 4680 cylinders in the industry is advancing rapidly. At this juncture, both scale expansion and process upgrading are required.
Control the thickness of dry film formation
For the difficulty of dry film forming thickness and uniform control, the solution is double steel belt system forming and multi-stage rolling.Double steel belt system
The double-steel belt rolling technology realizes the manufacture of dry-process electrode self-supporting film. The steel belt system can be used as the carrier of the self-supporting electrode film to reduce the phenomenon of electrode film breaking during roll-to-roll manufacturing and high-speed movement.Multi stage rolling
The powder is rolled into a thick film by rolling technology, and then wound up or compounded with the current collector after repeated hot pressing to ensure that the film is thinned to the specified thickness and the compaction density is increased without continuous belting.
The future of dry electrode technology can be expected. With the development of dry electrode technology, the energy density of the electrode can be increased to 500Wh/kg, and the energy density of the battery will be increased by 25% in a period of about 2 years, while the cost will continue to decline with 10%, breaking through the bottleneck of the energy density of ternary lithium battery.
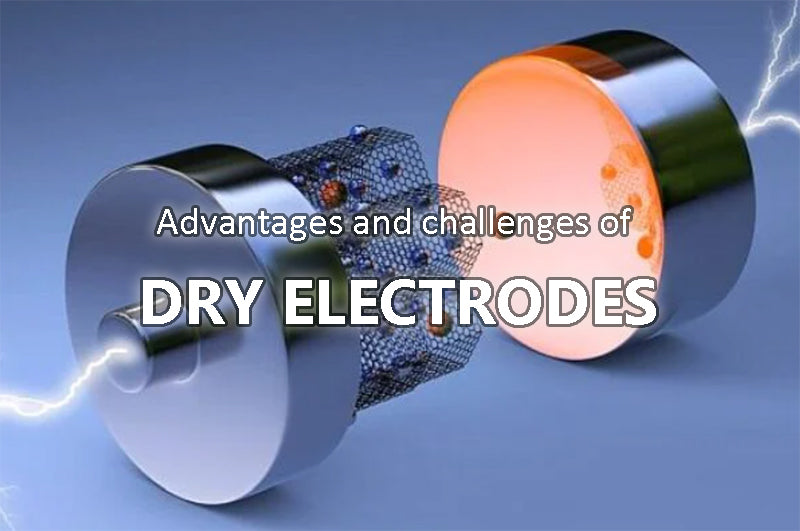
Advantages and challenges of dry electrodes
The main advantages of dry electrode are: first, cost advantage. Coating, drying and solvents in the electrode manufacturing process account for more than 48% of the electrode manufacturing cost. Considering the total material cost and battery manufacturing process, the entire electrode manufacturing coating, drying and solvent recovery steps account for 19.56% of the total cost.
Meanwhile, it improves the performance of the electrode, reduce the porosity of the electrode and effectively increase the thickness of the electrode to increase the energy density of the battery, increase the strength of the electrode, and improve the rate performance of the electrode by reducing the inactive components.
The main challenges faced by dry-process electrodes are as follows: First, the mechanism of binders for dry-process electrodes in different processes has not been fully studied, and the research on binder screening has been accelerated. Different processes should be fully studied, especially the matching of different binders to different materials should be fully demonstrated.
Second, the changes of dry electrodes during long-term cycling have not been fully studied. The evolution of electrodes prepared by the dry method during cycling should be fully understood. Third, the scale production efficiency of dry electrodes needs to be discussed. At present, the uniformity of dry-process electrode mixing and film production in large quantities still need continuous improvement.
Related article: how to clean battery corrosion, lithium ion battery electrolyte, top 10 lithium battery ternary material companies